一、尿素泵齒輪介紹及加工工藝
尿素齒輪泵為外嚙合齒輪泵,他是依靠主動(dòng)齒輪帶動(dòng)從動(dòng)齒輪的旋轉(zhuǎn)使入口與出口的容積變化實(shí)現(xiàn)尿素水溶液的吸入與排出的液壓泵,如圖1所示;
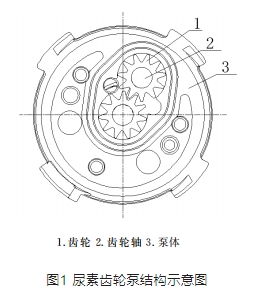
齒輪是外嚙合齒輪泵的核心部件,齒輪材料通常需要選擇耐磨性好、抗變形能力高的材料,常用材料有鋼、鑄鐵以及非金屬材料等,能夠滿足傳統(tǒng)齒輪泵的應(yīng)用。但尿素泵與傳統(tǒng)齒輪泵不同,因尿素水溶液具有腐蝕性,故尿素泵齒輪要求耐腐蝕。相比于金屬齒輪,塑料齒輪具有成本低、重量輕、耐腐蝕、自潤(rùn)滑性好、傳動(dòng)噪聲低等優(yōu)點(diǎn),為此, 本文齒輪選擇PEEK (聚醚醚酮)塑料,PEEK是一種半晶態(tài)的高分子聚合物,不僅具有耐高溫、耐磨損、耐化學(xué)腐蝕和綜合力學(xué)性能等特性, 還具有低吸水性、高韌性和耐沖擊性。
塑料齒輪制造工藝分為非切削加工和切削加工:(1) 非切削加工,如注塑、模壓成型等,適用于批量大、尺寸精度低的塑料齒輪;(2)切削加工,通常由塑料齒輪經(jīng)車(chē)削、銑削、插齒或滾齒等加工,達(dá)到尺寸精度和表面粗糙度要求,但效率較低。尿素泵齒輪如圖2所示,齒輪相對(duì)于軸的圓跳動(dòng)為0.03、齒輪面的粗糙度為 Ra0.8,精度要求較高;為了滿足該塑料齒輪精度要求,本文結(jié)合非切削加工和切削加工的優(yōu)缺點(diǎn),設(shè)計(jì)一套塑料齒輪精密切削夾具。
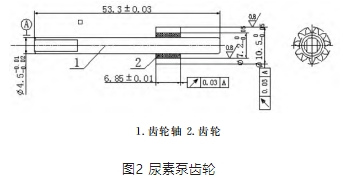
二、塑料切削原理及切削夾具結(jié)構(gòu)
塑料切削原理
塑料的切削過(guò)程是指通過(guò)切削運(yùn)動(dòng),使刀具從工件上切除多余的塑料層,形成切屑和已加工表面的過(guò)程,塑料的切削過(guò)程是擠壓過(guò)程。如圖3所示,當(dāng)使用前角 γ0 和后角α0的切刀切削塑料工件時(shí),被壓的塑料開(kāi)始產(chǎn)生彈性變形,而后是塑性變形;當(dāng)壓力達(dá)到塑料的剪切強(qiáng)度時(shí),則沿著滑移面 OA 在 OMA 區(qū)內(nèi)滑移,切刀繼續(xù)運(yùn)動(dòng), 促使鄰近刀刃附近的塑料發(fā)生變形,直至在刀刃前沿發(fā)生斷裂,形成切屑。本文塑料齒輪加工屬于成形法加工齒輪,將切削刀具加工成齒輪形狀,對(duì)毛坯塑料齒輪進(jìn)行一次精密切削成型。
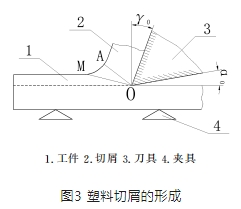
切削夾具結(jié)構(gòu)
本塑料齒輪精密切削夾具可用小型沖床進(jìn)行切削,切削夾具結(jié)構(gòu)如圖4所示,將需加工的工件夾在下壓滑塊下和限位塊之間進(jìn)行定位,通過(guò)切削塊上下的滑動(dòng)對(duì)工件進(jìn)行切削。
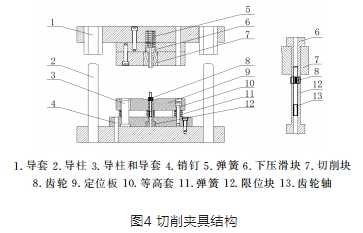
對(duì)加工精度要求較高的塑料零件,粗、精加工應(yīng)分開(kāi)進(jìn)行。即粗銑時(shí)按效率優(yōu)先的原則,盡可能在允許的變形范圍內(nèi)選擇能提高生產(chǎn)效率的加工參數(shù),但必須保證留 0.1 mm 左右的加工余量用于精加工。本文中齒輪精密切削前,是先通過(guò)模具注塑成齒輪毛坯,齒輪軸作為嵌件被一同注塑,毛坯齒輪整體外形尺寸比圖紙單邊大0.1mm。在切削前要先定位,由于齒輪泵齒輪隨著齒輪軸轉(zhuǎn)動(dòng),為了保證齒輪形位公差的精度要求,以齒輪軸作為定位基準(zhǔn)。定位過(guò)程如下步驟:
1、如圖5所示,定位板上和限位塊加工成齒輪狀,兩者間隙配合,齒輪軸一端先裝入限位塊的內(nèi)孔,一半齒輪則嵌入定位板的齒輪槽內(nèi);
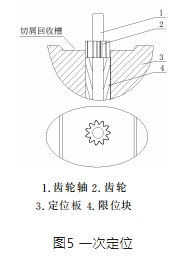
2、如圖6所示,機(jī)床下壓,齒輪軸的另一端插入下壓滑塊的內(nèi)孔,同時(shí)下壓滑塊在彈簧的作用下頂住齒輪進(jìn)行二次定位。
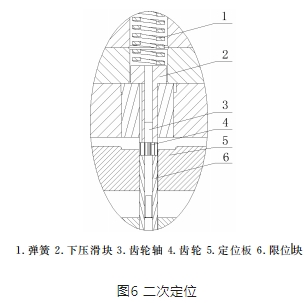
工件定位后進(jìn)行切削,切削過(guò)程如下步所示驟:
1、如圖7 ,隨著機(jī)床下壓過(guò)程,切削塊開(kāi)始切削齒輪。
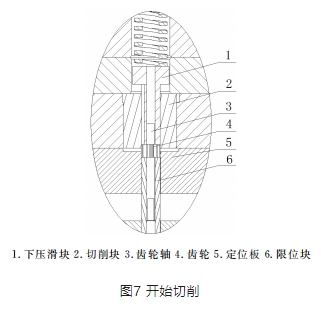
2、如圖8所示,機(jī)床繼續(xù)下壓,帶動(dòng)定位板下降,限位塊連同齒輪則一同頂入切削塊的切削孔內(nèi),這時(shí)切削完成,切削廢料則落入切屑回收槽內(nèi)。
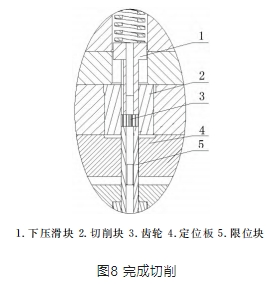
最后夾具分開(kāi),由彈簧推動(dòng)下壓滑塊將加工好的齒輪從切削塊中頂出進(jìn)行卸料,定位板則在底部彈簧的作用下復(fù)位。
三、夾具的主要工作零件的設(shè)計(jì)
切削塊
切削塊的結(jié)構(gòu)如圖9所示,齒輪的加工精度主要由切削塊決定,如果切削刃發(fā)生磨損,或齒輪孔內(nèi)壁粗糙等, 都會(huì)使齒輪工件表面粗糙,甚至造成齒輪開(kāi)裂,故要求切削塊具有較高的硬度和粗糙度較低的切削工作面;同時(shí)熱塑性材質(zhì)的硬度低,需要的切削力小,所以應(yīng)選擇容易磨出鋒利刀具刃口的刀具材質(zhì),如經(jīng)過(guò)淬火的碳素工具鋼、高速鋼、合金工具鋼和鎢鈷類硬質(zhì)合金,需要精密加工時(shí)可選金剛石車(chē)刀。本夾具切削塊選用鎢鋼(合金工具鋼)制造。
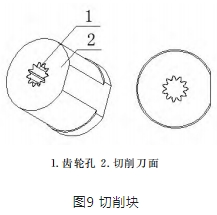
由于切削塊在下壓滑塊和限位塊之間滑動(dòng),沿齒輪一整圈做切削加工,為此切削塊后角α0=0比較適宜。切削塊前角γ0的大小直接影響切削效果,其大小的選擇應(yīng)綜合考慮塑料種類、刀具材料以及加工性質(zhì)三方面的因素。前角的大小主要解決刀頭的堅(jiān)固性與鋒利性的矛盾。因此首先要根據(jù)加工材料的硬度來(lái)選擇前角。加工材料的硬度高,前角取小值,反之取大值。其次要根據(jù)加工性質(zhì)來(lái)考慮前角的大小,粗加工時(shí)前角要取小值,精加工時(shí)前角應(yīng)取大值。前角一般在-5°~ 25°之間選取。本文在保證齒輪精度和切削塊強(qiáng)度的情況下,選擇切削塊前角γ0=0。
切削塊的齒輪孔用慢走絲加工,加工表面的粗糙度的范圍在 Ra0.2-0.3μm 之間,外形和尺寸按工件圖紙要求;另外切削塊切削平面可用工藝磨床精加工,加工后其表面粗糙度同樣可達(dá)到 Ra0.2-0.3μm;經(jīng)上述加工方法加工切削塊,其切削刃較鋒利;切削塊切削工件的表面則平整、光滑。
下壓滑塊和限位塊
下壓滑塊和定位塊如圖10所示,主要作定位用途是通過(guò)定位工件來(lái)配合切削塊切削,因承受擠壓和沖擊,故要有一定的硬度和耐磨性,可選用 Cr12MoV 制造,淬火硬度 HRC58-62;下滑塊和限位塊用淬火后的 Cr12MoV 進(jìn)行慢走絲加工,加工成齒輪條狀,與底座過(guò)盈配合,然后焊接牢固后磨平焊點(diǎn)。切削時(shí),齒輪軸兩端分別穿入限位塊和下壓滑塊的內(nèi)孔,齒輪軸的尺寸為 Φ4.5,為了保證齒輪相對(duì)于齒輪軸的同心度, 內(nèi)孔尺寸比齒輪軸單邊大 0.05mm;為了便于安放齒輪和齒輪軸穿入下壓滑塊,限位塊和下滑塊的內(nèi)孔端口處做斜倒角0.1mm× 0.5mm。
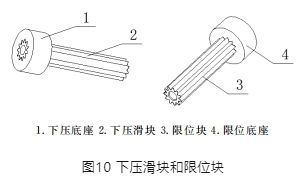
精密切削間隙
如圖11所示,限位塊托起毛坯齒輪,切削塊由上往下滑動(dòng),限位塊需要穿入切削塊進(jìn)行完全切削,如果限位塊齒輪形外形尺寸過(guò)小,切削時(shí)則會(huì)引起塑料齒輪塌角、開(kāi)裂;由參考文獻(xiàn)可知,沖壓切削凸凹模雙邊間隙應(yīng)小于0.01mm,但從切削夾具制造裝配精度和使用壽命考慮,該要求過(guò)高。根據(jù)生產(chǎn)實(shí)踐可知 ,只要切削塊和限位塊之間單邊邊間隙不超過(guò)0.02mm 就能保證齒輪精度和工件無(wú)塌角、無(wú)開(kāi)裂。
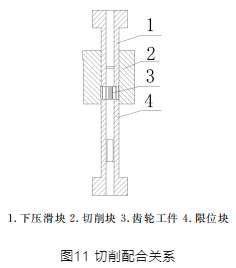
如圖12所示,切削過(guò)程中,切削塊在下壓滑塊上進(jìn)行滑動(dòng),切削完成后,下壓滑塊將切削塊齒輪孔內(nèi)的工件進(jìn)行頂出脫料,為了保證切削塊和下壓滑塊之間滑動(dòng)平順, 兩者之間間隙約為單邊0.1mm;同理,如圖9所示,為了保證限位塊和定位板之間滑動(dòng)平順,兩者之間間隙同樣為單邊0.1mm。
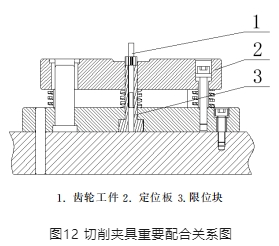
四、結(jié)論
本文運(yùn)用塑料切削原理,結(jié)合塑料齒輪特點(diǎn),設(shè)計(jì)了一副塑料齒輪精密切削夾具。該齒輪已經(jīng)量產(chǎn),而該夾具自使用以來(lái),所切削的齒輪表面光潔且無(wú)塌角、無(wú)開(kāi)裂,且與齒輪的圓跳動(dòng)小于0.03mm,滿足尿素齒輪泵的技術(shù)要求。生產(chǎn)結(jié)果表明,該精密切削夾具結(jié)構(gòu)原理正確、零件設(shè)計(jì)與選材合理、夾具使用穩(wěn)定性高和工作效率高。
參考文獻(xiàn)略.