磨損、腐蝕、斷裂是機(jī)器零部件的三大失效模式,齒輪的失效主要以齒面剝落,點(diǎn)蝕或斷裂等失效形式,其中以斷裂失效的災(zāi)難與損失最大。而斷裂失效又以疲勞斷裂模式所占比例最高。因此,從設(shè)計(jì)、材料、工藝等各方面想辦法提高齒輪的疲勞壽命。齒輪強(qiáng)力噴丸是提高齒輪疲勞壽命的手段之一。
我國(guó)強(qiáng)力噴丸工藝在機(jī)械行業(yè)也是從20世紀(jì)80年代起,特別是近二十年隨著汽車(chē)制造業(yè)的崛起、風(fēng)電發(fā)電工業(yè)的發(fā)展才得以重視,并帶動(dòng)噴丸強(qiáng)化用介質(zhì)、設(shè)備和工藝技術(shù)的發(fā)展。介紹各種強(qiáng)力噴丸的資料不少,但對(duì)18CrNiMo7-6鋼不同硬化層深度下,強(qiáng)力噴丸對(duì)齒輪性能的影響研究不多。本文就強(qiáng)力噴丸對(duì)18CrNiMo7-6鋼不同硬化層深度齒輪的性能影響進(jìn)行研究,為18CrNiMo7-6鋼齒輪強(qiáng)力噴丸提供工藝試驗(yàn)依據(jù)。
1.試驗(yàn)材料和試驗(yàn)方法
試驗(yàn)用18CrNiMo7-6鋼采用電弧爐真空脫氣冶煉,澆注成鋼錠,經(jīng)開(kāi)坯、鍛造撥長(zhǎng),正火加高溫回火預(yù)先熱處理。粗加工后先進(jìn)行調(diào)質(zhì)處理后,分別加工成模數(shù)為6和15.25兩種3齒塊,齒寬為100mm,進(jìn)行滲碳淬火、低溫回火。試樣化學(xué)成分為(wt,%):C0.19,Si0.32,Mn0.72,P0.010,S0.008,Cr1.62,Mo0.28,Ni1.51,H≤2ppm,O≤20ppm,其余為Fe。
18CrNiMo7-6鋼模數(shù)為6齒塊在Aichelin可控氣氛多用爐,隨齒輪零件一起進(jìn)行滲碳直接淬火,滲碳溫度930℃,強(qiáng)滲碳勢(shì)1.10%~1.20%,強(qiáng)滲時(shí)間4.5h,擴(kuò)散碳勢(shì)0.65%~0.75%,擴(kuò)散時(shí)間2.5h,降溫至830℃,保溫0.5h直接在G油中淬火,160~200℃低溫回火5h×2空冷,清理拋丸,滲碳直淬工藝曲線(xiàn)如圖1所示。
18CrNiMo7-6鋼模數(shù)為15.25齒塊在Aichelin可控井式爐滲碳,強(qiáng)滲期碳勢(shì)1.10%~1.20%,擴(kuò)散期碳勢(shì)0.65%~0.75%,進(jìn)行不同時(shí)間滲碳后850℃出爐緩冷;然后在Aichelin可控氣氛多用爐加熱淬火,加熱溫度820~850℃保溫5h后在G油中淬火,160~200℃低溫回火5h×2空冷,清理拋丸。滲碳淬火工藝曲線(xiàn)如圖2所示。
在KXS-226P數(shù)控噴丸機(jī)進(jìn)行強(qiáng)力噴丸,彈丸為S330鑄鋼丸,彈丸直徑0.8~1.0mm,彈丸硬度48~52HRC,用阿爾門(mén)A試片弧高值測(cè)定噴丸強(qiáng)度,弧高值為0.42~0.43mm,進(jìn)行強(qiáng)力噴丸,覆蓋率200%以上。利用HR-150A洛氏硬度計(jì)測(cè)表面硬度,利用FM-700半自動(dòng)顯微硬度計(jì)檢驗(yàn)有效硬化層深度,利用AXIO OBSERVER.AI金相顯微鏡觀察組織,由上海交大材料科學(xué)和工程學(xué)院,利用Proto-iXRD型X射線(xiàn)應(yīng)力儀,Cr-Kσ輻射,1mm準(zhǔn)直管,(211)衍射晶面,X射線(xiàn)彈性常數(shù)-S1=1.28×10-6mm2/N,及S2/2=5.92×10-6mm2/N,測(cè)試執(zhí)行ASTME975-84及GB7704-87標(biāo)準(zhǔn)檢測(cè)齒根表面殘余壓應(yīng)力。
2.試驗(yàn)結(jié)果與討論
18CrNiMo7-6鋼模數(shù)為6齒塊在Aichelin可控氣氛多用爐隨齒輪零件一起進(jìn)行滲碳直接淬火,滲碳溫度930℃,強(qiáng)滲碳勢(shì)1.10%~1.20%,強(qiáng)滲時(shí)間4.5h,擴(kuò)散碳勢(shì)0.65%~0.75%,擴(kuò)散時(shí)間2.5h,降溫至830℃,保溫0.5h直接入光亮淬火油淬火,160~200℃低溫回火5h×2空冷,清理拋丸,在KXS-226P數(shù)控噴丸機(jī)進(jìn)行強(qiáng)力噴丸,噴丸強(qiáng)度為阿爾門(mén)A試片弧高值0.4~0.45mm,表面覆蓋率為200%。
試驗(yàn)結(jié)果:滲碳淬火后滲碳層組織見(jiàn)圖3,為馬氏體和少量殘留奧氏體,硬化層深度為550HV1=1.35mm,強(qiáng)力噴丸前表面硬度59~60HRC,強(qiáng)力噴丸后表面硬度60~61HRC,齒根表面應(yīng)力為-601MPa,見(jiàn)表1。 從表1數(shù)據(jù)可知,18CrNiMo7-6鋼6模數(shù)齒塊經(jīng)滲碳直接淬火低溫回火,強(qiáng)力噴丸后,硬度提高了1~2HRC。
18CrNiMo7-6鋼模數(shù)為15.25齒塊在Aichelin可控井式爐與齒輪零件一起進(jìn)行滲碳,滲碳溫度930℃,強(qiáng)滲碳勢(shì)1.10%~1.20%,強(qiáng)滲時(shí)間H1分別為20h、28h、40h,擴(kuò)散碳勢(shì)0.65%~0.75%,擴(kuò)散時(shí)間H2分別為7h、9h、16h,然后降溫至850℃入緩冷爐,溫度降至600℃以下出爐空冷。在Aichelin可控氣氛多用爐進(jìn)行加熱淬火,加熱溫度為820~850℃,保溫5h入光亮淬火油淬火,160~200℃低溫回火5h×2空冷,清理拋丸,在KXS-226P數(shù)控噴丸機(jī)進(jìn)行強(qiáng)力噴丸,噴丸強(qiáng)度為阿爾門(mén)A試片弧高值0.4~0.45mm,表面覆蓋率為200%。
試驗(yàn)結(jié)果:滲碳淬火后滲碳層組織見(jiàn)圖4,為馬氏體和少量殘留奧氏體,硬化層深度,強(qiáng)力噴丸前表面硬度、強(qiáng)力噴丸后表面硬度,表面應(yīng)力等見(jiàn)表2。從表2數(shù)據(jù)可知,18CrNiMo7-6鋼,15.25模數(shù)齒塊經(jīng)滲碳緩冷,加熱淬火,低溫回火,強(qiáng)力噴丸后,硬度提高了2~3HRC,硬化層深度在550HV1為2.34mm、2.83mm、3.78mm強(qiáng)力噴丸后齒根表面壓應(yīng)力為-720.5MPa、-722MPa、-731.8MPa。
表2 18CrNiMo7-6鋼 模數(shù)15.25齒塊滲碳淬火后金相組織、硬化層深度和強(qiáng)力噴丸前后齒根表面應(yīng)力
從表1和表2數(shù)據(jù)可知,18CrNiMo7-6鋼經(jīng)滲碳淬火低溫回火后,模數(shù)為6齒塊,硬層深度550HV1=1.35mm和模數(shù)為15.25齒塊,硬化層深度為550HV1分別為2.34mm、2.83mm、3.78mm,在相同強(qiáng)力噴丸參數(shù)下噴丸,齒根表面應(yīng)力為壓應(yīng)力,且壓應(yīng)力值不同。m=6齒塊550HV1=1.35mm,齒根表面壓應(yīng)力為-601MPa,m=15.25齒塊, 550HV1=2.34mm,齒根表面壓應(yīng)力為-720.5MPa,550HV1=2.83mm,齒根表面壓應(yīng)力為-722MPa,550HV1=3.78mm,齒根表面壓應(yīng)力為-731.8MPa。模數(shù)為m=15.25,硬化層深度550HV1分別為2.34mm、2.83mm、3.78mm,三種齒塊在相同強(qiáng)力噴丸參數(shù)下噴丸,其齒根表面壓應(yīng)力值比較接近。從表1和表2還可知,18CrNiMo7-6鋼,模數(shù)為m=6齒塊滲碳淬火低溫回火后,硬度層深度550HV1=1.35mm,齒頂硬度為59~60HRC,強(qiáng)力噴丸后齒頂硬度為60~61HRC,模數(shù)為m=15.25齒塊滲碳淬火低溫回火后,硬化層深度為550HV1分別為2.34mm、2.83mm、3.78mm,齒頂硬度為59~60HRC,強(qiáng)力噴丸后齒頂硬度均為61~62HRC。模數(shù)為m=15.25齒塊滲碳淬火低溫回火后,硬化層深度為550HV1分別為2.34mm、2.83mm、3.78mm強(qiáng)力噴丸后,齒頂硬度比模數(shù)為m=6齒塊滲碳淬火低溫回火后,硬度層深度550HV1=1.35mm的齒頂硬度高1HRC。
從表2數(shù)據(jù)還可知,模數(shù)為15.25齒塊滲碳淬火低溫回火后,硬化層深度為550HV1分別為2.34mm、2.83mm、3.78mm,強(qiáng)力噴丸前齒根表面為很小的壓應(yīng)力,分別為-22MPa、25MPa、-27MPa,強(qiáng)力噴丸后齒根表面壓應(yīng)力分別為-720.5MPa、-722MPa、-731.8MPa。強(qiáng)力噴丸后大大提高了齒根表面壓應(yīng)力。因?yàn)閲娡柽^(guò)程就是表層金屬發(fā)生循環(huán)塑性變形的過(guò)程,并產(chǎn)生加工硬化的過(guò)程,從而提高表面硬度。同時(shí)強(qiáng)力噴丸使表面增加殘余壓應(yīng)力。
3.結(jié)語(yǔ)
通過(guò)對(duì)18CrNiMo7-6鋼滲碳淬火低溫回火后,進(jìn)行強(qiáng)力噴丸,強(qiáng)度為阿爾門(mén)A試片弧高值0.4~0.45mm,表面覆蓋率大于200%的強(qiáng)力噴丸工藝試驗(yàn)研究,得出如下結(jié)論:
(1)18CrNiMo7-6鋼模數(shù)為6齒塊,滲碳淬火低溫回火后齒頂硬度為59~60HRC,硬化層深度為1.35mm,強(qiáng)力噴丸后齒頂硬度為60~61HRC,齒頂硬度提高1~2HRC;強(qiáng)力噴丸后,齒根表面為壓應(yīng)力,應(yīng)力為-601MPa。
(2)18CrNiMo7-6鋼模數(shù)為15.25齒塊,滲碳緩冷,加熱淬火低溫回火后,硬度層深度分別為2.34mm、2.83mm、3.78mm,齒頂硬度為59~60HRC;強(qiáng)力噴丸后齒頂硬度為61~62HRC,齒頂硬度提高2~3HRC。
(3)18CrNiMo7-6鋼模數(shù)為15.25齒塊,滲碳緩冷,加熱淬火低溫回火后,硬度層深度分別為2.34mm、2.83mm、3.78mm,測(cè)得齒根表面應(yīng)力為-22MPa、-25MPa、-27MPa,強(qiáng)力噴丸后,測(cè)得齒根表面應(yīng)力分別為-720.5MPa、-722MPa、-731.8MPa。
我國(guó)強(qiáng)力噴丸工藝在機(jī)械行業(yè)也是從20世紀(jì)80年代起,特別是近二十年隨著汽車(chē)制造業(yè)的崛起、風(fēng)電發(fā)電工業(yè)的發(fā)展才得以重視,并帶動(dòng)噴丸強(qiáng)化用介質(zhì)、設(shè)備和工藝技術(shù)的發(fā)展。介紹各種強(qiáng)力噴丸的資料不少,但對(duì)18CrNiMo7-6鋼不同硬化層深度下,強(qiáng)力噴丸對(duì)齒輪性能的影響研究不多。本文就強(qiáng)力噴丸對(duì)18CrNiMo7-6鋼不同硬化層深度齒輪的性能影響進(jìn)行研究,為18CrNiMo7-6鋼齒輪強(qiáng)力噴丸提供工藝試驗(yàn)依據(jù)。
1.試驗(yàn)材料和試驗(yàn)方法
試驗(yàn)用18CrNiMo7-6鋼采用電弧爐真空脫氣冶煉,澆注成鋼錠,經(jīng)開(kāi)坯、鍛造撥長(zhǎng),正火加高溫回火預(yù)先熱處理。粗加工后先進(jìn)行調(diào)質(zhì)處理后,分別加工成模數(shù)為6和15.25兩種3齒塊,齒寬為100mm,進(jìn)行滲碳淬火、低溫回火。試樣化學(xué)成分為(wt,%):C0.19,Si0.32,Mn0.72,P0.010,S0.008,Cr1.62,Mo0.28,Ni1.51,H≤2ppm,O≤20ppm,其余為Fe。
18CrNiMo7-6鋼模數(shù)為6齒塊在Aichelin可控氣氛多用爐,隨齒輪零件一起進(jìn)行滲碳直接淬火,滲碳溫度930℃,強(qiáng)滲碳勢(shì)1.10%~1.20%,強(qiáng)滲時(shí)間4.5h,擴(kuò)散碳勢(shì)0.65%~0.75%,擴(kuò)散時(shí)間2.5h,降溫至830℃,保溫0.5h直接在G油中淬火,160~200℃低溫回火5h×2空冷,清理拋丸,滲碳直淬工藝曲線(xiàn)如圖1所示。
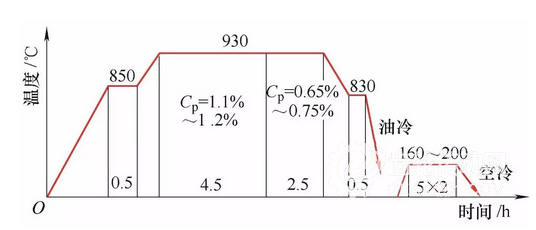
圖1 18CrNiMo7-6 6模數(shù)齒塊滲碳直淬工藝曲線(xiàn)
18CrNiMo7-6鋼模數(shù)為15.25齒塊在Aichelin可控井式爐滲碳,強(qiáng)滲期碳勢(shì)1.10%~1.20%,擴(kuò)散期碳勢(shì)0.65%~0.75%,進(jìn)行不同時(shí)間滲碳后850℃出爐緩冷;然后在Aichelin可控氣氛多用爐加熱淬火,加熱溫度820~850℃保溫5h后在G油中淬火,160~200℃低溫回火5h×2空冷,清理拋丸。滲碳淬火工藝曲線(xiàn)如圖2所示。
在KXS-226P數(shù)控噴丸機(jī)進(jìn)行強(qiáng)力噴丸,彈丸為S330鑄鋼丸,彈丸直徑0.8~1.0mm,彈丸硬度48~52HRC,用阿爾門(mén)A試片弧高值測(cè)定噴丸強(qiáng)度,弧高值為0.42~0.43mm,進(jìn)行強(qiáng)力噴丸,覆蓋率200%以上。利用HR-150A洛氏硬度計(jì)測(cè)表面硬度,利用FM-700半自動(dòng)顯微硬度計(jì)檢驗(yàn)有效硬化層深度,利用AXIO OBSERVER.AI金相顯微鏡觀察組織,由上海交大材料科學(xué)和工程學(xué)院,利用Proto-iXRD型X射線(xiàn)應(yīng)力儀,Cr-Kσ輻射,1mm準(zhǔn)直管,(211)衍射晶面,X射線(xiàn)彈性常數(shù)-S1=1.28×10-6mm2/N,及S2/2=5.92×10-6mm2/N,測(cè)試執(zhí)行ASTME975-84及GB7704-87標(biāo)準(zhǔn)檢測(cè)齒根表面殘余壓應(yīng)力。
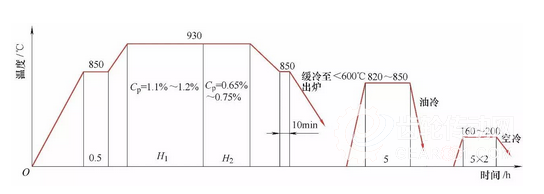
圖2 1818CrNiMo7-6 6模數(shù)齒塊滲碳加熱淬火工藝曲線(xiàn)
2.試驗(yàn)結(jié)果與討論
18CrNiMo7-6鋼模數(shù)為6齒塊在Aichelin可控氣氛多用爐隨齒輪零件一起進(jìn)行滲碳直接淬火,滲碳溫度930℃,強(qiáng)滲碳勢(shì)1.10%~1.20%,強(qiáng)滲時(shí)間4.5h,擴(kuò)散碳勢(shì)0.65%~0.75%,擴(kuò)散時(shí)間2.5h,降溫至830℃,保溫0.5h直接入光亮淬火油淬火,160~200℃低溫回火5h×2空冷,清理拋丸,在KXS-226P數(shù)控噴丸機(jī)進(jìn)行強(qiáng)力噴丸,噴丸強(qiáng)度為阿爾門(mén)A試片弧高值0.4~0.45mm,表面覆蓋率為200%。
試驗(yàn)結(jié)果:滲碳淬火后滲碳層組織見(jiàn)圖3,為馬氏體和少量殘留奧氏體,硬化層深度為550HV1=1.35mm,強(qiáng)力噴丸前表面硬度59~60HRC,強(qiáng)力噴丸后表面硬度60~61HRC,齒根表面應(yīng)力為-601MPa,見(jiàn)表1。 從表1數(shù)據(jù)可知,18CrNiMo7-6鋼6模數(shù)齒塊經(jīng)滲碳直接淬火低溫回火,強(qiáng)力噴丸后,硬度提高了1~2HRC。
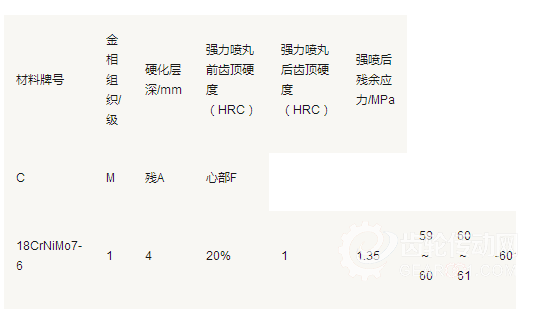
表1 18CrNiMo7-6鋼m=6齒塊滲碳淬火后金相組織、硬化層深和強(qiáng)力噴丸后齒根表面應(yīng)力
18CrNiMo7-6鋼模數(shù)為15.25齒塊在Aichelin可控井式爐與齒輪零件一起進(jìn)行滲碳,滲碳溫度930℃,強(qiáng)滲碳勢(shì)1.10%~1.20%,強(qiáng)滲時(shí)間H1分別為20h、28h、40h,擴(kuò)散碳勢(shì)0.65%~0.75%,擴(kuò)散時(shí)間H2分別為7h、9h、16h,然后降溫至850℃入緩冷爐,溫度降至600℃以下出爐空冷。在Aichelin可控氣氛多用爐進(jìn)行加熱淬火,加熱溫度為820~850℃,保溫5h入光亮淬火油淬火,160~200℃低溫回火5h×2空冷,清理拋丸,在KXS-226P數(shù)控噴丸機(jī)進(jìn)行強(qiáng)力噴丸,噴丸強(qiáng)度為阿爾門(mén)A試片弧高值0.4~0.45mm,表面覆蓋率為200%。
試驗(yàn)結(jié)果:滲碳淬火后滲碳層組織見(jiàn)圖4,為馬氏體和少量殘留奧氏體,硬化層深度,強(qiáng)力噴丸前表面硬度、強(qiáng)力噴丸后表面硬度,表面應(yīng)力等見(jiàn)表2。從表2數(shù)據(jù)可知,18CrNiMo7-6鋼,15.25模數(shù)齒塊經(jīng)滲碳緩冷,加熱淬火,低溫回火,強(qiáng)力噴丸后,硬度提高了2~3HRC,硬化層深度在550HV1為2.34mm、2.83mm、3.78mm強(qiáng)力噴丸后齒根表面壓應(yīng)力為-720.5MPa、-722MPa、-731.8MPa。

圖3 18CrNiMo7-6 模數(shù)為6齒塊滲碳淬火金相組織
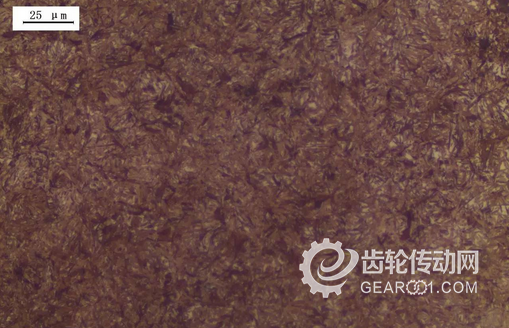
圖4 18CrNiMo7-6 模數(shù)為15.25齒塊滲碳淬火金相組織
表2 18CrNiMo7-6鋼 模數(shù)15.25齒塊滲碳淬火后金相組織、硬化層深度和強(qiáng)力噴丸前后齒根表面應(yīng)力
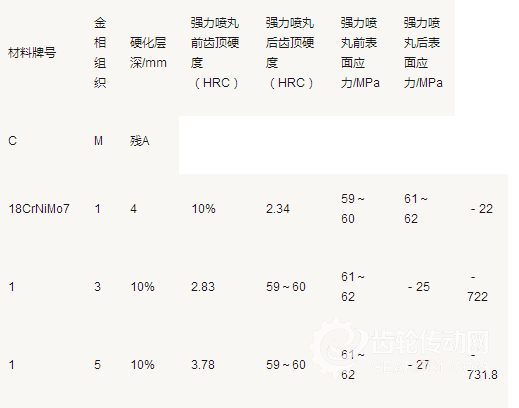
從表1和表2數(shù)據(jù)可知,18CrNiMo7-6鋼經(jīng)滲碳淬火低溫回火后,模數(shù)為6齒塊,硬層深度550HV1=1.35mm和模數(shù)為15.25齒塊,硬化層深度為550HV1分別為2.34mm、2.83mm、3.78mm,在相同強(qiáng)力噴丸參數(shù)下噴丸,齒根表面應(yīng)力為壓應(yīng)力,且壓應(yīng)力值不同。m=6齒塊550HV1=1.35mm,齒根表面壓應(yīng)力為-601MPa,m=15.25齒塊, 550HV1=2.34mm,齒根表面壓應(yīng)力為-720.5MPa,550HV1=2.83mm,齒根表面壓應(yīng)力為-722MPa,550HV1=3.78mm,齒根表面壓應(yīng)力為-731.8MPa。模數(shù)為m=15.25,硬化層深度550HV1分別為2.34mm、2.83mm、3.78mm,三種齒塊在相同強(qiáng)力噴丸參數(shù)下噴丸,其齒根表面壓應(yīng)力值比較接近。從表1和表2還可知,18CrNiMo7-6鋼,模數(shù)為m=6齒塊滲碳淬火低溫回火后,硬度層深度550HV1=1.35mm,齒頂硬度為59~60HRC,強(qiáng)力噴丸后齒頂硬度為60~61HRC,模數(shù)為m=15.25齒塊滲碳淬火低溫回火后,硬化層深度為550HV1分別為2.34mm、2.83mm、3.78mm,齒頂硬度為59~60HRC,強(qiáng)力噴丸后齒頂硬度均為61~62HRC。模數(shù)為m=15.25齒塊滲碳淬火低溫回火后,硬化層深度為550HV1分別為2.34mm、2.83mm、3.78mm強(qiáng)力噴丸后,齒頂硬度比模數(shù)為m=6齒塊滲碳淬火低溫回火后,硬度層深度550HV1=1.35mm的齒頂硬度高1HRC。
從表2數(shù)據(jù)還可知,模數(shù)為15.25齒塊滲碳淬火低溫回火后,硬化層深度為550HV1分別為2.34mm、2.83mm、3.78mm,強(qiáng)力噴丸前齒根表面為很小的壓應(yīng)力,分別為-22MPa、25MPa、-27MPa,強(qiáng)力噴丸后齒根表面壓應(yīng)力分別為-720.5MPa、-722MPa、-731.8MPa。強(qiáng)力噴丸后大大提高了齒根表面壓應(yīng)力。因?yàn)閲娡柽^(guò)程就是表層金屬發(fā)生循環(huán)塑性變形的過(guò)程,并產(chǎn)生加工硬化的過(guò)程,從而提高表面硬度。同時(shí)強(qiáng)力噴丸使表面增加殘余壓應(yīng)力。
3.結(jié)語(yǔ)
通過(guò)對(duì)18CrNiMo7-6鋼滲碳淬火低溫回火后,進(jìn)行強(qiáng)力噴丸,強(qiáng)度為阿爾門(mén)A試片弧高值0.4~0.45mm,表面覆蓋率大于200%的強(qiáng)力噴丸工藝試驗(yàn)研究,得出如下結(jié)論:
(1)18CrNiMo7-6鋼模數(shù)為6齒塊,滲碳淬火低溫回火后齒頂硬度為59~60HRC,硬化層深度為1.35mm,強(qiáng)力噴丸后齒頂硬度為60~61HRC,齒頂硬度提高1~2HRC;強(qiáng)力噴丸后,齒根表面為壓應(yīng)力,應(yīng)力為-601MPa。
(2)18CrNiMo7-6鋼模數(shù)為15.25齒塊,滲碳緩冷,加熱淬火低溫回火后,硬度層深度分別為2.34mm、2.83mm、3.78mm,齒頂硬度為59~60HRC;強(qiáng)力噴丸后齒頂硬度為61~62HRC,齒頂硬度提高2~3HRC。
(3)18CrNiMo7-6鋼模數(shù)為15.25齒塊,滲碳緩冷,加熱淬火低溫回火后,硬度層深度分別為2.34mm、2.83mm、3.78mm,測(cè)得齒根表面應(yīng)力為-22MPa、-25MPa、-27MPa,強(qiáng)力噴丸后,測(cè)得齒根表面應(yīng)力分別為-720.5MPa、-722MPa、-731.8MPa。