大型工程機(jī)械設(shè)備是由多種部件構(gòu)成,每個(gè)部件是否能夠穩(wěn)定運(yùn)行均影響著工程機(jī)械的性能發(fā)揮,尤其是齒輪部件?,F(xiàn)今,工程機(jī)械設(shè)備正在向著高性能、高強(qiáng)度、大型化、高可靠性等方向發(fā)展,使得齒輪傳動(dòng)在設(shè)備中承擔(dān)的任務(wù)愈來(lái)愈重,伴隨著工程機(jī)械設(shè)備應(yīng)用時(shí)間的增加,齒輪內(nèi)部接觸疲勞逐漸累積,致使齒輪出現(xiàn)裂紋,裂紋擴(kuò)展范圍過(guò)大會(huì)發(fā)生斷裂現(xiàn)象,造成齒輪失效,威脅著工程機(jī)械設(shè)備的安全運(yùn)行。齒輪內(nèi)部疲勞斷裂可靠性很難進(jìn)行直接監(jiān)測(cè),而數(shù)值模擬方法為其提供了有力的手段支撐,能夠預(yù)測(cè)齒輪內(nèi)部疲勞斷裂可靠性相關(guān)數(shù)值,為工程機(jī)械的穩(wěn)定運(yùn)行提供支撐。
文獻(xiàn)以齒輪材料強(qiáng)度退化理論與應(yīng)力強(qiáng)度模糊干涉函數(shù)為基礎(chǔ),聯(lián)合齒輪疲勞準(zhǔn)則構(gòu)建齒輪內(nèi)部疲勞斷裂可靠性分析模型,探究并計(jì)算多種因素對(duì)于齒輪內(nèi)部疲勞斷裂的影響程度,以此為依據(jù),對(duì)齒輪進(jìn)行優(yōu)化設(shè)計(jì),提升齒輪內(nèi)部疲勞斷裂可靠性;文獻(xiàn)以 20CrMnTi 作為研究對(duì)象,在試驗(yàn)機(jī)上進(jìn)行疲勞斷裂試驗(yàn),應(yīng)用數(shù)值模擬軟件對(duì)齒輪內(nèi)部疲勞斷裂過(guò)程進(jìn)行數(shù)值模擬,為齒輪優(yōu)化設(shè)計(jì)提供有力的支撐;文獻(xiàn)采用 Monte-Carlo 模擬齒輪內(nèi)部疲勞斷裂過(guò)程,并依據(jù)齒輪內(nèi)部疲勞斷裂模擬數(shù)值與實(shí)際數(shù)值之間的誤差對(duì)數(shù)值模擬過(guò)程進(jìn)行不斷的優(yōu)化與調(diào)整。上述三種方法雖然能夠?qū)崿F(xiàn)齒輪內(nèi)部疲勞斷裂數(shù)值模擬功能,但是均存在著模擬數(shù)值與實(shí)際數(shù)值之間誤差較大的缺陷,無(wú)法滿(mǎn)足工程機(jī)械的應(yīng)用需求,故提出新的工程機(jī)械齒輪內(nèi)部疲勞斷裂可靠性數(shù)值模擬方法。
一、疲勞斷裂可靠性數(shù)值模擬方法設(shè)計(jì)
工程機(jī)械齒輪模型構(gòu)建
為了更好地進(jìn)行齒輪內(nèi)部疲勞斷裂可靠性數(shù)值模擬,獲取更加精準(zhǔn)的數(shù)值模擬結(jié)果,首要環(huán)節(jié)就是構(gòu)建工程機(jī)械齒輪模型,為后續(xù)研究奠定堅(jiān)實(shí)的基礎(chǔ)。工程機(jī)械齒輪模型如圖 1 所示。
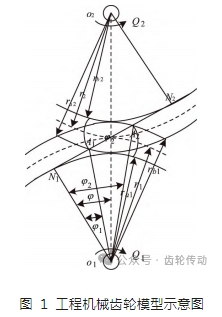
如圖 1 所示,o1 與 o2 表示的是主動(dòng)齒輪與從動(dòng)齒輪的中心;Q1 與 Q2 表示的是主動(dòng)齒輪與從動(dòng)齒輪的運(yùn)動(dòng)方向;N1 與 N2 連線(xiàn)表示的是齒輪副理論嚙合線(xiàn);A1 與 A2 連線(xiàn)表示的是齒輪副實(shí)際嚙合線(xiàn);r1 、ra1與 rb1分別表示的是主動(dòng)齒輪對(duì)應(yīng)的分度圓半徑、齒頂圓半徑與基圓半徑;r2 、ra2與 rb2分別表示的是從動(dòng)齒輪對(duì)應(yīng)的分度圓半徑、齒頂圓半徑與基圓半徑;φ 表示的是齒輪的壓力角;φ1 與 φ2 表示的是主動(dòng)齒輪與從動(dòng)齒輪對(duì)應(yīng)的壓力角。齒輪基圓,分度圓和齒頂圓對(duì)應(yīng)的半徑數(shù)值如下式所示:
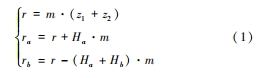
式(1)中,r、ra 與 rb 表示的是齒輪基圓、分度圓與齒頂圓的半徑;m 表示的是齒輪模數(shù);z1 與 z2 表示的是主動(dòng)齒輪與從動(dòng)齒輪對(duì)應(yīng)的齒數(shù);Ha 表示的是齒頂高系數(shù);Hb 表示的是頂隙系數(shù)。
齒輪重合度好壞是影響其磨損大小的關(guān)鍵因素,以齒輪重合度理論為基礎(chǔ),得到齒輪重合度計(jì)算公式:

式(2)中,ζ 表示的是齒輪重合度數(shù)值。
一般情況下,齒輪瞬時(shí)壓力角是確定理論接觸線(xiàn)的主要依據(jù),其計(jì)算公式為:

式(3)中,φt 表示的是齒輪瞬時(shí)壓力角;φ1,n與 φ2,n表示的是主動(dòng)齒輪與從動(dòng)齒輪對(duì)應(yīng)的瞬時(shí)壓力角。
以式(3)計(jì)算結(jié)果為依據(jù),即可確定齒輪的理論接觸線(xiàn),具體確定流程如圖 2 所示。
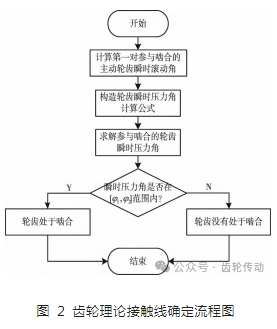
上述過(guò)程完成了工程機(jī)械齒輪模型的構(gòu)建,并給出了齒輪理論接觸線(xiàn)的確定流程,為齒輪內(nèi)部力學(xué)特性分析提供支撐。
齒輪內(nèi)部力學(xué)特性分析
以上述構(gòu)建工程機(jī)械齒輪模型為基礎(chǔ),利用邊界元法求解齒輪內(nèi)部應(yīng)力強(qiáng)度因子,分析齒輪內(nèi)部力學(xué)特性,為后續(xù)齒輪內(nèi)部疲勞斷裂可靠性模型搭建提供數(shù)據(jù)基礎(chǔ)。
由線(xiàn)性斷裂力學(xué)分析可知,齒輪內(nèi)部疲勞裂紋前緣應(yīng)力場(chǎng)與應(yīng)變場(chǎng)存在著一定的奇異性,為了更加精準(zhǔn)的分析齒輪內(nèi)部力學(xué)特性,利用奇異性邊界元法獲取齒輪內(nèi)部疲勞裂紋邊界應(yīng)變性質(zhì),以此為基礎(chǔ),計(jì)算齒輪內(nèi)部疲勞裂紋應(yīng)力強(qiáng)度因子,為后續(xù)研究提供數(shù)據(jù)支撐。其中,采用八節(jié)點(diǎn)等參元方法對(duì)齒輪內(nèi)部疲勞裂紋邊界進(jìn)行處理,其插值函數(shù)表達(dá)式為:
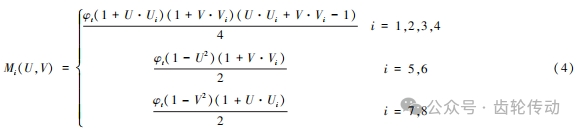
式(4)中,Mi(U,V)表示的是齒輪內(nèi)部疲勞裂紋邊界插值函數(shù)。其中,U 與 V 表示的是橫向與縱向?qū)?yīng)的應(yīng)力數(shù)值;Ui 與 Vi 表示的是第 i 個(gè)插值點(diǎn)對(duì)應(yīng)的橫向與縱向應(yīng)力數(shù)值。
八節(jié)點(diǎn)等參元與等參奇性元如圖 3 所示。
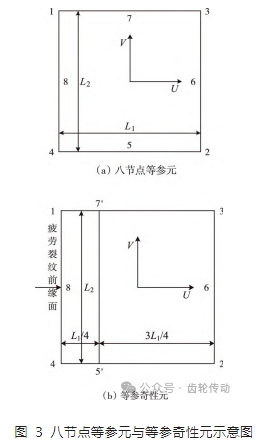
如圖 3 所示,利用等參變換方法確定插值點(diǎn)連線(xiàn)之間的橫軸坐標(biāo)信息(以插值點(diǎn) 1 與插值點(diǎn) 2 連線(xiàn)為例),計(jì)算公式為:

式(5)中,X 表示的是插值點(diǎn) 1 與插值點(diǎn) 2 連線(xiàn)的橫軸坐標(biāo)信息;X1 、X2 表示的是插值點(diǎn) 1、插值點(diǎn) 2 對(duì)應(yīng)的橫坐標(biāo)信息。
基于雅可比式原理,結(jié)合式(5)計(jì)算結(jié)果,即可確定齒輪內(nèi)部疲勞裂紋邊界應(yīng)變數(shù)值,其表達(dá)式為:
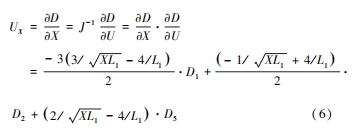
式(6)中,UX 表示的是橫軸方向?qū)?yīng)的齒輪內(nèi)部疲勞裂紋邊界應(yīng)變數(shù)值;D 表示的是位移數(shù)值;J-1表示的是雅可比式輔助因子,其取值范圍為[0,1];L1 表示的是齒輪內(nèi)部疲勞裂紋的長(zhǎng)度;D1 、D2 與 D5 表示的是插值點(diǎn) 1、插值點(diǎn) 2 與插值點(diǎn) 5 對(duì)應(yīng)的位移數(shù)值。
根據(jù)實(shí)際情況將齒輪內(nèi)部疲勞裂紋看作為半橢圓形,即疲勞裂紋前緣參數(shù)方程可以寫(xiě)為:

式(7)中,x 與 y 表示的是疲勞裂紋前緣坐標(biāo)信息;Vy 表示的是縱軸方向?qū)?yīng)的齒輪內(nèi)部疲勞裂紋邊界應(yīng)變數(shù)值;θ 表示的是半橢圓形裂紋內(nèi)角。
以柱坐標(biāo)系為標(biāo)準(zhǔn)來(lái)展示疲勞裂紋單元,具體如圖 4 所示。
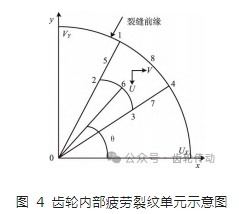
如圖 4 所示,齒輪內(nèi)部疲勞裂紋位移與應(yīng)力強(qiáng)度因子之間存在著緊密的聯(lián)系,表達(dá)式為:

式(8)中,是每循環(huán)的裂紋擴(kuò)展長(zhǎng)度;C 是常數(shù);K 是應(yīng)力強(qiáng)度因子;Kth是裂紋開(kāi)始擴(kuò)展所需的最小應(yīng)力強(qiáng)度因子。
通過(guò)求解公式(8)即可獲得齒輪內(nèi)部力學(xué)特性———齒輪內(nèi)部疲勞裂紋應(yīng)力強(qiáng)度因子 K,為后續(xù)研究提供支撐。
齒輪內(nèi)部疲勞斷裂可靠性模型搭建
以上述齒輪內(nèi)部力學(xué)特性分析結(jié)果為基礎(chǔ),融合齒輪內(nèi)部極限狀態(tài),搭建齒輪內(nèi)部疲勞斷裂可靠性模型,為最終數(shù)值模擬實(shí)現(xiàn)提供依據(jù)。
一般情況下,齒輪內(nèi)部失效存在一個(gè)模糊漸變區(qū),其隸屬函數(shù)表達(dá)式為:
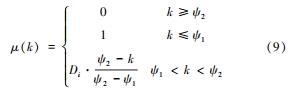
式(9)中,μ(k)表示的是齒輪內(nèi)部失效模糊漸變區(qū)隸屬度數(shù)值,k 表示的是模糊數(shù);ψ1 與 ψ2 表示的是模糊上界與下界。
以式(9)計(jì)算結(jié)果為依據(jù),即可獲得齒輪內(nèi)部疲勞斷裂可靠性數(shù)值,表達(dá)式為:
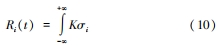
式(10)中,Ri(t)的取值范圍為 0~ 1;σi 表示的是齒輪內(nèi)部的應(yīng)力均值。
上述過(guò)程完成了齒輪內(nèi)部疲勞斷裂可靠性的計(jì)算,為研究目標(biāo)的實(shí)現(xiàn)提供支撐。
齒輪內(nèi)部疲勞斷裂可靠性數(shù)值模擬
以 2. 1 節(jié)構(gòu)建的工程機(jī)械齒輪模型為基底,以 2. 2 節(jié)計(jì)算獲得的應(yīng)力強(qiáng)度因子與 2. 3 節(jié)搭建的齒輪內(nèi)部疲勞斷裂可靠性模型為依據(jù),建立齒輪內(nèi)部疲勞裂紋動(dòng)態(tài)擴(kuò)展模型,以此為依據(jù),對(duì)齒輪內(nèi)部疲勞斷裂全過(guò)程進(jìn)行數(shù)值模擬。
在數(shù)值模擬過(guò)程中,首要環(huán)節(jié)就是確定工程機(jī)械齒輪內(nèi)部載荷情況與邊界條件,以此為基礎(chǔ),應(yīng)用 ABAQUS 軟件對(duì)齒輪進(jìn)行有限元?jiǎng)澐?,具體如圖 5 所示。
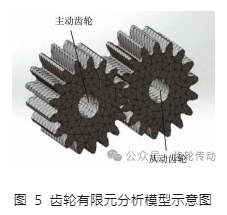
以圖 5 為依據(jù),建立齒輪內(nèi)部疲勞裂紋動(dòng)態(tài)擴(kuò)展模型,表達(dá)式為:

式(11)中,g(t)表示的是疲勞裂紋動(dòng)態(tài)擴(kuò)展模型;G[·]表示的是齒輪內(nèi)部狀態(tài)函數(shù);υi(t)表示的是齒輪內(nèi)部疲勞裂紋的擴(kuò)展速率。
依據(jù)式(11)對(duì)齒輪內(nèi)部疲勞斷裂過(guò)程進(jìn)行數(shù)值模擬,為齒輪狀態(tài)監(jiān)測(cè)提供有效的方法支撐。
二、實(shí)驗(yàn)與結(jié)果分析
設(shè)置風(fēng)電滲碳齒輪內(nèi)部疲勞斷裂可靠性研究、20CrMnTi 齒輪鋼疲勞裂紋擴(kuò)展試驗(yàn)與數(shù)值模擬研究為對(duì)比方法 1、對(duì)比方法 2,聯(lián)合提出方法共同進(jìn)行工程機(jī)械齒輪內(nèi)部疲勞斷裂可靠性數(shù)值模擬對(duì)比實(shí)驗(yàn),以此來(lái)驗(yàn)證提出方法的應(yīng)用性能。
實(shí)驗(yàn)設(shè)備選取
依據(jù)對(duì)比實(shí)驗(yàn)需求,選取疲勞試驗(yàn)機(jī)與齒輪夾具作為主要實(shí)驗(yàn)設(shè)備,具體如圖 6 所示。
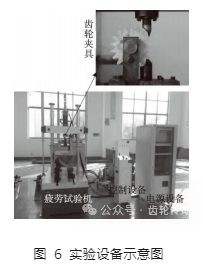
選取的疲勞試驗(yàn)機(jī)實(shí)質(zhì)上是一種機(jī)械共振材料試驗(yàn)設(shè)備,頻率范圍為 80~ 250Hz,標(biāo)準(zhǔn)頻率計(jì)算公式為:

式(12)中,fo 表示的是疲勞試驗(yàn)機(jī)的標(biāo)準(zhǔn)頻率;Ctotal 表示的是疲勞試驗(yàn)機(jī)的總剛度;Mtotal 表示的是疲勞試驗(yàn)機(jī)的總質(zhì)量。
依據(jù)實(shí)驗(yàn)需求對(duì)疲勞試驗(yàn)機(jī)其它參數(shù)進(jìn)行設(shè)置,具體如表 1 所示。
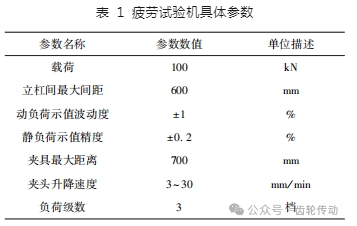
上述過(guò)程完成了實(shí)驗(yàn)設(shè)備———疲勞試驗(yàn)機(jī)與齒輪夾具的選取任務(wù),為實(shí)驗(yàn)的順利進(jìn)行提供了一定的便利。
實(shí)驗(yàn)結(jié)果分析
以上述選取的實(shí)驗(yàn)設(shè)備為工具,進(jìn)行工程機(jī)械齒輪內(nèi)部疲勞斷裂可靠性數(shù)值模擬對(duì)比實(shí)驗(yàn),通過(guò)齒輪內(nèi)部疲勞裂紋擴(kuò)展速率數(shù)值模擬結(jié)果與齒輪內(nèi)部疲勞斷裂可靠性數(shù)值模擬結(jié)果驗(yàn)證提出方法的應(yīng)用性能。
通過(guò)實(shí)驗(yàn)獲得齒輪內(nèi)部疲勞裂紋擴(kuò)展速率數(shù)值模擬結(jié)果如圖 7 所示。
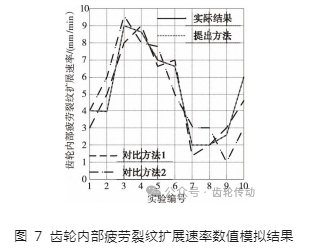
如圖 7 所示,應(yīng)用提出方法獲得的齒輪內(nèi)部疲勞裂紋擴(kuò)展速率數(shù)值模擬結(jié)果與實(shí)際結(jié)果基本保持一致,而對(duì)比方法 1 與對(duì)比方法 2 應(yīng)用后獲得的齒輪內(nèi)部疲勞裂紋擴(kuò)展速率數(shù)值模擬結(jié)果與實(shí)際結(jié)果存在著一定的偏差。說(shuō)明提出方法的模擬結(jié)果更加可靠,可以為齒輪狀態(tài)分析提供精準(zhǔn)的數(shù)據(jù)基礎(chǔ)。
通過(guò)實(shí)驗(yàn)獲得齒輪內(nèi)部疲勞斷裂可靠性數(shù)值模擬結(jié)果如圖 8 所示。
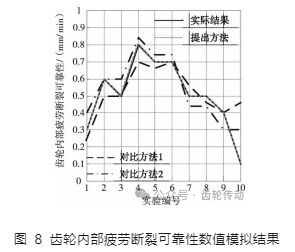
如圖 8 所示,應(yīng)用提出方法獲得的齒輪內(nèi)部疲勞斷裂可靠性數(shù)值模擬結(jié)果與實(shí)際結(jié)果基本保持一致,而對(duì)比方法 1 與對(duì)比方法 2 應(yīng)用后獲得的齒輪內(nèi)部疲勞斷裂可靠性數(shù)值模擬結(jié)果與實(shí)際結(jié)果存在著一定的偏差。由此進(jìn)一步驗(yàn)證了提出方法的應(yīng)用效果,其具備較高模擬精度,有利于保障工程機(jī)械設(shè)備運(yùn)行穩(wěn)定性與安全性。
三、結(jié)束語(yǔ)
隨著工程機(jī)械設(shè)備應(yīng)用頻率的升高,其應(yīng)用缺陷逐漸顯現(xiàn),尤其是齒輪內(nèi)部疲勞斷裂故障,直接威脅著工程機(jī)械能否繼續(xù)運(yùn)行,其直接監(jiān)測(cè)難以實(shí)現(xiàn),故提出工程機(jī)械齒輪內(nèi)部疲勞斷裂可靠性數(shù)值模擬方法。實(shí)驗(yàn)結(jié)果顯示:提出方法應(yīng)用后獲得的數(shù)值模擬結(jié)果與實(shí)際結(jié)果基本相同,表明提出方法數(shù)值模擬精度較高,能為工程機(jī)械穩(wěn)定運(yùn)行提供有效的保障。
參考文獻(xiàn)略.