近些年,風電等清潔能源的快速發(fā)展對鋼鐵材料提出更高的要求. 由于風電機組常服役于高山、低谷等風能資源豐富但環(huán)境惡劣的地區(qū),維護成本高昂,因此,保證其關鍵部件的可靠性尤為重要.風電齒輪是風電機組正常運行的重要傳動部件.感應淬火技術作為一種金屬冶金加工有效的強化方式,憑借其清潔、高效的優(yōu)勢,對碳中和等產(chǎn)業(yè)發(fā)展產(chǎn)生積極影響。
良好的溫度均勻性是獲得沿齒廓均勻分布的硬化層以及全齒寬均勻淬硬的前提,也是保障齒輪表面強化質(zhì)量的重要條件. 然而,目前齒輪的感應淬火較難獲得理想的硬化層,齒根位置以及端面位置是熱處理的薄弱區(qū)域,容易產(chǎn)生軟點和淬火軟帶,風電等重載齒輪更是如此,當齒輪發(fā)生偏載時,輪齒的兩端未硬化區(qū)極易發(fā)生開裂失效. 因此,實現(xiàn)全齒寬硬化是提高齒輪使用性能的重要途徑. Lusgin 等在鑄鐵熔煉的多頻加熱中,改變現(xiàn)有低高頻電流功率的調(diào)節(jié)方法,實現(xiàn)對熔池加熱和金屬運動的靈活控制. 王寧等發(fā)現(xiàn)感應加熱能夠明顯提高加熱速率,并有效解決在加熱過程中溫降的問題. Sung 等發(fā)現(xiàn)采用相鄰方向相反的兩種線圈均勻加熱工具鋼表面,可使表面具有更均勻的溫度分布. Kierepka 等利用雙頻諧振逆變器改變形狀不規(guī)則復雜元件的磁場穿透深度,從而達到控制加熱過程的目的. Min 等研究發(fā)現(xiàn)不同的材料性能參數(shù)對感應加熱過程有著不同的影響;感應焊管焊接生產(chǎn)中,受加熱參數(shù)影響,焊縫表面沿壁厚形成沙漏狀溫度場;橫向磁通感應加熱可以有效加熱連鑄和熱軋之間的板坯表面,選擇合適的參數(shù)可使溫度分布更加均勻. Barglik 等將連續(xù)雙頻淬火 ( consecutive dual frequency induct harding,CDFIH)工藝應用在齒輪的高頻節(jié)能輪廓淬火中,并提出數(shù)學模型能夠對硬化溫度及硬度進行有效預測,獲得齒輪的完全硬化區(qū)域的齒廓形狀. Barglik 等認為短時高功率感應加熱有利于提高齒面硬化層厚度均勻性. Su 等對一種新開發(fā)的兩步感應加熱 ( double induction quenching,DIQ)方法進行研究,發(fā)現(xiàn)進行過 DIQ 處理的硬化層中存在陡峭的壓縮殘余應變。
隨著計算機技術的發(fā)展,計算機仿真技術越來越多被應用于制造領域,用以解決傳統(tǒng)方式較難完成以及實驗成本較高的工作與研究.感應加熱的計算機仿真有助于明確工件內(nèi)的磁場、溫度場、功率分布等情況,進而明確加熱區(qū)域溫度相關影響,建立經(jīng)驗公式等.相較于實驗方式,計算機仿真具有實施靈活、周期短的特點,并且可以探究實驗較難發(fā)現(xiàn)的工件內(nèi)部演變情況.周丹等利用 ABAQUS 模擬軟件,準確地預測球扁鋼感應加熱過程中截面溫度場變化,并且預測結果可作為球扁鋼感應加熱工藝參數(shù)優(yōu)化的參考;肖瑤等利用有限元軟件 ANSYS 以及專用焊接軟件 SYSWELD 進行中頻組織場模擬,得出加熱后焊管焊縫附近的組織分布.將運動考慮在內(nèi)的感應加熱有限元模型可以得到更精確的數(shù)值結果,通過計算機模擬仿真的方式進行風電齒輪感應加熱過程預測與研究,有利于提升研究效率,降低成本.
然而,目前專門針對感應加熱過程中金屬工件的溫度分布和變化的研究相對較少.實現(xiàn)齒輪等材料感應加熱的精確控制,明確其存在的溫度分布形式及原因對生產(chǎn)精品鋼鐵具有積極意義.本文研究大模數(shù)風電齒輪掃描感應加熱沿齒廓和齒寬方向的溫度分布與溫度場均勻性,為研究全齒寬硬化提供了有效手段,為適應未來風電產(chǎn)業(yè)的快速發(fā)展對高端齒輪的需求提供理論參考.
一、有限元模型
本文以一風電機組齒輪箱齒圈為仿真對象,齒輪模數(shù) m = 16,齒數(shù) z = 95,齒寬 b = 200 mm.所用感應器為Π形感應器,圖 1 為Π形感應器電流走向和實體結構,其中 hπ = 10 mm,dmπ = 20 mm,hπ0 = 40 mm.冷卻采用在感應器端部增加噴淋孔的方式,根據(jù)感應器的實體結構可以得到該熱處理過程的掃描速度為 3. 8 mm/s.掃描感應淬火的電參數(shù)均為用示波器測量感應線圈接線柱得到的,相關參數(shù)如表 1 所示.所用電源為 IGBT 晶體管變頻電源,額定輸出功率為 250 kW.
齒輪材料為 42CrMo,加熱時珠光體向奧氏體轉變的溫度 AC1為 718 ℃,鐵素體向奧氏體轉變的終了溫度 AC3為 775 ℃.感應加熱過程中,材料的磁導率、電阻率決定了渦流產(chǎn)生的過程,熱導率、比熱容則決定了傳熱過程.針對這 4 個與溫度相關的重要物性參數(shù),本模型采用查表法進行非線性變化的計算.
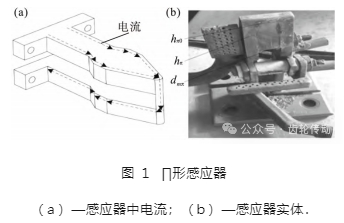
圖 2 為∏形感應器原理圖與齒輪的有限元模型.在中頻感應加熱中,所用頻率為 6 000 Hz,計算得到波長為 5 × 104 m,波長遠大于所研究工件的幾何尺寸.本文采用∏形感應器進行感應加熱,其工作原理如圖 2a 所示.感應器的兩側形成一個完整的電流環(huán),感應器放置于兩齒之間,在齒輪上產(chǎn)生相應的渦流區(qū).為了確保仿真結果的準確性同時節(jié)省計算成本,對齒輪進行如圖 2b 所示的網(wǎng)格劃分.將滲透層中的網(wǎng)格進行精細劃分,并在加熱層與基體之間添加過渡層.由于加熱時感應器靠近輪齒表面,在掃描加熱過程中很難準確測量到加熱表面溫度,故采用感應淬火相變層深度測量實驗來驗證該動態(tài)仿真過程.
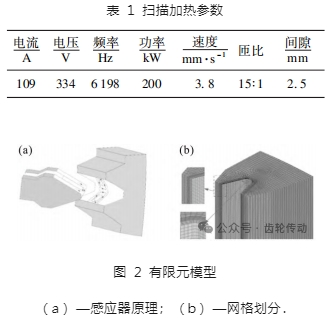
在此工藝參數(shù)下,掃描至齒寬中部加熱穩(wěn)定狀態(tài)的相變層宏觀形貌如圖 3 所示,以感應器完全駛入齒輪開始計算,所截取齒輪截面位置為距離駛入端面 100 mm 處.其中,δm ,δrl,δe,δrr分別表示側向齒廓、左側齒根圓角、齒根中部,以及右側齒根圓角處的最小相變層深度.
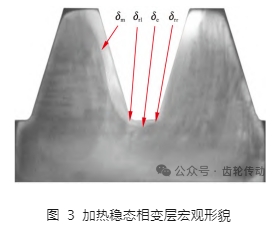
位置不同,相變層深度也不同.側向齒廓位置與齒根處相變層距離分別達到 3 mm 與 2 mm,深度分別為 δm =3. 38 mm, δe = 2. 10 mm.而兩側齒根圓角位置,相變層深度則分別為 δrl = 1. 65 mm,δrr = 1. 40 mm.左右兩側齒根圓角處相變層深度不一致,主要原因在于執(zhí)行設備的運行偏差,導致感應器與兩側齒廓間隙存在誤差從而使加熱結果產(chǎn)生差異.同時,由于感應器噴淋孔的結構不能夠保證完全對稱導致冷卻的不同,也會影響相變的結果.
在沿齒溝逐齒感應淬火中,端部淬火質(zhì)量較薄弱.圖 4 所示為試件的不同位置截面,齒輪端面為起始位置,l1 ,l2 ,l3 ,l4 分別表示相應截面與齒輪端面的距離,其中,l1 = 5 mm,l2 = 10 mm,l3 = 15 mm,l4 = 20 mm.運動參數(shù)引入后,將使加熱過程發(fā)生改變,因而需再次對模型進行驗證與修正.齒輪端部的冷卻在整個齒寬處理中屬于較佳區(qū)域,而加熱結果較差.因此取 l1 處截面位置進行分析,該位置冷卻充分使組織保存良好.
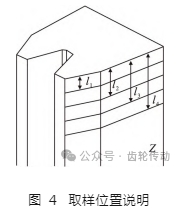
對試件打磨拋光后,使用 4% 硝酸酒精溶液腐蝕表面,獲得如圖 5a 所示相變層形貌.對修正后模型的計算結果,截取相同位置的溫度場,獲取圖 5b 所示云圖.結果顯示,側向齒廓位置相變層深度顯著大于齒根及圓角處.齒輪材料 42CrMo 的相變起始溫度為 718 ℃,以此為判據(jù)測量仿真云圖中的加熱層深度.齒廓方向不同位置的加熱層深度及相變層深度如表 2 所示.
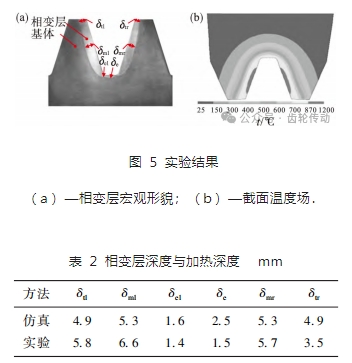
圖 5a 及表 2 均顯示,實驗獲得的相變層具有顯著的偏移現(xiàn)象,而仿真結果則具有良好的對稱性.設備運行偏差在齒輪端部位置的影響尤其劇烈.因此將實驗數(shù)據(jù)兩側對應位置的平均值,作為分析數(shù)據(jù).在此,齒頂?shù)南嘧儗由疃葹?4. 65 mm,中部相變層深度為 6. 15 mm,左側齒根圓角相變深度為 1. 60 mm,齒根相變層深度為 2. 50 mm.仿真結果與此相比,齒頂位置偏差 5. 38% ,中部位置偏差 7. 30% ,齒根圓角處偏差 0% .而齒根處偏差較大,達到 66. 60% ,這是由于感應器為圖 1b 所示結構,引發(fā)的冷卻不足所導致的.綜上認定,本文所建立的風電齒輪移動感應加熱模型可以進行相關研究.
二、移動加熱效果分析
在齒輪的逐齒掃描感應加熱中,齒輪兩側端部位置及中間部位的溫度分布及演化過程存在較大差異.對齒輪端部及中間位置的齒廓方向溫度分布,以及齒寬方向上的溫度場進行研究,揭示移動加熱的效果.為加熱質(zhì)量的預測以及工藝優(yōu)化提供了參考依據(jù).
相對溫度浮動率分析
在風電齒輪的移動感應加熱過程中,由于感應器為上下兩層線圈結構,導致同一位置先后經(jīng)歷了預熱與加熱兩個過程.同時,在輸入功率與頻率一定的情況下,齒輪的表面溫度可反映一定深度內(nèi)的加熱溫度.因此,對于不同的分析截面,獲取整個加熱過程中表面上各位置的最高溫度記為 “綜合溫度”,以綜合溫度作為判定加熱效果的基礎數(shù)據(jù).
對于齒廓方向,根據(jù)齒輪的特殊幾何結構,建立由齒頂中點為起點,沿齒輪表面終止于齒根中點的路徑.所建立的路徑位于圖 4 所示的取樣截面上.以平均溫度與路徑上的最大溫度差 Δtmax作為加熱結果判定指標,其數(shù)據(jù)來源于節(jié)點上的綜合溫度.
對于齒寬方向,由于齒根位置加熱狀態(tài)相對穩(wěn)定,因此對側向齒廓的溫度加熱結果進行分析.建立如圖 6 所示的路徑,因加熱過程中的對稱性,選取一側齒廓作為研究對象.圖 6 所示的路徑位 于齒輪的一側齒廓表面,LA - LA ,LB - LB,LC - LC 三條分析路徑均與齒頂?shù)睦膺吰叫?路徑完整地貫穿齒輪兩側,起于齒輪端面,經(jīng)過側向齒廓,終于另一端面.
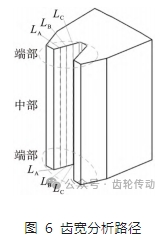
對于齒寬方向上的溫度分布,除經(jīng)綜合溫度計算的平均溫度 及最大溫度差 Δtmax外,引入相對溫度浮動率 Ut 作為另一判斷指標.Ut 的定義 如式(1)所示.路徑在齒寬中間部分的數(shù)據(jù)點選取數(shù)量,與兩側端部的數(shù)量相同.相對溫度浮動率 Ut 的數(shù)值越大,則表示齒輪兩端與中部的差距越大,溫度在齒寬方向上的溫度分布均勻性越差.

式中:tmax為齒寬路徑上的溫度最高值;tmin為齒寬路徑上的溫度最低值.
入口端加熱效果分析
圖 7 為截面齒廓方向溫度變化.以圖 4 所示取樣位置,獲取完整加熱過程中每個齒廓上節(jié)點的綜合溫度.齒輪入口端部位置的綜合溫度分布如圖 7a 所示.在 l1 = 5 mm 截面位置,齒廓側邊的綜合溫度顯著高于其他截面,而齒根處溫度則低于其他截面.原因在于齒輪端部具有的棱邊結構,導致邊部磁場集中,同時向外傳熱較小.而對于齒根及附近位置,由于 l1 = 5 mm 截面距離端面較近,使得此處磁力線逸散嚴重.在 l2 = 10 mm 截面到 l4 = 20 mm 截面位置,最高溫度產(chǎn)生于齒根處,而齒根圓角位置溫度則相對較低.原因則在于導磁體的驅磁作用使齒根磁力線集中,同時因導磁體的缺口,使得圓角附近的磁力線較少.
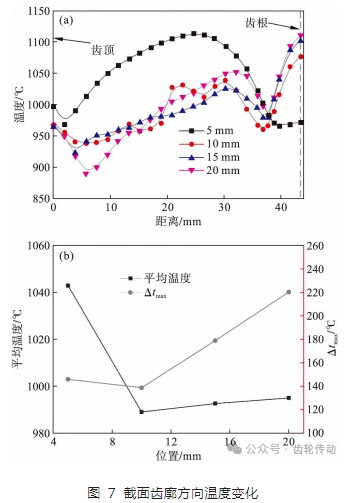
以圖 7a 中溫度數(shù)據(jù)為基礎,計算得到不同截面的平均溫度與最大溫度差 Δtmax結果如圖 7b 所示.在 l1 = 5 mm 截面處的平均溫度顯著高于 l2 = 10 mm 至 l4 = 20 mm 截面處.由 l2 = 10 mm 向l4 = 20 mm 截面位置靠近,平均溫度有小幅度的升高.最大溫度差 Δtmax則先略有降低,而后顯著升高.原因在于,齒輪的棱邊使得靠近其位置截面的平均溫度明顯更高.隨著位置由 l2 = 10 mm 截面繼續(xù)深入,區(qū)域的保溫效果較好,導致平均溫度略有上升.
對于遠離齒輪端面的 l2 = 10 mm 截面和 l4 = 20 mm 截面,不同位置的加熱深度如表 3 所示.其中,δt,δm,δr,δe 分別表示齒頂、齒側、齒根圓角以及齒根的加熱深度.在不同截面中,齒根圓角處均為深度最小位置.在加熱達到運動穩(wěn)態(tài)之前,隨著遠離齒輪端面,加熱深度逐漸降低.齒根圓角處不但是強化的薄弱區(qū)域,同時還是加熱的薄弱區(qū).
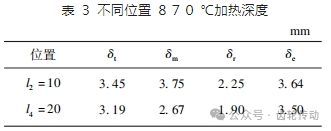
穩(wěn)態(tài)齒廓加熱效果分析
感應器運動至齒輪中部達到加熱穩(wěn)態(tài)時,任一截面在一個完整的感應器掃描加熱歷程中,其加熱過程皆相同.因此,對于加熱穩(wěn)態(tài),只需選取一截面進行分析.截面上的綜合溫度分布如圖 8 所示.
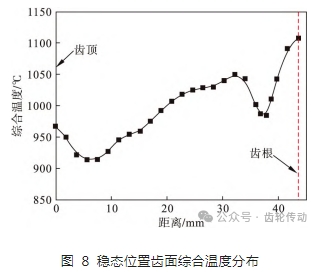
在整個加熱歷程中,截面的溫度最大值出現(xiàn)在齒根位置.整個截面上的平均溫度 為995. 9 ℃,最大溫度差 Δtmax達到 194 ℃.穩(wěn)態(tài)位置截面遠離齒輪端面,最低溫度由 890 ℃上升為 914 ℃,而最高溫度幾乎維持不變.914 ℃ 產(chǎn)生于第二層線圈掃描加熱時,原因在于穩(wěn)態(tài)位置時感應器運動的后方和前方溫度整體較高,同時前方未加熱區(qū)域熱梯度降低.
當感應器運動達到加熱穩(wěn)態(tài)時,溫度場三維等值面情況如圖 9 所示.齒根部分的高溫區(qū)域覆蓋范圍顯著高于齒側位置.同時,雖然高溫區(qū)域達到穩(wěn)定的加熱狀態(tài),但較低的溫度范圍仍存在明顯的向齒端滯后的現(xiàn)象.滯后現(xiàn)象持續(xù)的時間隨等溫線下限的降低而不斷延長.
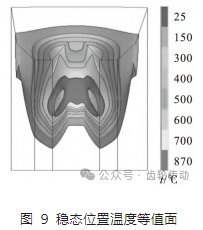
在加熱深度方向,生熱情況將反向影響加熱結果,齒輪內(nèi)部對應位置與表面溫度的差值是最直接的體現(xiàn).圖 10 為深度方向溫度圖,如圖 10a 所示分別在齒頂、齒中、齒根以及齒底位置取分析節(jié)點,計算表面與內(nèi)部溫度差,取樣深度為 3 mm.D1 - D1、D2 - D2、D3 - D3 及 D4 - D4 位置的溫度差值隨時間變化如圖 10b 所示.其中,起始時間為截面出現(xiàn) 870 ℃高溫區(qū)域時。
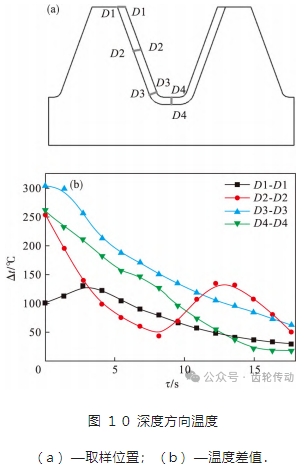
如圖 10b 所示,齒根位置 D4 - D4,齒根圓角位置 D3 - D3 的內(nèi)外溫度場 Δt隨著溫度的升高而穩(wěn)步降低.原因在于兩處位置對應的感應器連續(xù),加熱始終連續(xù)穩(wěn)定進行,持續(xù)的加熱使溫度越來越均勻.D3 - D3 處的溫差波動幅度最大,達到 79. 5%.齒頂 D1 - D1 的表面與內(nèi)部溫差首先升高,而后逐漸降低.原因則在于初始加熱時能量在表面集中,而隨著加熱進行,劇烈的感應加熱層不斷向內(nèi)移動.而側向齒面中部的 D2 - D2 位置,由于感應器在齒寬的不連續(xù),導致溫度差 Δt 發(fā)生起伏.同時,由于感應器側邊結構在齒寬方向上的不連續(xù),導致掃描加熱過程與靜態(tài)產(chǎn)生差異.因此,側向齒廓溫度有所降低.
齒寬加熱效果分析
風電齒輪的掃描感應強化,全齒寬高質(zhì)量淬硬始終是風電齒輪熱處理的技術難題.優(yōu)異的加熱質(zhì)量是獲取高質(zhì)量強化結果的前提,因此采用如圖 6 所示分析路徑,以綜合溫度作為分析溫度,對齒寬方向的加熱效果進行分析,以期為齒寬方向加熱質(zhì)量的提升提供研究基礎與依據(jù).
圖 11 分布.其中為在齒寬方向上 3 條路徑的綜合溫度,入口端表示感應器駛入位置的齒輪端面,出口端表示感應器駛出位置齒輪的端面,圖中橫坐標表示與入口端之間的距離.3 條分析路徑在齒寬中部的溫度分布較為平穩(wěn),而在兩端面溫度有顯著變化.在距離兩端面 15 mm 附近位置,溫度有顯著的降低,繼續(xù)遠離則稍有回升.齒輪端面的棱邊結構,是其溫度更高的直接原因.而熱量的向內(nèi)快速傳遞,則導致銜接處溫度較低.并且由于感應器掃描加熱過程中,齒輪中熱量向其前方位置傳遞,導致端部溫度更早到達居里點溫度,因此 3 條路徑上出口端的溫度均低于入口端位置溫度.
綜合溫度的最大溫度差在 LA - LA 路徑上達 到 133 ℃,LB - LB 路徑上為 121. 11 ℃,LC - LC 路徑上為 86 ℃.由此可見,齒形幾何結構在端面對加熱結果的影響貫穿整個加熱過程.LA - LA ,LB - LB,LC - LC 3 條路徑上的溫度浮動率分別為 14. 3% ,12. 1% 以及 8. 3%.因此,齒寬方向上的加熱溫度結果,受齒形位置的影響較大.在齒側位置沿著齒寬方向,由齒頂向齒根方向的溫度均勻性不斷提升,原因在于齒形結構厚度的劇烈變化.
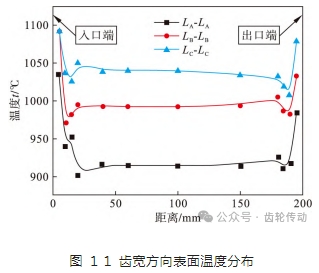
三、感應強化實驗研究
經(jīng)感應加熱的齒輪,再經(jīng)過急冷處理,將使其表層被強化,能夠極大地提升現(xiàn)有性能.在冷速達到臨界冷卻速度且冷卻充分的情況下,所獲得的相變層與加熱溫度層能夠較好地貼合.因此高溫區(qū)域溫度場邊界,可表示理想冷卻條件下的感應加熱淬火強化層.而對于淬硬深度,則根據(jù) GB/ T 5617—2005 規(guī)定,淬硬深度處極限硬度為零件表面所要求的最低硬度的 0. 8 倍.本節(jié)分別對齒輪相變情況,以及實際淬硬情況進行分析并觀察組織成分,以明確最終強化結果.本實驗中齒輪的表面硬度目標值為 HRC58 ~ 62.
相變層深度分析
不同截面位置的相變層變化如圖 12 所示.在各個截面位置,齒根圓角處的相變層深度均為最低.在靠近齒輪端部位置的 l1 = 5 mm 截面層,齒側中部相變層深度變化平緩,這與加熱結果及冷卻過程相契合.而隨著遠離端面,相變層發(fā)生較快改變,中部位置相變層深度發(fā)生顯著收縮.至 l4 = 20 mm 截面時,相變層達到穩(wěn)定狀態(tài).而齒根及圓角處,隨著遠離端面,由于設備運行偏差導致的影響降低.
而遠離端面位置的側向齒廓中部,加熱狀態(tài)相對穩(wěn)定,同時冷卻狀態(tài)相對穩(wěn)定,因而產(chǎn)生相似的相變形貌.在齒側中部位置,最高溫度相對較低并且高溫持續(xù)時間更短,因而深度下降.而齒頂?shù)睦膺吔Y構,則會導致加熱深度更大.同時結合感應器下方冷卻結構,產(chǎn)生圖 12 所示的結果。
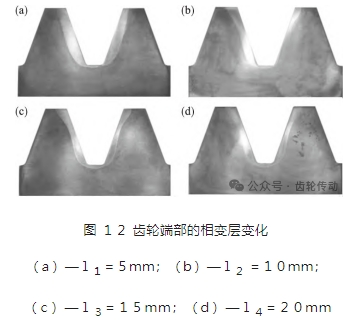
圖 13 為不同模數(shù)的齒輪逐齒感應淬火后的相變層形貌. 圖 13a 中齒輪模數(shù)為 14,圖 13b 齒輪模數(shù)為 20.兩齒輪側向齒廓靠近齒頂中上的位置,均如圖 12 中存在相似的相變層深度減小現(xiàn)象,圖 13a 中的減小現(xiàn)象相較于圖 13b 中的減小現(xiàn)象更為明顯.同時隨著模數(shù)增大,齒根及齒根圓角位置的相變層深度發(fā)生明顯的降低.
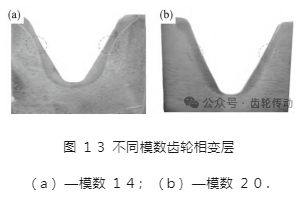
將模數(shù)為 16 的齒輪側向齒廓最小相變層深度 δm 繼續(xù)細化為左側最小相變層深度 δml,以及右側最小相變層深度 δmr。l1 至 l4 截面位置,其各處的相變層深度數(shù)值如表 4 所示.左側齒廓相變層深度在 l1 = 5 mm 時較大,達到了 δml = 5. 80 mm.其余位置穩(wěn)定在 3. 40 mm 附近,變化率 為 43. 1% .同樣,右側齒廓的相變層深度 δmr 由 3. 30 mm 逐漸降低至 2. 90 mm.而齒根處以及兩側齒根圓角位置,相變層深度則不斷增加.δrl 由 1. 16 mm 增加至 1. 83 mm,δe 由 1. 50 mm 增加至 2. 30 mm 附近,δrr由 0. 51 mm 增加至 1. 48 mm 附近.然而,在此參數(shù)進行模數(shù) 16 齒輪的感應處理時,齒根及圓角位置硬化層與加熱結果不完全匹配,原因在于感應器冷卻結構導致齒輪對應位置的冷卻不足.
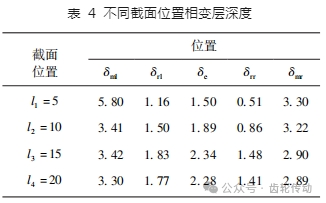
金相組織
圖 14 為實驗齒輪的金相組織照片.圖 14a 顯示 42CrMo 的原始組織為片狀珠光體和鐵素體組織.圖 14b 為經(jīng)感應淬硬后的金相組織,經(jīng)感應淬火后形成板條狀馬氏體組織.
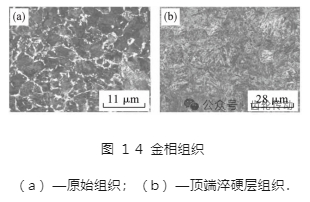
硬度分布
硬度是判斷齒輪淬火強化結果的一項重要指標,在硬化層內(nèi)應獲得相對均勻的硬度分布.測量硬度的硬度計為 TMHV - 30Z 維氏硬度計,硬度計通過接口與計算機連接,測量得到的數(shù)據(jù)可以 直接在計算機上轉換成洛氏硬度并讀取.為研究齒廓及深度方向的淬硬效果,建立圖 15 所示的 5 條分析路徑進行顯微硬度測定.其中路徑 HL1 - HL1 與齒廓平行,距離為 0. 5 mm. 路徑HL2 - HL2 與齒頂邊界平行,距離為 1. 35 mm.路徑 HL3 - HL3、HL4 - HL4 為與側向齒廓垂直向內(nèi)的路徑,與齒頂距離分別為14. 5 mm 和29 mm.HL5 - HL5 為與齒根中心位置垂直向內(nèi)的路徑.
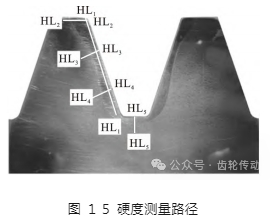
圖 16 為側向齒廓 HL1 - HL1 路徑與齒頂 HL2 - HL2 路徑的硬度分布.齒廓 HL1 - HL1 路徑硬度幾乎全部達到 58HRC 以上,符合硬度要求,并且硬度數(shù)值變化相對較小. HL2-HL2 路徑上,硬度在距離齒廓 5 mm 以內(nèi)相對穩(wěn)定,維持在較高數(shù)值.齒頂淬硬深度約為 6. 5 mm,小于相變層深度(7. 45 mm).
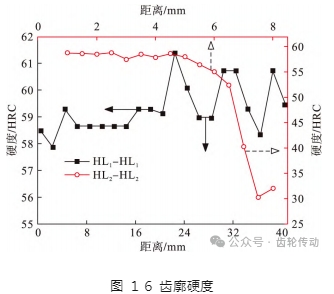
垂直于齒輪齒面的 HL3 - HL3 至 HL5 - HL5 路徑上的硬度分布如圖 17 所示.在 HL3 - HL3 路徑上,硬化層內(nèi)硬度較為穩(wěn)定,在交界處硬度有顯著降低.在 HL4 - HL4 路徑上的硬度從齒廓向內(nèi)較均勻地降低,同樣在齒根位置 HL5 - HL5 路徑上的硬度分布有相同的趨勢.
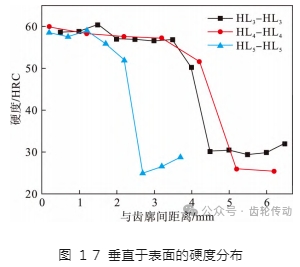
四、結論
1) 在入口端距離齒輪端面不同位置,溫度分布具有顯著差異,平均溫度與最大溫度差同樣具有明顯的波動情況.
2) 在齒寬方向中間部位達到加熱穩(wěn)態(tài),側向齒面在整個齒寬方向由齒頂至齒底的溫度均勻程度不斷提升,溫度偏差率最大可降低 6%.
3) 在穩(wěn)態(tài)位置經(jīng)感應淬火強化齒輪的齒廓方向,淬硬層深度整體上幾乎與宏觀相變層深度保持一致,過渡區(qū)域相對較窄.淬硬區(qū)形成細小的馬氏體組織,在相變交界區(qū)域存在明顯的過渡性組織結構.
參考文獻略.