一、風(fēng)電齒輪箱金屬齒軸斷齒的基本情況
齒輪箱系統(tǒng)作為整個(gè)風(fēng)機(jī)系統(tǒng)的核心部件,受到通過葉片系統(tǒng)傳遞來的低速強(qiáng)載荷的擾動(dòng)沖擊作用,同時(shí)承載齒輪箱的機(jī)艙系統(tǒng)在陣風(fēng)作用下也有較大幅度的擺動(dòng),再加上內(nèi)部的溫度計(jì)潤滑狀態(tài)的變動(dòng),因此關(guān)鍵零部件金屬齒輪、軸承、主軸等失效問題是目前最主要、影響最大的裝備故障,齒輪輪齒損傷是目前比例大且影響相對(duì)較大的損傷形式。某風(fēng)場使用的風(fēng)機(jī)在服役 3 年后發(fā)生故障,進(jìn)行檢查后發(fā)現(xiàn)在齒輪箱齒軸上有斷齒現(xiàn)象,如圖 1 所示。本文通過宏觀檢查、斷口微觀形貌分析、化學(xué)成分分析、低倍試驗(yàn)、力學(xué)性能試驗(yàn)、金屬夾渣物評(píng)級(jí)、金相組織分析方法對(duì)該齒軸斷齒現(xiàn)象進(jìn)行分析。
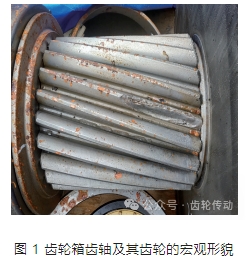
二、實(shí)驗(yàn)研究
宏觀檢查
金屬齒軸齒輪上有 1 個(gè)輪齒在偏右側(cè)齒端處發(fā)生折斷,開裂起始于輪齒的工作面靠近齒根處,其余輪齒未發(fā)生折斷,在金屬輪齒的工作面上均有印痕存在,其分布與斷齒的斷裂位置(見圖 2)。
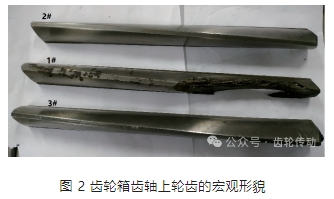
在體視顯微鏡下觀察發(fā)現(xiàn),斷齒(編為 1#)起始開裂處的邊緣存在明顯的壓痕,部分區(qū)域的表層金屬已被壓碎 ;2 個(gè)未斷裂的輪齒(編號(hào)為 2# 和 3#)工作面上存在壓痕、擦傷和破損現(xiàn)象,齒頂及其附近的非工作面上均有擦傷或破損痕跡存在,3# 輪齒非工作面局部區(qū)域存在麻點(diǎn)狀銹蝕點(diǎn)。
斷口微觀形貌
掃描電鏡觀察斷裂金屬輪齒的斷口形貌發(fā)現(xiàn),斷裂起始于輪齒的工作面?zhèn)?,裂源區(qū)的斷口形貌呈疲勞輝紋特征(見圖 3、圖 4、圖 5),裂紋擴(kuò)展區(qū)的斷口形貌呈疲勞輝紋特征(見圖 6、圖 7、圖 8)。
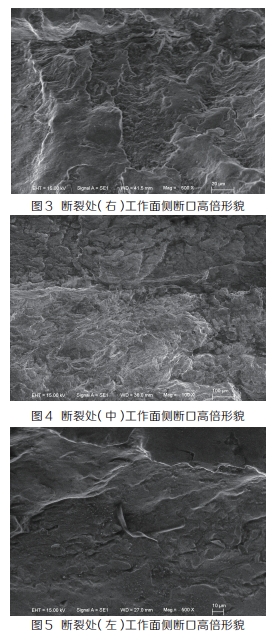
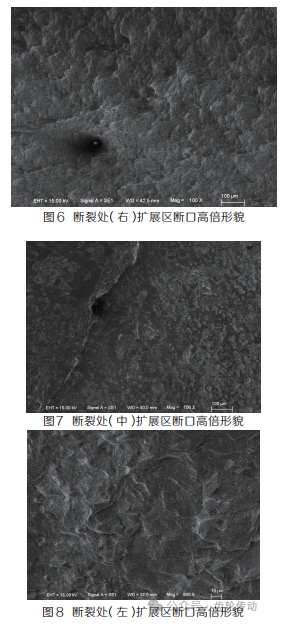
化學(xué)成分分析
對(duì)金屬齒輪進(jìn)行化學(xué)成分分析,結(jié)果發(fā)現(xiàn)齒輪的成分符合 EN10084-1998 中 18CrNiMo7-6 的成分標(biāo)準(zhǔn),結(jié)果見表 1。

低倍檢驗(yàn)
在斷裂的輪齒(1#)、未斷裂的輪齒(2#、3#)上取橫截面,腐蝕后發(fā)現(xiàn)輪齒的表面淬硬層完整,無明顯差異。
金相檢驗(yàn)
在 2# 輪齒上取縱截面,參照 GB/T 10561-2005 鋼中金屬夾雜物含量的測定標(biāo)準(zhǔn)評(píng)級(jí)圖顯微檢驗(yàn)法進(jìn)行評(píng)級(jí),輪齒的金屬夾雜物評(píng)為 A 類細(xì)系 0.5 級(jí),結(jié)果見表 2。
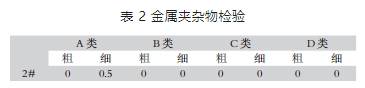
分別在 1# 輪齒的未損壞區(qū)域取橫截面和縱截面、在 2# 輪齒對(duì)應(yīng)于 1# 輪齒的損壞區(qū)域取橫截面和縱截面進(jìn)行金相檢驗(yàn),結(jié)果發(fā)現(xiàn)金屬齒頂和齒根部位均存在微裂紋,齒面基本無微裂紋,但在 2# 輪齒的齒面上存在損傷凹坑;輪齒表面經(jīng)過滲碳淬回火處理,滲碳層的金相組織為針狀馬氏體、貝氏體及殘余奧氏體,輪齒心部的金相組織為回火馬氏體 + 貝氏體,組織中存在帶狀偏析(見圖 9~18)。
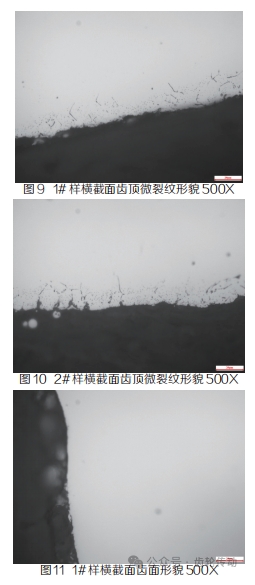
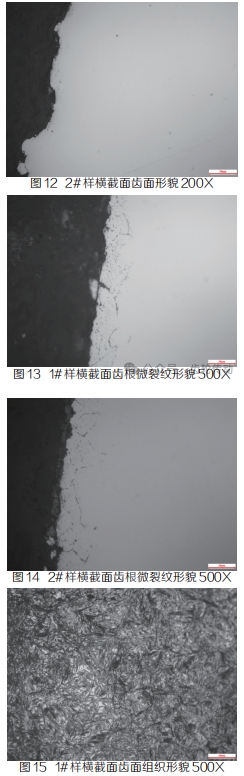
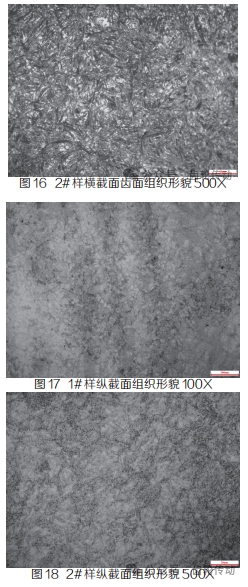
參照 GB/T 6394-2017 金屬平均晶粒度測定方法,1# 輪齒和 2# 輪齒的晶粒度評(píng)為 7 級(jí),形貌見圖 19、圖 20。
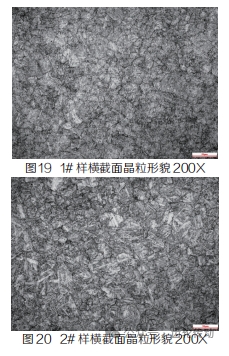
滲層深度測試
分別在 1# 輪齒的未損壞區(qū)域取橫截面、在 2# 輪齒對(duì)應(yīng)于 1# 輪齒的損壞區(qū)域取橫截面,對(duì)齒頂、齒面、齒根進(jìn)行有效硬化層深度的測定:1# 齒頂有效硬化層深度約為 4.2mm,2# 齒頂有效硬化層深度約為 2.6mm,1# 齒面有效硬化層深度約為 2.8mm,2# 齒面有效硬化層深度約為 2.4mm,1# 齒根有效硬化層深度約為 2.8mm,2# 齒根有效硬化層深度約為 2.6mm,1# 輪和 2# 輪齒的齒硬化層硬度變化曲線見圖 21、22。
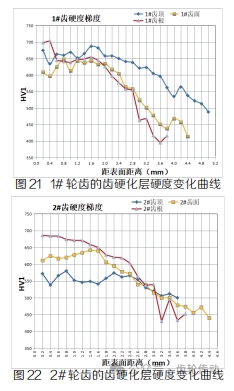
硬度檢測
分別在1#輪齒(斷裂齒)和2#(完整齒)輪齒的橫截面上對(duì)基體進(jìn)行硬度檢測,1#輪齒的基體硬度為36.0~39.0HRC,表面硬度為56.6~59.5HRC,2#輪齒的基體硬度為38.5~40.0HRC,表面硬度為51.8~58.9HRC,結(jié)果見表3。
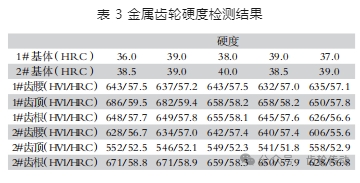
沖擊試驗(yàn)
在金屬齒軸半徑的 1/3 位置取 1 組橫向沖擊試樣,齒軸半徑的 1/2 位置取 1 組縱向沖擊試樣,在 -40℃下進(jìn)行沖擊性能試驗(yàn),結(jié)果見表 4?!?/p>
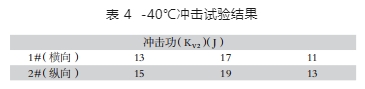
三、分析討論
實(shí)驗(yàn)結(jié)果表明:金屬齒軸齒輪的成分符合成分符合 EN10084-1998 中 18CrNiMo7-6 的成分標(biāo)準(zhǔn)。2# 輪齒的輪齒的非金屬夾雜物評(píng)為 A 類細(xì)系 0.5 級(jí) ;1# 輪齒和 2# 輪齒的晶粒度評(píng)為 7 級(jí) ;1# 輪齒的未損壞區(qū)域的齒頂和齒根部位均存在微裂紋,齒面基本無微裂紋 ;2# 輪齒對(duì)應(yīng)于 1# 輪齒的損壞區(qū)域的齒頂和齒根部位均存在微裂紋,齒面基本無微裂紋,但有損傷凹坑存在 ;1# 輪齒和 2# 輪齒的表面均經(jīng)過滲碳淬回火處理,滲碳層的金相組織為針狀馬氏體、貝氏體及殘余奧氏體,輪齒心部的金相組織均為回火馬氏體 + 貝氏體,組織中存在帶狀偏析 ;斷裂輪齒和未斷裂輪齒的表面淬硬層完整,無明顯差異。1# 輪齒未損壞區(qū)域的有效硬化層深度:齒頂約為 4.2mm,齒面約為 2.8mm,齒根約為 2.8mm ;2# 輪齒對(duì)應(yīng)于 1# 輪齒的損壞區(qū)域的有效硬化層深度 :齒頂約為 2.6mm,齒面約為 2.4mm,齒根約為 2.6mm;1# 輪齒的基體硬度為36.0~39.0HRC,表面硬度為 56.6~59.5HRC,2# 輪齒的基體硬度為38.5~40.0HRC,表面硬度為 51.8~58.9HRC,齒軸材料在 -40℃的沖擊值為 11~19J ;
金屬齒軸齒輪上有 1 個(gè)輪齒在偏右側(cè)發(fā)生疲勞折斷,開裂起始于輪齒的工作面靠近齒根處,起始開裂處的邊緣存在明顯的壓痕,部分區(qū)域的表層金屬已被壓碎。其余輪齒未發(fā)生折斷,但在輪齒的工作面上均有壓痕、擦傷和破損存在,其分布與斷齒的斷裂位置相對(duì)應(yīng)。
從上述實(shí)驗(yàn)結(jié)果來看,在輪齒的未損壞區(qū)域,其齒面和齒根有效硬化層深度約為 2.8mm,齒根有微裂紋存在,為表面淬硬處理產(chǎn)生的缺陷。當(dāng)齒輪在傳動(dòng)過程中,輪齒類似一根懸臂梁,承載后齒根處產(chǎn)生較大的彎曲應(yīng)力,由于輪齒在交變的彎曲應(yīng)力下工作,容易從齒根處的薄弱環(huán)節(jié)形成裂紋源,繼而裂紋發(fā)生疲勞擴(kuò)展,最終導(dǎo)致齒輪疲勞折斷。
整個(gè)齒輪輪齒的右側(cè)存在損傷痕跡,說明該區(qū)域受到異物擠壓。至于異物的來源,很可能是折斷輪齒部分。
四、結(jié)語
金屬齒輪表面淬硬處理后表面有微裂紋存在,輪齒承載后齒根附近受到的應(yīng)力較大,在交變應(yīng)力的作用下輪齒發(fā)生了疲勞折斷。
參考文獻(xiàn)略.