相較于插齒、銑齒等傳統(tǒng)內(nèi)齒輪加工方法,車齒具有材料去除率高、成形精度好等優(yōu)點,同時具備實現(xiàn)精加工的潛能,可以進一步縮短加工鏈,降低能耗。但車齒由于獨特的加工特性,成形齒面會呈現(xiàn)出波紋狀的進給刀痕,影響齒面質(zhì)量,阻礙了其精加工應(yīng)用。因此,研究車齒加工誤差影響因素,降低成形齒面波紋誤差是推廣車齒工藝發(fā)展,實現(xiàn)齒輪高效加工的關(guān)鍵。
目前,國內(nèi)外學(xué)者對車齒工藝進行了大量研究,并且在車齒工藝原理、刀具設(shè)計、切屑成形機理、加工誤差等方面取得了一定成果。針對車齒加工精度的問題,Guo研究了刀具運動偏心誤差對車齒加工精度的影響,研究結(jié)果表明工件齒面出現(xiàn)的進給刀痕的切深與刀具的運動偏心有關(guān),進而在較大程度上影響著工件的齒向和齒形誤差。Maximilian提出了一種計算車齒成形齒面微觀形貌的數(shù)學(xué)模型,并基于該模型探討了不同軸向進對齒面微觀形貌的影響規(guī)律以及對齒輪噪聲的影響。吳震宇針對軸交角誤差的存在影響車齒精度的問題,詳細對比分析了無進給、刀具進給和工件進給三種不同進給方式以及不同軸交角誤差方向?qū)圐X加工誤差的影響程度。楊亞蒙根據(jù)車齒運動學(xué)原理建立了機床幾何位姿誤差與車齒成形齒面法向誤差的映射關(guān)系,研究了各項幾何位姿誤差對法向誤差的影響程度。
本文采用數(shù)值仿真的方法建立了齒面誤差模型,首先基于車齒工藝理論和齊次坐標(biāo)變換原理,根據(jù)刀具和工件的運動學(xué)關(guān)系建立了刀具切削刃空間軌跡曲面幾何數(shù)學(xué)模型;然后采用離散網(wǎng)格方法計算得到齒面法向誤差形貌;最后分析了軸向進給量、刀具前角、刀具螺旋角對最大齒面偏差的影響程度。該模型可以為車齒工藝參數(shù)優(yōu)化、刀具幾何設(shè)計等研究提供支撐。
一、車齒工藝原理
加工外齒輪時車齒刀與工件的相對位置與運動關(guān)系如圖 1 所示。車齒工藝的五個切削參數(shù)對應(yīng)機床的五種運動:車齒刀的回轉(zhuǎn)運動是車齒加工中的主運動,在車齒加工過程中車齒刀以恒定轉(zhuǎn)速 ωc(rad/min)繞軸線連續(xù)回轉(zhuǎn);工作與車齒刀按照一定的傳動比關(guān)系同步回轉(zhuǎn)以保證兩者正確嚙合從而獲得正確的齒形,在車齒加工過程中工件以恒定轉(zhuǎn)速 ωw(rad/min)繞軸線連續(xù)回轉(zhuǎn);工件沿軸線軸向進給加工出齒輪齒寬,描述軸向進給運動的參數(shù)為 v(mm/min);安裝中心距 a 由機床切削運動調(diào)整決定;為了保證車齒刀與工件在節(jié)圓柱面上的螺旋線相切,需要將車齒刀的軸線相對于工件端面偏轉(zhuǎn)一個角度 Σ 進行交錯安裝。
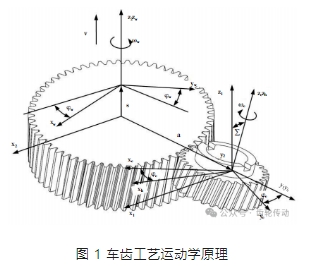
安裝中心距 a 的大小由車齒刀分度圓半徑 rc 與工件分度圓半徑 rw 決定:

式中:“+”用于外齒輪嚙合車齒加工;“-”用于內(nèi)齒輪嚙合車齒加工。本文建立的模型為車齒加工外齒輪模型,此時安裝中心距 a 的大小為 rc+rw。
車齒刀與工件軸線之間的傾斜角被成為軸交角,軸交角 Σ 與車齒刀分度圓螺旋角 βc 和工件分度圓螺旋角 βw 有關(guān),三者關(guān)系為:

式中:當(dāng)加工外齒輪時,“+”用于車齒刀和工件的螺旋方向一致,“-”用于車齒刀和工件的螺旋方向相反;當(dāng)加工內(nèi)齒輪時,“+”用于車齒刀和工件的螺旋方向相反,“-”用于車齒刀和工件的螺旋方向一致。本文模型中車齒刀和工件均為右旋,因此軸交角 Σ 的大小為 βc+βw。
在實際車齒加工過程中,軸向進給運動的引入破壞了工件與車齒刀原本的傳動關(guān)系,因此在加工具有螺旋角的齒輪時,工件或車齒刀還需要額外增加一個回轉(zhuǎn)運動以形成齒輪齒槽螺旋線,這個運動被稱為差動運動,用 Δω 表示。若通過在工件上增加差動運動,此時工件完整的回轉(zhuǎn)運動如下所示:
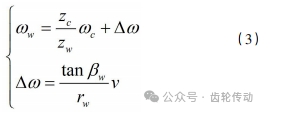
與機床結(jié)構(gòu)一致,共設(shè)置 5 個坐標(biāo)系與各運動部組相對應(yīng):Oh-xhyhzh 為車齒刀安裝坐標(biāo)系,是和車齒刀初始位置重合的固定坐標(biāo)系;O2-x2y2z2 為工件參考坐標(biāo)系,是和工件初始位置重合的固定坐標(biāo)系;O1-x1y1z1 為車齒刀參考坐標(biāo)系,與工件參考坐標(biāo)系相互平行;Oc-xcyczc 為車齒刀固連的運動坐標(biāo)系;Ow-xwywzw 為與工件固連的運動坐標(biāo)系。
根據(jù)齊次坐標(biāo)變換原理,車齒刀坐標(biāo)系和工件坐標(biāo)系之間可以通過變換矩陣進行轉(zhuǎn)換。設(shè)車齒刀切削刃曲線已知,表示在車齒刀坐標(biāo)中為 M=[x(u),y(u),z(u),1] T,通過齊次坐標(biāo)變換,可以得到切削刃運動形成的空間軌跡曲面在工件坐標(biāo)系 Ow-xwywzw 中齊次坐標(biāo)方程為:

式中:Mhc、M1h、M21、Mw2 分別表示從車齒刀坐標(biāo)系到車齒刀安裝坐標(biāo)系、車齒刀安裝坐標(biāo)系到車齒刀參考坐標(biāo)系、車齒刀參考坐標(biāo)系到工件參考坐標(biāo)系、工件參考坐標(biāo)系到工件坐標(biāo)系的變換矩陣,其完整形式如下:
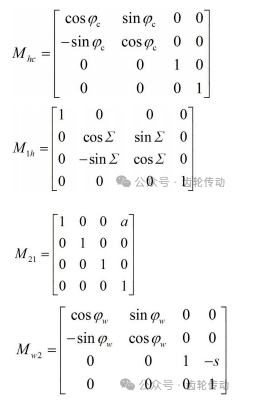
二、車齒成形齒面幾何數(shù)值仿真計算
車齒加工齒面成形過程分析
車齒加工實質(zhì)是車齒刀與工件按照給定傳動比做同步回轉(zhuǎn)運動,由分布在車齒刀上的切削刃根據(jù)運動關(guān)系在空間中掠過生成一系列軌跡曲面,稱為掃掠面,掃掠面依次與工件相交并切除材料,最終形成了加工齒輪的表面形貌。
齒面包絡(luò)波紋誤差計算方法
理想漸開線圓柱齒輪的齒面可視為一條標(biāo)準(zhǔn)漸開線繞齒輪軸線做螺旋創(chuàng)成運動形成的空間漸開面。以漸開線展開角 θ 為參數(shù),標(biāo)準(zhǔn)漸開線的參數(shù)方程表示為:
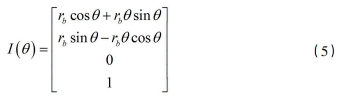
式中:rb 為工件齒輪基圓半徑。
設(shè) M(Δ)表示漸開線生成漸開面的的齊次變換矩陣,以標(biāo)準(zhǔn)漸開線沿齒輪軸線的位移量 ζ 為參數(shù),齒輪理論齒面的齊次坐標(biāo)方程 F(θ,ζ)如式(6)所示:
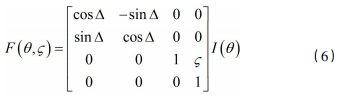
式中:△包括漸開線做螺旋運動時與位移量ζ 對應(yīng)轉(zhuǎn)過的角度和獲得齒槽寬的齒面張角。

式中:ατ 為工件端面壓力角。
齒面包絡(luò)波紋誤差是沿理論齒面 F(θ,ζ)上一點的法向計算的,即齒面的法向誤差,理論齒面 F(θ,ζ)的法向量計算公式為:

本文采用離散網(wǎng)格法計算齒面包絡(luò)波紋誤差,具體方法如下:將理想齒面 F(θ,ζ)的參數(shù) θ 與 ζ 在其取值范圍內(nèi)離散形成網(wǎng)格,網(wǎng)格區(qū)域面積設(shè)置為 m×l,步長設(shè)置為 Δθ 與 Δζ。用上標(biāo) m、l 對網(wǎng)格上離散點進行編號,F(xiàn)(θ,ζ) 在離散點(θm,ζl)的法向矢量表示為 ni(θ m,ζ l),其法向誤差表示為 hi(θm,ζ l)。
圖 2 為法向誤差計算示意圖,由圖中可知,理想齒面 F(θ,ζ)上離散點(θm,ζl)的法向矢量 ni(θm,ζl)會先后穿過不同的掃掠面,因此法向誤差值需分別計算 F(θ,ζ)的法向量與各個掃掠面之間的法向距離,取其中的最小值即為齒面的法向誤差值 hi(θm,ζl)。
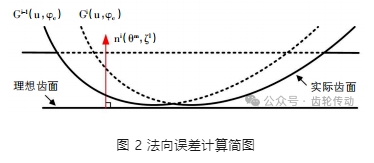
三、齒面包絡(luò)波紋誤差影響因素分析
影響車齒加工質(zhì)量的因素有很多,主要包括刀具幾何參數(shù)、切削參數(shù)、設(shè)備因素、環(huán)境因素等。本文對車齒加工過程中不同軸向進給量 f、刀具螺旋角 βc 和刀具前角 γ0 下成形齒面微觀形貌進行數(shù)值仿真計算,車齒刀和工件的設(shè)計參數(shù)如表 1 和表 2 所示。
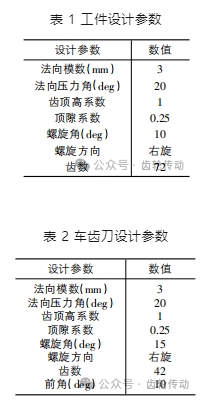
各車齒工藝參數(shù)對齒面法向誤差的影響規(guī)律如圖 3、圖 4 所示。由圖可知,在試驗參數(shù)范圍內(nèi),保持刀具螺旋角或刀具前角不變的情況下,隨著軸向進給量的增大,齒面最大法向誤差值 Rmax 隨之增大,且變化幅值較大。這是由于軸向進給量的增加會導(dǎo)致刀具每齒切削厚度增大,波紋誤差的波距變大,刀齒在單位時間內(nèi)切除材料的體積隨之上升,切削力隨之增大,故表面粗糙度增加,表面形貌變差。
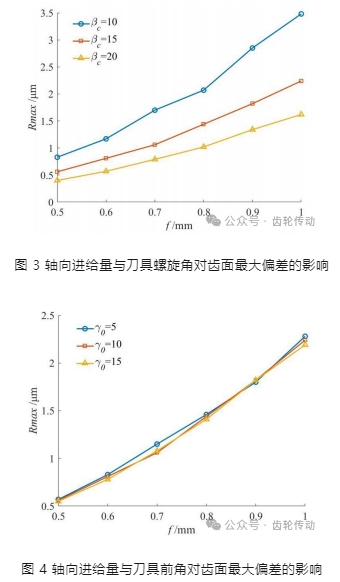
由圖 3 可知,隨著刀具螺旋角的增大,齒面最大法向誤差值 Rmax 隨之減小,且變化幅值較大。這是由于刀具螺旋角增大,軸交角隨之增大,增大軸交角可以提高刀刃切削性能,改善切削條件,從而降低表面粗糙度。但軸交角增大會減小接觸區(qū)域?qū)挾?,過大的軸交角反而會對加工精度產(chǎn)生不利影響,因此實際加工時需要綜合考慮多種因素以選擇合理的軸交角。
由圖 4 可知,隨著刀具前角的增大,齒面最大法向誤差值 Rmax 出現(xiàn)振蕩趨勢,但是振幅比較小且沒有明顯變化,可以認為刀具前角對理論加工誤差影響較小,基本可以忽略不計。
四、結(jié)論
本文為了研究車齒工藝中加工誤差的影響因素,通過分析車齒工藝原理,建立了車齒加工過程中切削刃空間軌跡曲面數(shù)學(xué)參數(shù)模型,然后采用離散網(wǎng)格方法計算了齒面包絡(luò)誤差,在此基礎(chǔ)上分析車齒工藝參數(shù)對齒面包絡(luò)波紋誤差的影響程度。本研究得到如下結(jié)論:①軸向進給量和刀具螺旋角對齒面包絡(luò)波紋誤差有較顯著的影響,刀具前角對包絡(luò)波紋誤差的影響較小;②通過增大刀具螺旋角或者減小軸向進給量可以提高車齒加工精度。
參考文獻略.