2019 年 4 月 23 日,格平根 - 對(duì)更高能源效率的需求以及對(duì)新能源汽車的不斷探索是該行業(yè)的主要?jiǎng)?chuàng)新驅(qū)動(dòng)力。舒勒為電動(dòng)汽車電機(jī)與電池殼體的制造提供多種解決方案。近期,舒勒系統(tǒng)業(yè)務(wù)部在德國(guó)格平根總部展示了最新研發(fā)的用于自扣電動(dòng)機(jī)鐵芯生產(chǎn)的高速?zèng)_Smartlin EV3.8,同時(shí)舒勒在中國(guó)大連的工廠也生產(chǎn)該設(shè)備,并提供與電動(dòng)汽車相關(guān)的其他解決方案。
沖片幾何形狀越來越復(fù)雜
舒勒技術(shù)日活動(dòng)的參與者超過了 50 人。舒勒的 Simon Schmidt先生表示,電動(dòng)汽車現(xiàn)在發(fā)展迅猛,汽車制造商紛紛加碼電動(dòng)汽車產(chǎn)業(yè)。為了獲得更高的電動(dòng)機(jī)效率,電動(dòng)機(jī)沖片的幾何形狀變得越來越復(fù)雜,因此加工所需的模具長(zhǎng)度也變得越來越長(zhǎng):“使用雙排模具進(jìn)行加工是目前十分先進(jìn)的技術(shù)。舒勒最新的高速?zèng)_ Smartline EV 3.8 工作臺(tái)長(zhǎng)度從 2.7 米增加至 3.7 米,能夠加工最寬 630 mm 的帶料。”
同時(shí),材料厚度也減少到了 0.35 mm 甚至 0.2 mm。“按照汽車行業(yè)對(duì)于電動(dòng)汽車的新要求,目前的沖片厚度定義在 0.25 mm 到 0.275 mm。因此,壓力機(jī)供應(yīng)商必須確保滑塊與工作臺(tái)擁有精準(zhǔn)的定位與平行度。”對(duì)此,舒勒早在 15 年前就開發(fā)出了一套沖裁深度控制裝置 (PDC),能夠提供完美的滑塊定位與位置重復(fù)精度。“通過該裝置我們可以保證對(duì)材料進(jìn)行精準(zhǔn)沖裁,從而實(shí)現(xiàn)精準(zhǔn)的模內(nèi)自扣。舒勒的 Smartline 系列設(shè)備能夠在所有沖裁速度下以 +/-0.01 mm 的精度調(diào)節(jié)滑塊下死點(diǎn)位置。”
Smartline EV3.8 所配備的 3.7 米長(zhǎng)滑塊為設(shè)備的設(shè)計(jì)帶來了很多挑戰(zhàn)。“對(duì)于小尺寸的 Smartline 設(shè)備,我們?cè)眉す鉁y(cè)量滑塊的下降深度,設(shè)備會(huì)對(duì)沖裁深度進(jìn)行校正,必要時(shí)每個(gè)行程都會(huì)自動(dòng)校正。”但是對(duì)于 3.7 m 長(zhǎng)的滑塊,就必須要考慮到撓度問題。”現(xiàn)在,舒勒在高級(jí)版 的沖裁深度控制系統(tǒng)中,我們把一個(gè)應(yīng)變儀安裝到模具的沖頭架里,用來代替激光測(cè)量:“從而可以保持壓力恒定,并可以控制滑塊的撓度。無論沖片的形狀如何,都能夠獲得完美的定子和轉(zhuǎn)子疊壓效果。”
舒勒的目標(biāo)是憑借 180 年的壓力機(jī)制造經(jīng)驗(yàn),為客戶提供可靠、耐用且高精度的設(shè)備。 Schmidt 先生說道,“我們的設(shè)備能夠以每分鐘 250 沖次的速度全速運(yùn)行,壓力最高可達(dá) 3150 kN,上模最大重量達(dá) 6 噸。”壓力機(jī)動(dòng)態(tài)與靜態(tài)平衡度高,無需特殊的基坑:客戶僅需保證基坑的靜態(tài)承重達(dá)到 110 噸即可。“由于動(dòng)態(tài)與靜態(tài)平衡度高,壓力機(jī)在全速運(yùn)行的情況下,在垂直方向的位移小于 1mm。”因此,滑塊導(dǎo)軌、壓力點(diǎn)、連桿以及主軸承上沒有易損件,最大程度地降低了維護(hù)成本。
盡管壓力機(jī)的體積和質(zhì)量都很大,舒勒僅使用了兩個(gè)承壓點(diǎn),而非三個(gè):“我們想要確切知道每個(gè)壓力點(diǎn)上的壓力,并確??梢詸z測(cè)到該壓力。當(dāng)有三個(gè)承壓點(diǎn)時(shí),總會(huì)出現(xiàn)較小的偏差,最終出現(xiàn)磨損以及故障只是時(shí)間問題。采用兩個(gè)承壓點(diǎn)時(shí),預(yù)定義的壓力就會(huì)達(dá)到協(xié)調(diào)狀態(tài),從而將磨損降至最小。同時(shí)還能實(shí)現(xiàn)滑塊的高平行度:我們能夠保證從左到右每米的平行度為 0.04 mm。”
得益于 Smartline EV 3.8 采用的高級(jí)版 PDC、雙壓力點(diǎn)設(shè)計(jì)、四個(gè)預(yù)張緊滑塊導(dǎo)軌以及完美的靜態(tài)與動(dòng)態(tài)平衡,模具的壽命能夠延長(zhǎng) 30%。
模具生命周期內(nèi)完成 1.8 億沖次
“對(duì)于高速鋼材料,在模具生命周期內(nèi)能夠完成約 500 萬沖次,”模具制造商 AWBEA 的 Daniel Kittig 說道。“對(duì)于粉末冶金材料,能夠?qū)崿F(xiàn) 3000 萬沖次,而對(duì)于碳化合金,則能夠?qū)崿F(xiàn)約 1.8 億沖次,具體取決于工藝條件與材料特性。”在大多數(shù)情況下,AWEBA 的模具工程師首先與客戶溝通,了解客戶的想法。“基于此,我們開始進(jìn)行設(shè)計(jì),同時(shí)考量部件的幾何形狀、尺寸、復(fù)雜度以及公差。”
客戶要生產(chǎn)的沖片數(shù)量是決定采用單排、雙排或多排模具的主要因素,但這也取決于壓力機(jī)的性能:“我們的目標(biāo)是為客戶提供最大程度的靈活性。即可以對(duì)工藝和材料問題導(dǎo)致的偏差和變化做出響應(yīng)。因此我們集成了可調(diào)節(jié)嵌入功能。”
每個(gè)模具都采用獨(dú)立的設(shè)計(jì)。通常,首先通過模具進(jìn)行預(yù)切割,以降低帶料的張力。接下來,逐步切割轉(zhuǎn)子的形狀,在這個(gè)過程中可能需要使用多個(gè)不同的工位。“如果僅使用一兩個(gè)工位,幾何形狀就會(huì)不太穩(wěn)定。”Kittig 解釋道。
在之后的工位中,通過氣動(dòng)沖裁對(duì)自扣操作進(jìn)行分片。用于沖片自扣的壓印可以在近軸孔處、成型模之間或近直徑處進(jìn)行:“我們也會(huì)在設(shè)計(jì)中使用黏膠工藝。”
“由于客戶的期待產(chǎn)量會(huì)越來越高,我們還采用了雙排和多排布局,完美適配舒勒的 EV 3.8 壓力機(jī),”Kittig 說道。“這樣會(huì)獲得更高的材料利用率。”他說制造這種長(zhǎng)度和精度的模具即使對(duì)于 AWEBA 也是一個(gè)巨大的挑戰(zhàn):“整個(gè)模具的精度需要控制在幾微米內(nèi)。”
降低電池殼體的制造成本
電池是導(dǎo)致電動(dòng)汽車比燃油汽車價(jià)格更高的主要原因。但是,從現(xiàn)在的發(fā)展規(guī)模來看,到 2026 年左右這一情況將會(huì)發(fā)生改變:彭博公布的統(tǒng)計(jì)數(shù)據(jù)顯示,相比 2018 年電池占到總成本的 42%,到那時(shí),這一比例將會(huì)降到 24%,電動(dòng)汽車將比燃油汽車更具經(jīng)濟(jì)性。
“對(duì)于現(xiàn)今的電動(dòng)汽車市場(chǎng),鋰離子電池的總需求量為 120 GWH,”舒勒的 Rainer Berkefeld 說道。“而到 2022 年,需求量將會(huì)超過 400 GWH,大約相當(dāng)于需要制造 10 億個(gè)電池殼體。”根據(jù) fka 與 Roland Berger 的數(shù)據(jù)顯示,在 2016 年至 2021 年之間,中國(guó)的電動(dòng)汽車電池產(chǎn)能需求為 178 GWH,韓國(guó)為 98 GWH,日本為 87 GWH,美國(guó)為 74 GWH,德國(guó)為 18 GWH。
目前,市場(chǎng)上超過半數(shù)的電池采用圓柱形電池殼體(如特斯拉的電動(dòng)汽車)或方形電池殼體(如豐田、三菱、本田、寶馬、大眾、奧迪、克萊斯勒、比亞迪、福特等廠商所采用的電池)。雖然圓柱形電池價(jià)格更低且商品化更成熟,但是需要復(fù)雜的電池管理系統(tǒng)。而方形電池則具有最佳的可擴(kuò)展性,循環(huán)壽命更長(zhǎng),但是生產(chǎn)成本仍然很高。
“舒勒已開發(fā)出了一種全自動(dòng)方形電池生產(chǎn)線,比目前的解決方案生產(chǎn)速度快 5 倍,同時(shí)還更節(jié)省材料,”Berkefeld先生 說道,“采用的是標(biāo)準(zhǔn)化設(shè)備以及在全球汽車和包裝行業(yè)普遍采用的成熟技術(shù)。”原材料采用鋁材料塊通過沖擊擠壓制成。當(dāng)沖頭擠壓料塊時(shí),材料會(huì)向相反方向流動(dòng)。
之后,從兩側(cè)掃描預(yù)成形件,以檢測(cè)裂縫或變形。超出規(guī)格的產(chǎn)品將會(huì)被移除,以防在接下來的工藝中導(dǎo)致停機(jī)。在下一個(gè)步驟中,預(yù)成形件將會(huì)通過四個(gè)通道進(jìn)入到一臺(tái) 300 噸后處理壓力機(jī)的一模四件模具中。除了變薄拉伸外,還可以集成精沖或整形校準(zhǔn)等功能。
然后,將殼體倒置在切邊機(jī)中。剪切頭從內(nèi)到外以擺動(dòng)的方式工作,避免內(nèi)部出現(xiàn)毛刺。在進(jìn)行清洗、干燥與通過視像檢測(cè)后,就可以進(jìn)行使用了。這臺(tái)高速?zèng)_設(shè)備目前已在一家大型電池制造商的工廠中投入使用,每年能夠生產(chǎn)超過 3000 萬個(gè)電池殼體。
舒勒同時(shí)也提供用于制造電池蓋的沖裁壓力機(jī)。它采用級(jí)進(jìn)模,包含 12 個(gè)成形工位,如沖孔、切邊、壓印與分片等。
Internet
網(wǎng)站
www.schulergroup.com/drives_generators
www.schulergroup.com/battery
圖片注釋
關(guān)于舒勒集團(tuán) – www.schulergroup.com
舒勒為客戶提供從聯(lián)網(wǎng)壓力機(jī)到?jīng)_壓車間規(guī)劃的先進(jìn)成形技術(shù)。除壓力機(jī)外,舒勒的產(chǎn)品范圍還包括面向整個(gè)金屬加工行業(yè)的自動(dòng)化與軟件解決方案、模具、工藝技術(shù)以及相關(guān)服務(wù)。舒勒的客戶不僅包括汽車制造商及零部件供應(yīng)商,還包括來自鍛造、家用電器和電子工業(yè)等諸多行業(yè)的公司。舒勒的壓力機(jī)為全球超過 180 個(gè)國(guó)家生產(chǎn)硬幣。作為創(chuàng)新系統(tǒng)解決方案供應(yīng)商,我們也向全球客戶提供成形技術(shù)相關(guān)的數(shù)字化改造服務(wù)。2018 財(cái)年舒勒銷售額達(dá)到 12.12 億歐元。舒勒股份公司成立于 1839 年,總部位于德國(guó)格平根,在歐洲、中國(guó)、美國(guó)等全球 40 多個(gè)國(guó)家和地區(qū)的員工總數(shù)約為 6600 人。奧地利的安德里茨集團(tuán)持有舒勒的多數(shù)股權(quán)。
沖片幾何形狀越來越復(fù)雜
舒勒技術(shù)日活動(dòng)的參與者超過了 50 人。舒勒的 Simon Schmidt先生表示,電動(dòng)汽車現(xiàn)在發(fā)展迅猛,汽車制造商紛紛加碼電動(dòng)汽車產(chǎn)業(yè)。為了獲得更高的電動(dòng)機(jī)效率,電動(dòng)機(jī)沖片的幾何形狀變得越來越復(fù)雜,因此加工所需的模具長(zhǎng)度也變得越來越長(zhǎng):“使用雙排模具進(jìn)行加工是目前十分先進(jìn)的技術(shù)。舒勒最新的高速?zèng)_ Smartline EV 3.8 工作臺(tái)長(zhǎng)度從 2.7 米增加至 3.7 米,能夠加工最寬 630 mm 的帶料。”
同時(shí),材料厚度也減少到了 0.35 mm 甚至 0.2 mm。“按照汽車行業(yè)對(duì)于電動(dòng)汽車的新要求,目前的沖片厚度定義在 0.25 mm 到 0.275 mm。因此,壓力機(jī)供應(yīng)商必須確保滑塊與工作臺(tái)擁有精準(zhǔn)的定位與平行度。”對(duì)此,舒勒早在 15 年前就開發(fā)出了一套沖裁深度控制裝置 (PDC),能夠提供完美的滑塊定位與位置重復(fù)精度。“通過該裝置我們可以保證對(duì)材料進(jìn)行精準(zhǔn)沖裁,從而實(shí)現(xiàn)精準(zhǔn)的模內(nèi)自扣。舒勒的 Smartline 系列設(shè)備能夠在所有沖裁速度下以 +/-0.01 mm 的精度調(diào)節(jié)滑塊下死點(diǎn)位置。”
Smartline EV3.8 所配備的 3.7 米長(zhǎng)滑塊為設(shè)備的設(shè)計(jì)帶來了很多挑戰(zhàn)。“對(duì)于小尺寸的 Smartline 設(shè)備,我們?cè)眉す鉁y(cè)量滑塊的下降深度,設(shè)備會(huì)對(duì)沖裁深度進(jìn)行校正,必要時(shí)每個(gè)行程都會(huì)自動(dòng)校正。”但是對(duì)于 3.7 m 長(zhǎng)的滑塊,就必須要考慮到撓度問題。”現(xiàn)在,舒勒在高級(jí)版 的沖裁深度控制系統(tǒng)中,我們把一個(gè)應(yīng)變儀安裝到模具的沖頭架里,用來代替激光測(cè)量:“從而可以保持壓力恒定,并可以控制滑塊的撓度。無論沖片的形狀如何,都能夠獲得完美的定子和轉(zhuǎn)子疊壓效果。”
舒勒的目標(biāo)是憑借 180 年的壓力機(jī)制造經(jīng)驗(yàn),為客戶提供可靠、耐用且高精度的設(shè)備。 Schmidt 先生說道,“我們的設(shè)備能夠以每分鐘 250 沖次的速度全速運(yùn)行,壓力最高可達(dá) 3150 kN,上模最大重量達(dá) 6 噸。”壓力機(jī)動(dòng)態(tài)與靜態(tài)平衡度高,無需特殊的基坑:客戶僅需保證基坑的靜態(tài)承重達(dá)到 110 噸即可。“由于動(dòng)態(tài)與靜態(tài)平衡度高,壓力機(jī)在全速運(yùn)行的情況下,在垂直方向的位移小于 1mm。”因此,滑塊導(dǎo)軌、壓力點(diǎn)、連桿以及主軸承上沒有易損件,最大程度地降低了維護(hù)成本。
盡管壓力機(jī)的體積和質(zhì)量都很大,舒勒僅使用了兩個(gè)承壓點(diǎn),而非三個(gè):“我們想要確切知道每個(gè)壓力點(diǎn)上的壓力,并確??梢詸z測(cè)到該壓力。當(dāng)有三個(gè)承壓點(diǎn)時(shí),總會(huì)出現(xiàn)較小的偏差,最終出現(xiàn)磨損以及故障只是時(shí)間問題。采用兩個(gè)承壓點(diǎn)時(shí),預(yù)定義的壓力就會(huì)達(dá)到協(xié)調(diào)狀態(tài),從而將磨損降至最小。同時(shí)還能實(shí)現(xiàn)滑塊的高平行度:我們能夠保證從左到右每米的平行度為 0.04 mm。”
得益于 Smartline EV 3.8 采用的高級(jí)版 PDC、雙壓力點(diǎn)設(shè)計(jì)、四個(gè)預(yù)張緊滑塊導(dǎo)軌以及完美的靜態(tài)與動(dòng)態(tài)平衡,模具的壽命能夠延長(zhǎng) 30%。
模具生命周期內(nèi)完成 1.8 億沖次
“對(duì)于高速鋼材料,在模具生命周期內(nèi)能夠完成約 500 萬沖次,”模具制造商 AWBEA 的 Daniel Kittig 說道。“對(duì)于粉末冶金材料,能夠?qū)崿F(xiàn) 3000 萬沖次,而對(duì)于碳化合金,則能夠?qū)崿F(xiàn)約 1.8 億沖次,具體取決于工藝條件與材料特性。”在大多數(shù)情況下,AWEBA 的模具工程師首先與客戶溝通,了解客戶的想法。“基于此,我們開始進(jìn)行設(shè)計(jì),同時(shí)考量部件的幾何形狀、尺寸、復(fù)雜度以及公差。”
客戶要生產(chǎn)的沖片數(shù)量是決定采用單排、雙排或多排模具的主要因素,但這也取決于壓力機(jī)的性能:“我們的目標(biāo)是為客戶提供最大程度的靈活性。即可以對(duì)工藝和材料問題導(dǎo)致的偏差和變化做出響應(yīng)。因此我們集成了可調(diào)節(jié)嵌入功能。”
每個(gè)模具都采用獨(dú)立的設(shè)計(jì)。通常,首先通過模具進(jìn)行預(yù)切割,以降低帶料的張力。接下來,逐步切割轉(zhuǎn)子的形狀,在這個(gè)過程中可能需要使用多個(gè)不同的工位。“如果僅使用一兩個(gè)工位,幾何形狀就會(huì)不太穩(wěn)定。”Kittig 解釋道。
在之后的工位中,通過氣動(dòng)沖裁對(duì)自扣操作進(jìn)行分片。用于沖片自扣的壓印可以在近軸孔處、成型模之間或近直徑處進(jìn)行:“我們也會(huì)在設(shè)計(jì)中使用黏膠工藝。”
“由于客戶的期待產(chǎn)量會(huì)越來越高,我們還采用了雙排和多排布局,完美適配舒勒的 EV 3.8 壓力機(jī),”Kittig 說道。“這樣會(huì)獲得更高的材料利用率。”他說制造這種長(zhǎng)度和精度的模具即使對(duì)于 AWEBA 也是一個(gè)巨大的挑戰(zhàn):“整個(gè)模具的精度需要控制在幾微米內(nèi)。”
降低電池殼體的制造成本
電池是導(dǎo)致電動(dòng)汽車比燃油汽車價(jià)格更高的主要原因。但是,從現(xiàn)在的發(fā)展規(guī)模來看,到 2026 年左右這一情況將會(huì)發(fā)生改變:彭博公布的統(tǒng)計(jì)數(shù)據(jù)顯示,相比 2018 年電池占到總成本的 42%,到那時(shí),這一比例將會(huì)降到 24%,電動(dòng)汽車將比燃油汽車更具經(jīng)濟(jì)性。
“對(duì)于現(xiàn)今的電動(dòng)汽車市場(chǎng),鋰離子電池的總需求量為 120 GWH,”舒勒的 Rainer Berkefeld 說道。“而到 2022 年,需求量將會(huì)超過 400 GWH,大約相當(dāng)于需要制造 10 億個(gè)電池殼體。”根據(jù) fka 與 Roland Berger 的數(shù)據(jù)顯示,在 2016 年至 2021 年之間,中國(guó)的電動(dòng)汽車電池產(chǎn)能需求為 178 GWH,韓國(guó)為 98 GWH,日本為 87 GWH,美國(guó)為 74 GWH,德國(guó)為 18 GWH。
目前,市場(chǎng)上超過半數(shù)的電池采用圓柱形電池殼體(如特斯拉的電動(dòng)汽車)或方形電池殼體(如豐田、三菱、本田、寶馬、大眾、奧迪、克萊斯勒、比亞迪、福特等廠商所采用的電池)。雖然圓柱形電池價(jià)格更低且商品化更成熟,但是需要復(fù)雜的電池管理系統(tǒng)。而方形電池則具有最佳的可擴(kuò)展性,循環(huán)壽命更長(zhǎng),但是生產(chǎn)成本仍然很高。
“舒勒已開發(fā)出了一種全自動(dòng)方形電池生產(chǎn)線,比目前的解決方案生產(chǎn)速度快 5 倍,同時(shí)還更節(jié)省材料,”Berkefeld先生 說道,“采用的是標(biāo)準(zhǔn)化設(shè)備以及在全球汽車和包裝行業(yè)普遍采用的成熟技術(shù)。”原材料采用鋁材料塊通過沖擊擠壓制成。當(dāng)沖頭擠壓料塊時(shí),材料會(huì)向相反方向流動(dòng)。
之后,從兩側(cè)掃描預(yù)成形件,以檢測(cè)裂縫或變形。超出規(guī)格的產(chǎn)品將會(huì)被移除,以防在接下來的工藝中導(dǎo)致停機(jī)。在下一個(gè)步驟中,預(yù)成形件將會(huì)通過四個(gè)通道進(jìn)入到一臺(tái) 300 噸后處理壓力機(jī)的一模四件模具中。除了變薄拉伸外,還可以集成精沖或整形校準(zhǔn)等功能。
然后,將殼體倒置在切邊機(jī)中。剪切頭從內(nèi)到外以擺動(dòng)的方式工作,避免內(nèi)部出現(xiàn)毛刺。在進(jìn)行清洗、干燥與通過視像檢測(cè)后,就可以進(jìn)行使用了。這臺(tái)高速?zèng)_設(shè)備目前已在一家大型電池制造商的工廠中投入使用,每年能夠生產(chǎn)超過 3000 萬個(gè)電池殼體。
舒勒同時(shí)也提供用于制造電池蓋的沖裁壓力機(jī)。它采用級(jí)進(jìn)模,包含 12 個(gè)成形工位,如沖孔、切邊、壓印與分片等。
Internet
網(wǎng)站
www.schulergroup.com/drives_generators
www.schulergroup.com/battery
圖片注釋
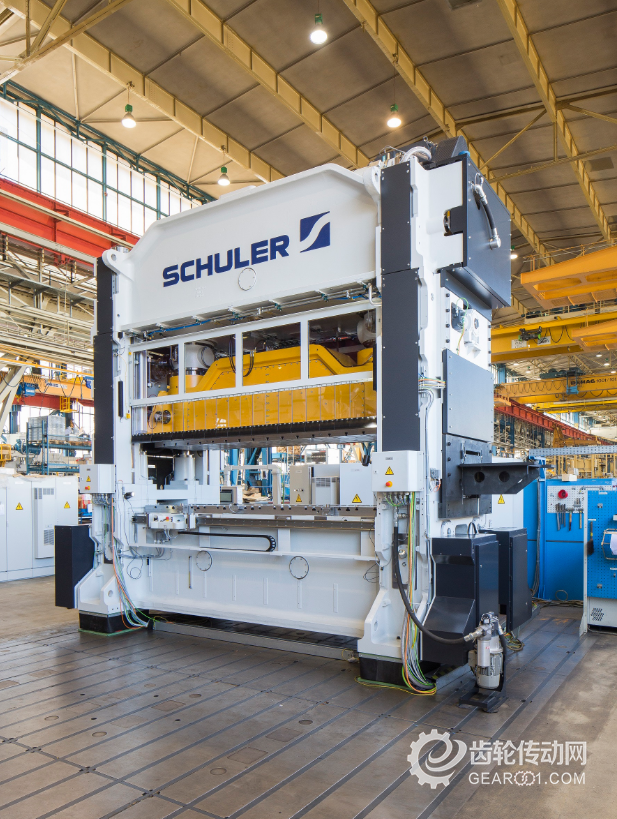
圖1: 舒勒在德國(guó)格平根總部展示了最新研發(fā)的高速?zèng)_ Smartline EV 3.8。
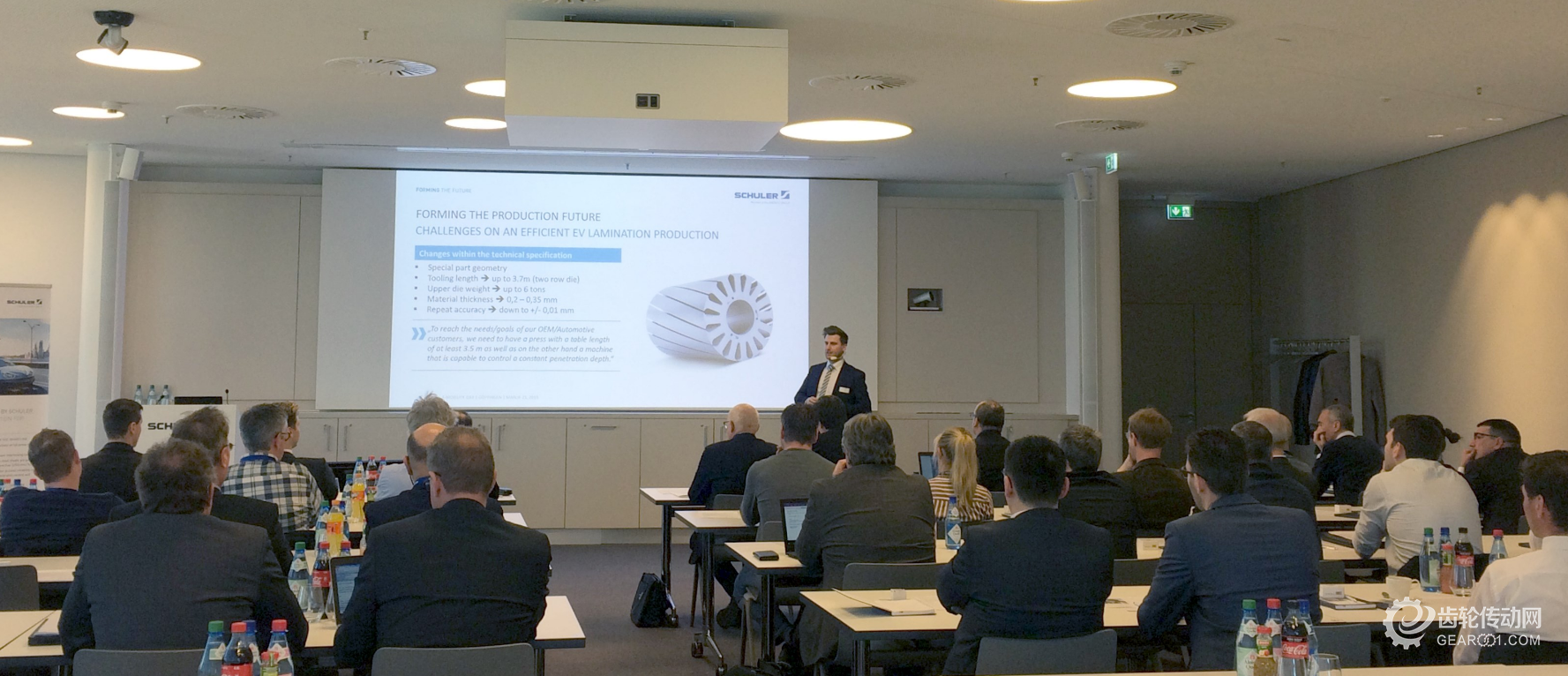
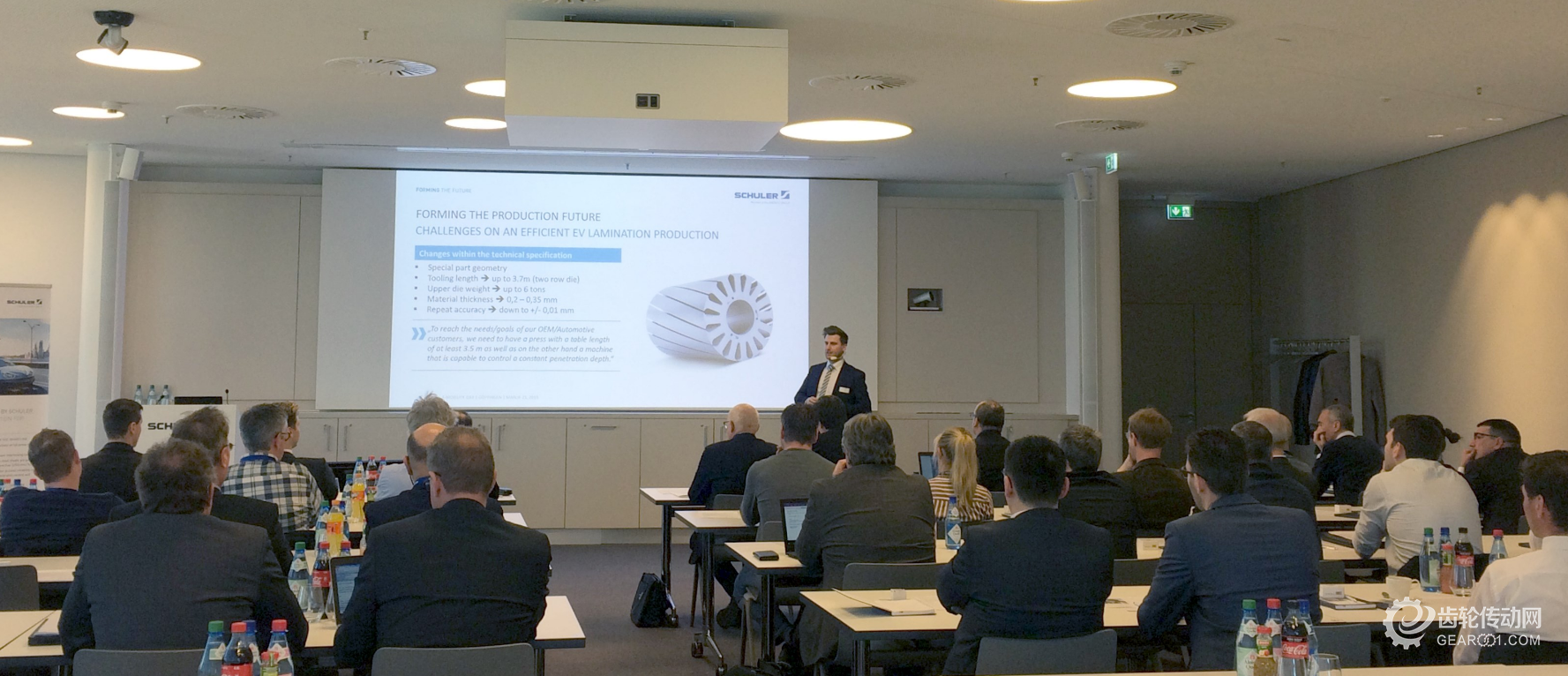
圖2: “舒勒最新的高速?zèng)_ Smartline EV 3.8 的工作臺(tái)長(zhǎng)度從 2.7 米增加至 3.7 米,能夠加工最寬 630 mm 的帶料。”舒勒 Simon Schmidt 說道。
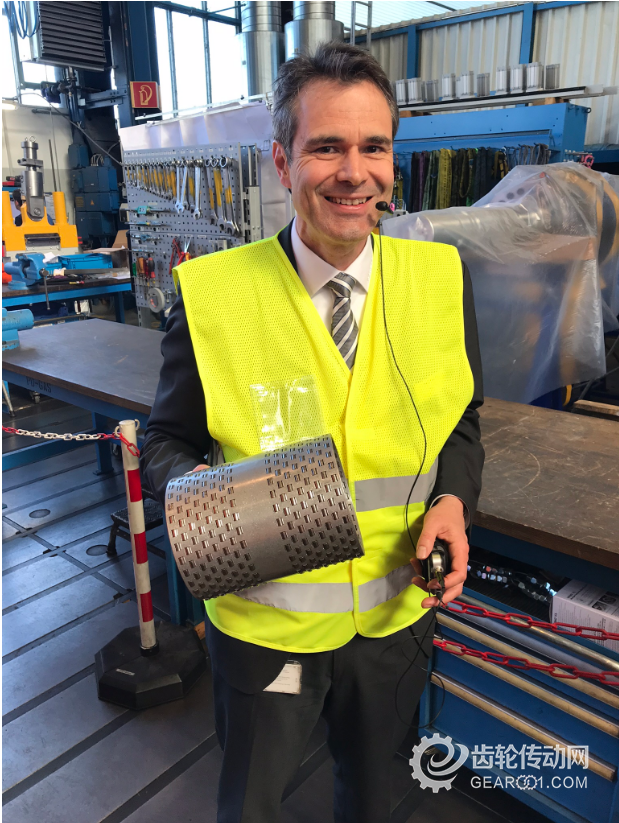
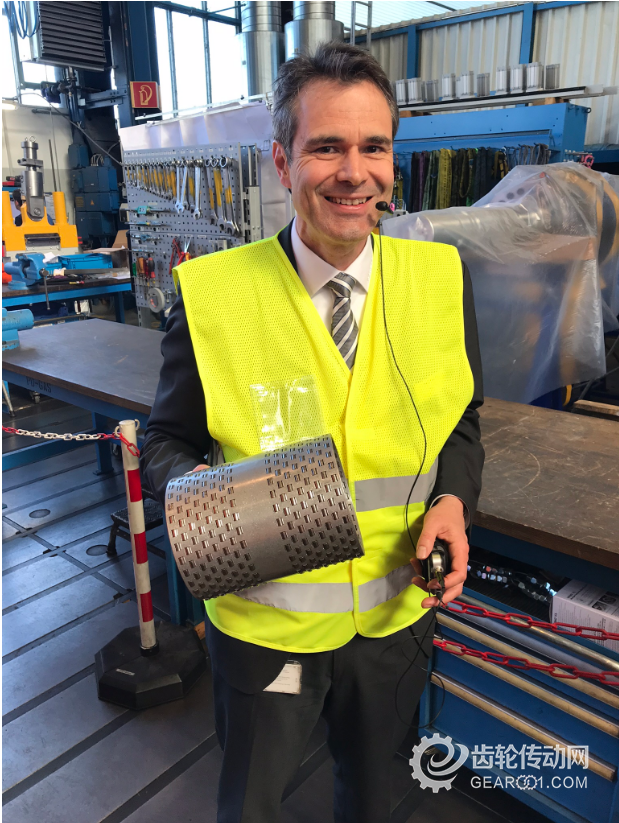
圖3: 舒勒電動(dòng)汽車相關(guān)業(yè)務(wù)負(fù)責(zé)人 Markus Roever先生 在展示內(nèi)部有上千個(gè)輥?zhàn)拥幕瑝K導(dǎo)軌。
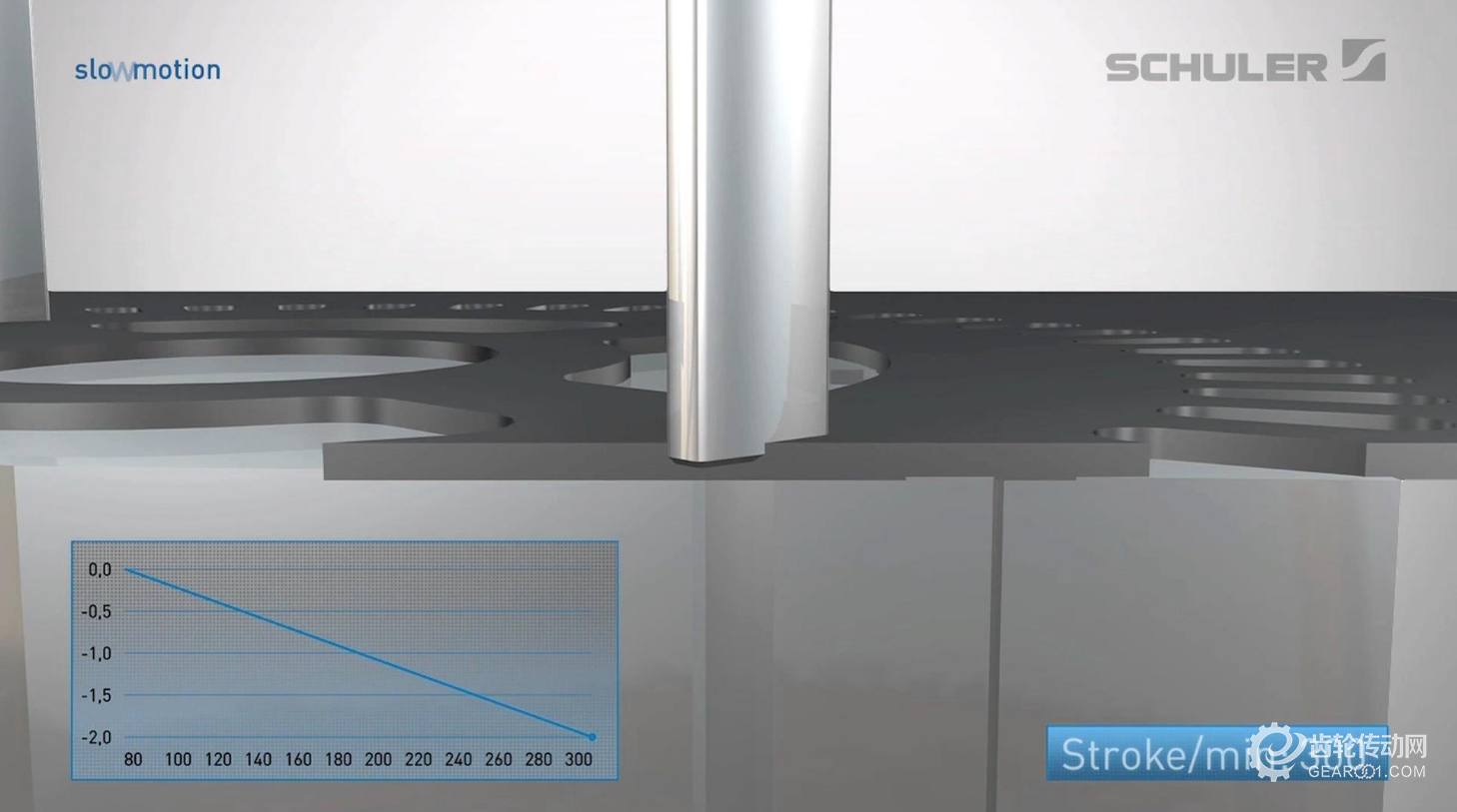
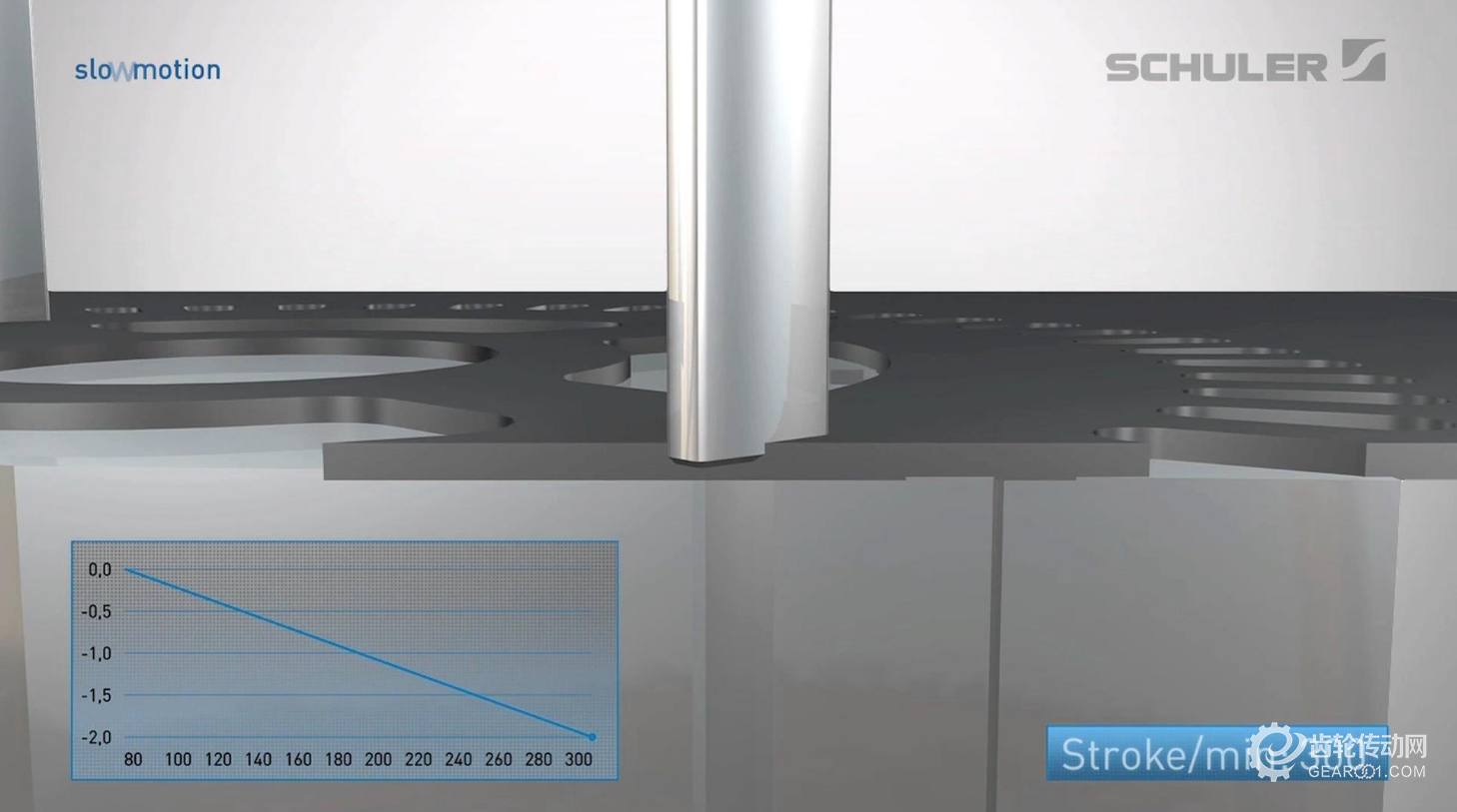
圖4: 舒勒開發(fā)出了一套沖裁深度控制裝置 (PDC),保證了滑塊相對(duì)于工作臺(tái)的重復(fù)位置精度。
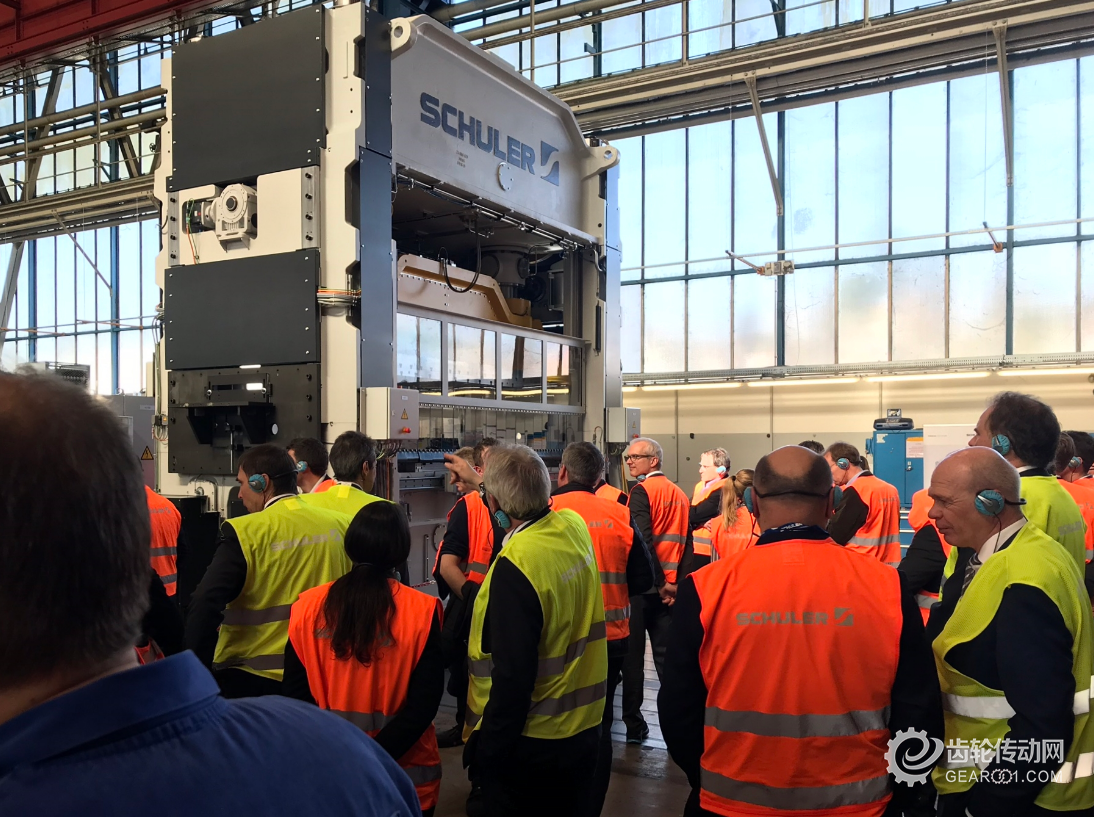
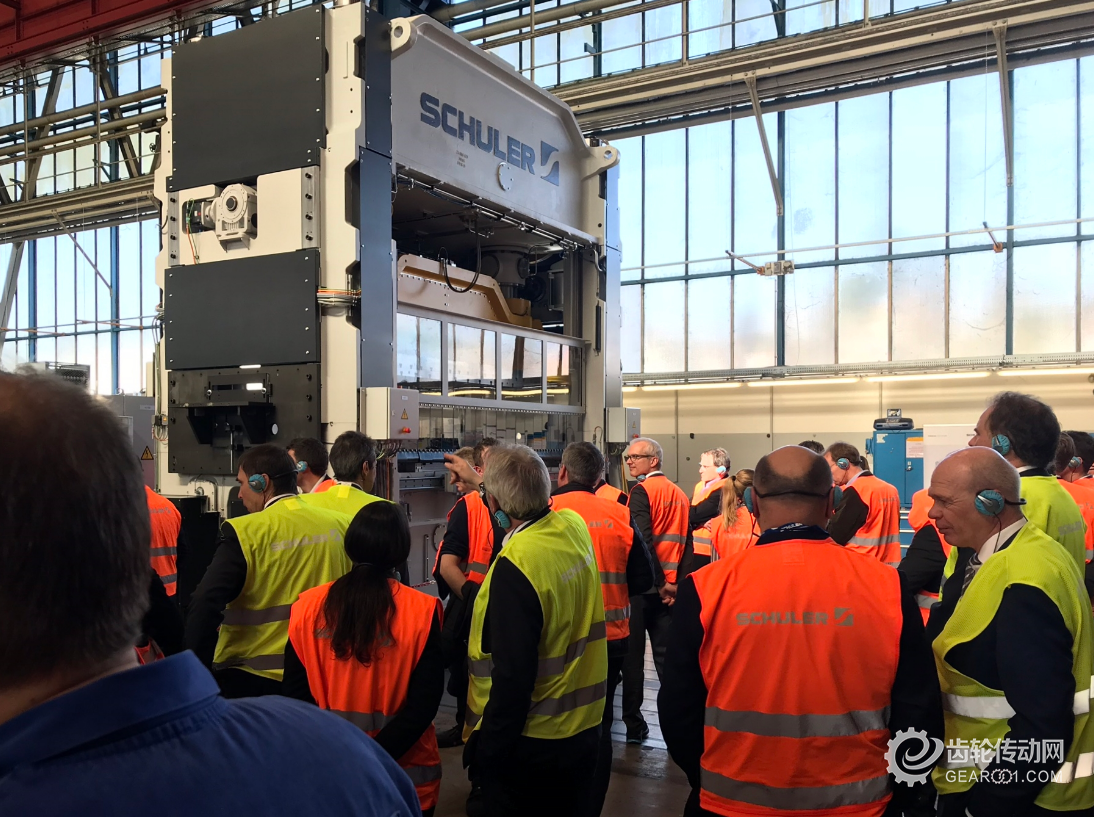
圖5: 舒勒技術(shù)日活動(dòng)的參與者超過了 50 人。
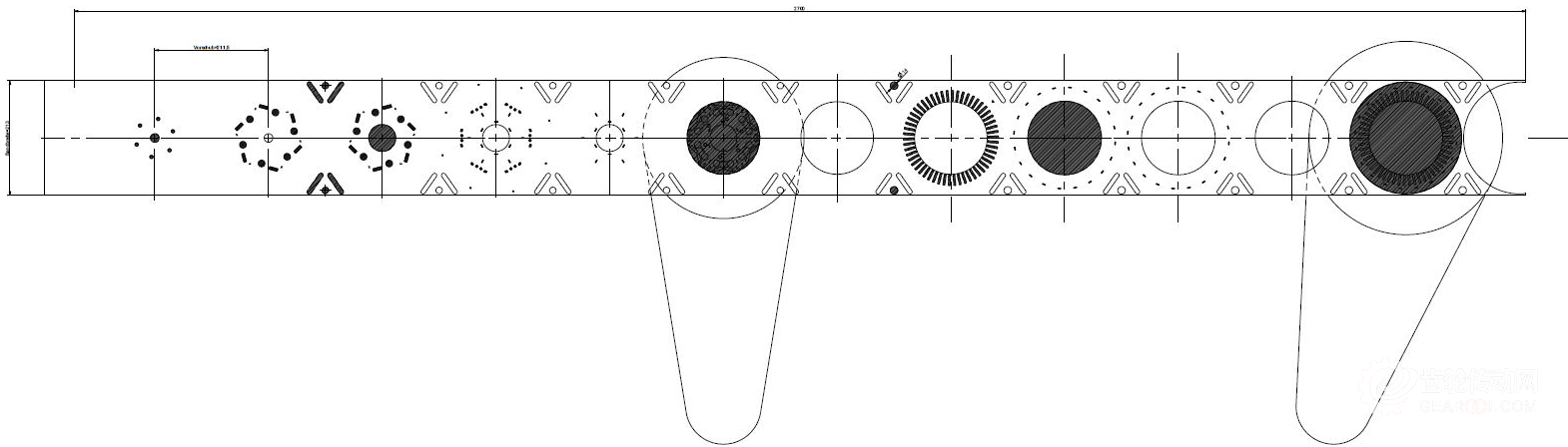
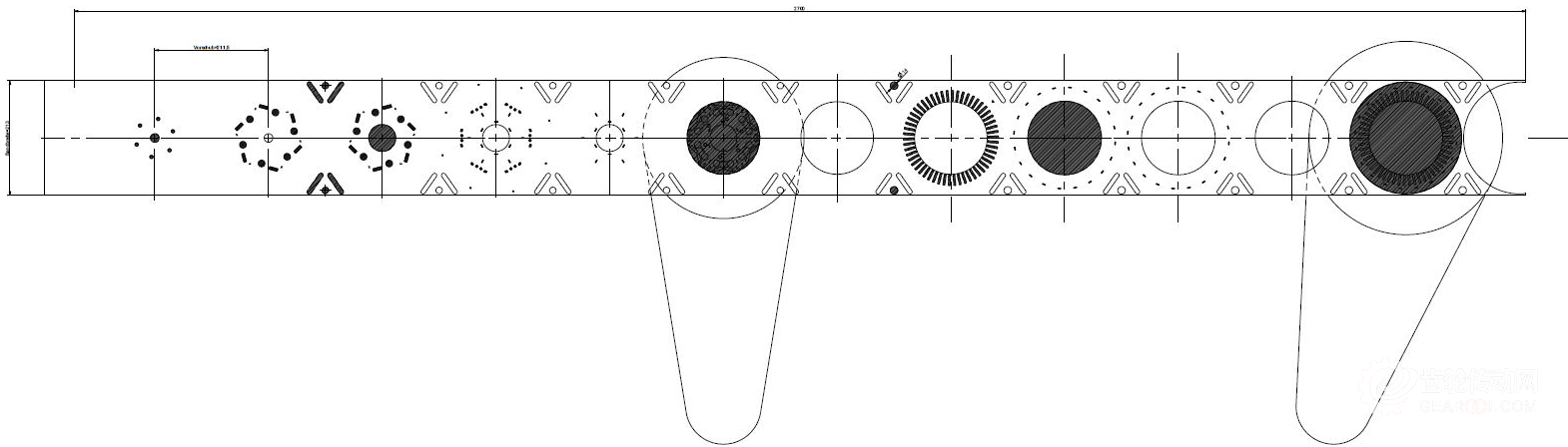
圖6: 客戶要生產(chǎn)的沖片數(shù)量是決定采用單排或雙排模具的主要因素。
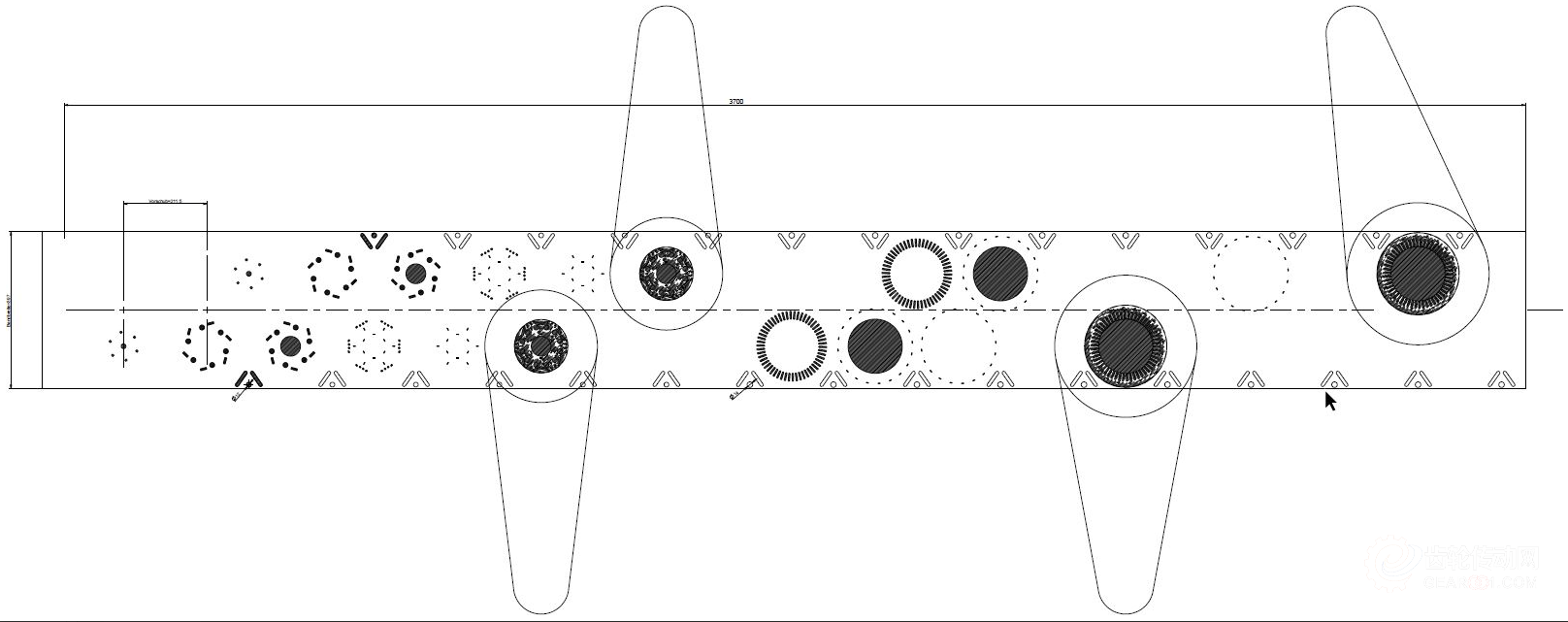
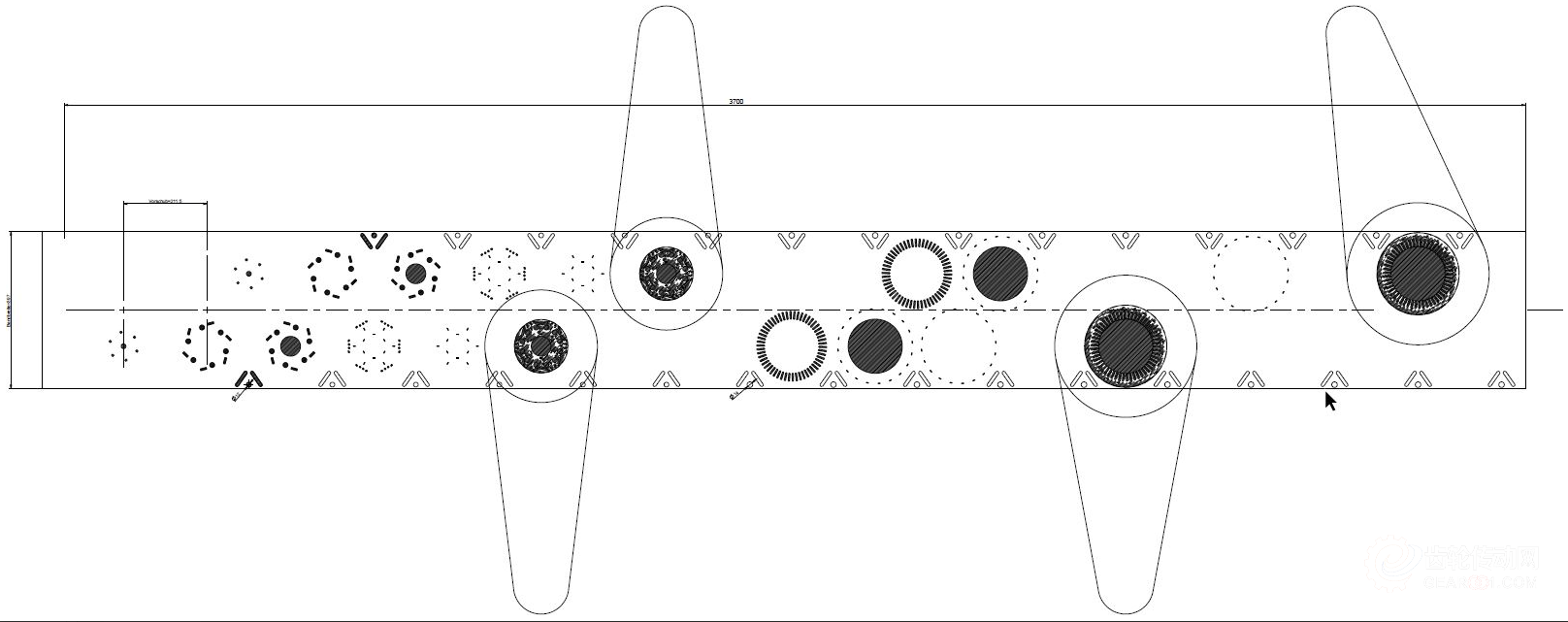
圖7: 針對(duì)更高的產(chǎn)能要求,AWEBA 也開發(fā)了雙排布局的模具,完美適配舒勒的 Smartline EV 3.8 高速?zèng)_。


圖8: 電池殼體原材料采用鋁材料塊(左)通過沖擊擠壓制成,并經(jīng)過成形、處理、切邊、清洗等工藝進(jìn)行加工。
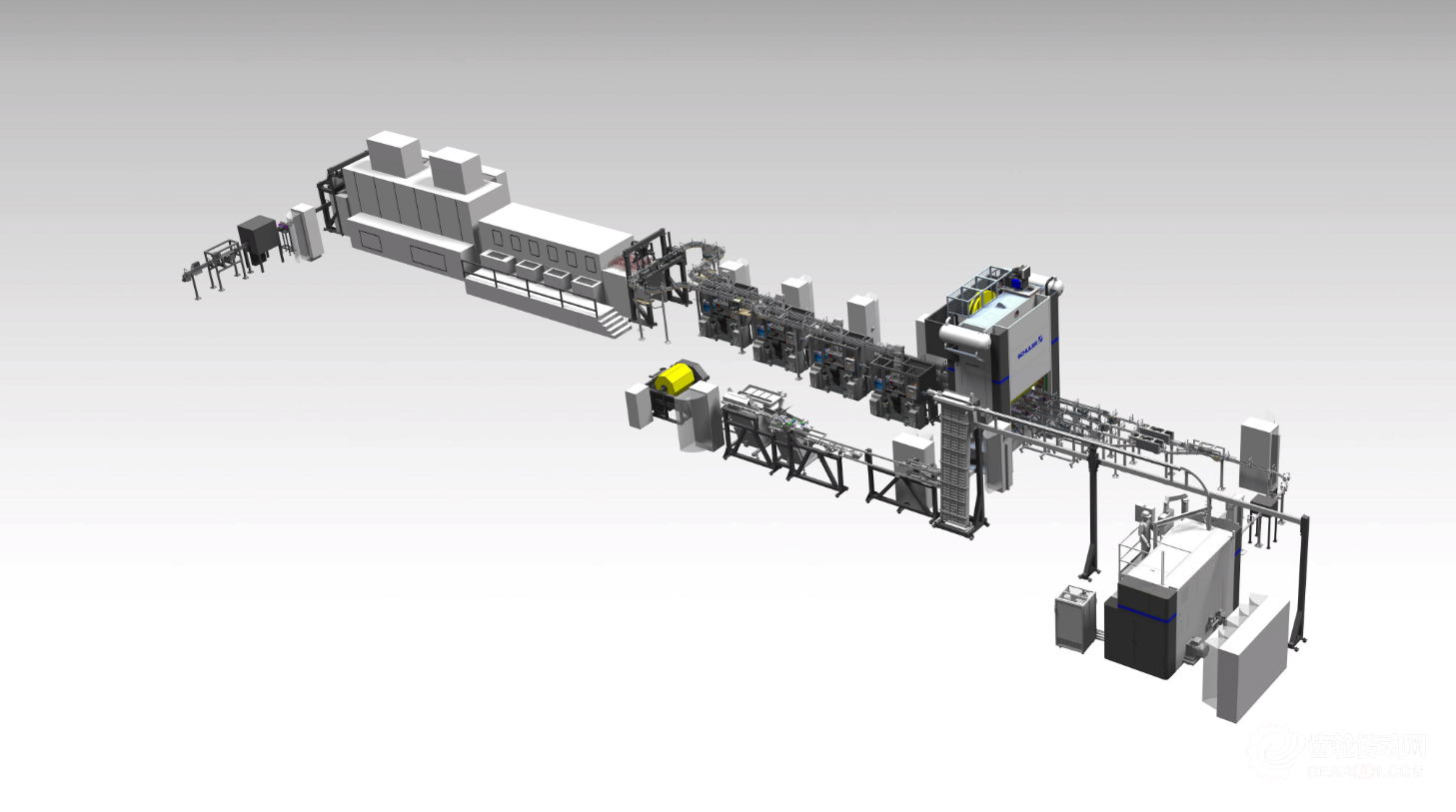
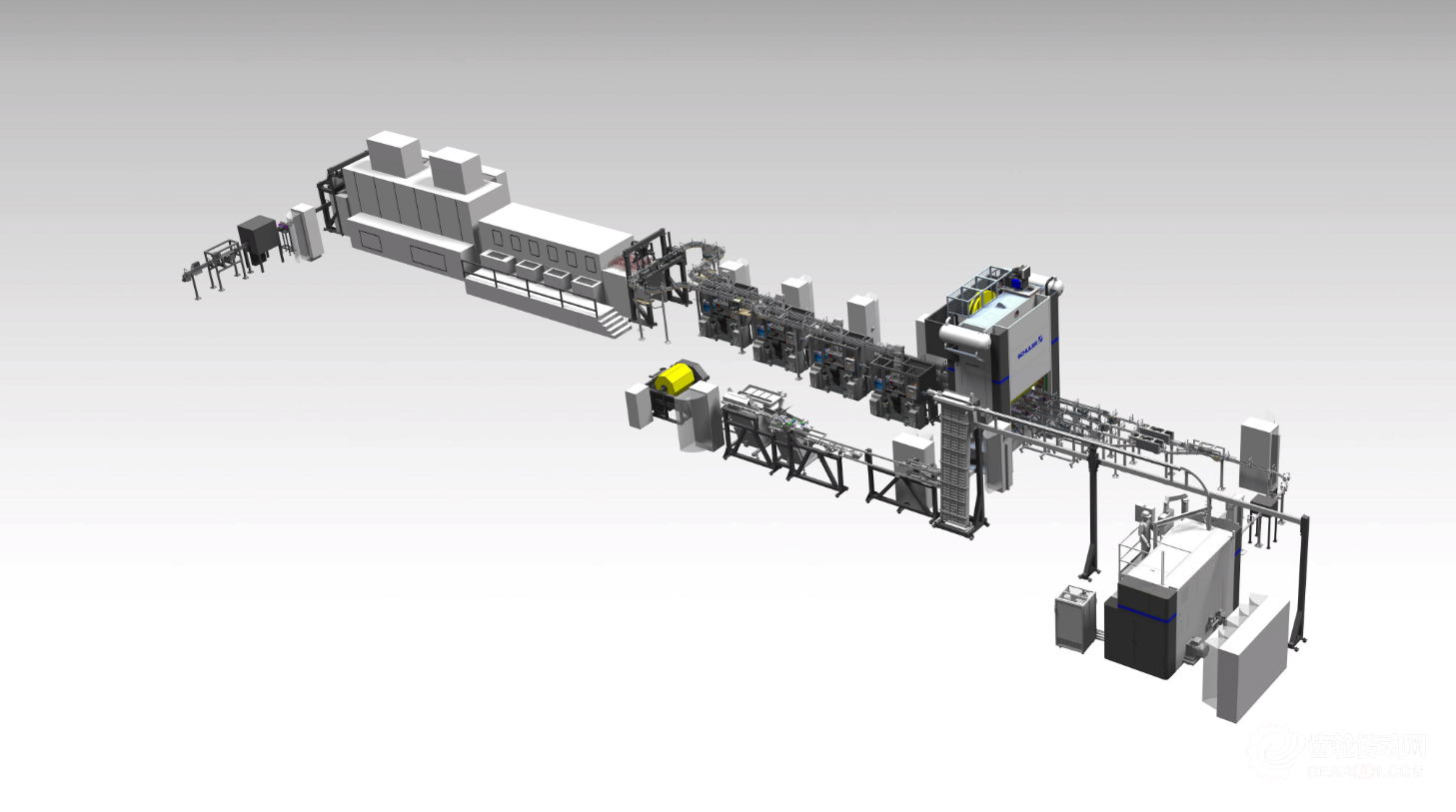
s 圖9: 生產(chǎn)線由沖擊擠壓機(jī)(右下)、精沖整形壓力機(jī)、切邊機(jī)、清洗裝置和烘干裝置組成。
請(qǐng)注明所有照片均出自舒勒。
關(guān)于舒勒集團(tuán) – www.schulergroup.com
舒勒為客戶提供從聯(lián)網(wǎng)壓力機(jī)到?jīng)_壓車間規(guī)劃的先進(jìn)成形技術(shù)。除壓力機(jī)外,舒勒的產(chǎn)品范圍還包括面向整個(gè)金屬加工行業(yè)的自動(dòng)化與軟件解決方案、模具、工藝技術(shù)以及相關(guān)服務(wù)。舒勒的客戶不僅包括汽車制造商及零部件供應(yīng)商,還包括來自鍛造、家用電器和電子工業(yè)等諸多行業(yè)的公司。舒勒的壓力機(jī)為全球超過 180 個(gè)國(guó)家生產(chǎn)硬幣。作為創(chuàng)新系統(tǒng)解決方案供應(yīng)商,我們也向全球客戶提供成形技術(shù)相關(guān)的數(shù)字化改造服務(wù)。2018 財(cái)年舒勒銷售額達(dá)到 12.12 億歐元。舒勒股份公司成立于 1839 年,總部位于德國(guó)格平根,在歐洲、中國(guó)、美國(guó)等全球 40 多個(gè)國(guó)家和地區(qū)的員工總數(shù)約為 6600 人。奧地利的安德里茨集團(tuán)持有舒勒的多數(shù)股權(quán)。