大規(guī)格漸開(kāi)線(xiàn)圓柱齒輪在礦山、海洋、冶煉、能源等領(lǐng)域扮演著重要的角色,承擔(dān)著大功率、重載荷運(yùn)動(dòng)傳輸、能量傳遞等任務(wù)。齒廓偏差是衡量齒輪工作平穩(wěn)性的重要指標(biāo)。大規(guī)格齒輪制造工藝異常復(fù)雜,造價(jià)及其高昂。如何控制其加工工藝過(guò)程,保證成品率、提高加工質(zhì)量,一直是亟待解決的問(wèn)題。
傳統(tǒng)的齒廓偏差檢測(cè)方法主要是借助大規(guī)格坐標(biāo)測(cè)量機(jī)或?qū)S玫腃NC齒輪測(cè)量中心,如:Leitz公司的PMM-G、Zeiss公司的ACCURA系列、Gleason公司的GMS系列等。這種方法屬于離線(xiàn)測(cè)量,存在著兩個(gè)方面的缺陷。首先,離線(xiàn)測(cè)量法會(huì)不可避免地產(chǎn)生二次裝夾誤差,引起加工與測(cè)量基準(zhǔn)的不重合,從而導(dǎo)致加工精度的流失;第二,被測(cè)齒輪需要在機(jī)床與測(cè)量設(shè)備上往返轉(zhuǎn)運(yùn),而大規(guī)格齒輪體積大、重量大的特點(diǎn)會(huì)造成安裝找正難度大、操作勞動(dòng)強(qiáng)度大、工藝過(guò)程時(shí)效性差等問(wèn)題。集成在機(jī)測(cè)量技術(shù)的出現(xiàn)妥善解決了上述問(wèn)題,它將精密測(cè)量技術(shù)融入工件的制造工藝過(guò)程,在工件加工位置上檢測(cè)其加工誤差并進(jìn)行補(bǔ)償,實(shí)現(xiàn)了“加工-測(cè)量”的閉環(huán)制造模式,有效提高了加工精度及生產(chǎn)效率,實(shí)現(xiàn)了工藝過(guò)程的自動(dòng)化、智能化。近年來(lái),在機(jī)測(cè)量技術(shù)得到了廣泛的應(yīng)用,如齒輪、燃?xì)廨啓C(jī)轉(zhuǎn)子、大尺寸薄壁零件、渦輪、高精密非球面廓形等。
齒廓偏差的在機(jī)測(cè)量方法一直是各方的研究熱點(diǎn)。王燕玲等提出了一種采用齒條形刃邊測(cè)頭測(cè)量齒廓偏差的方法;段振云等提出了一種基于直母線(xiàn)族的齒輪在機(jī)測(cè)量方法。這兩種方法將測(cè)量?jī)x器定位在機(jī)床或齒輪上來(lái)完成測(cè)量,測(cè)頭定位精度不高,測(cè)量精度較低。高峰等應(yīng)用觸發(fā)式測(cè)頭在齒形磨齒機(jī)上實(shí)現(xiàn)了齒廓偏差的在機(jī)測(cè) 量;王志永等研究了螺旋錐齒輪齒形誤差的在機(jī)測(cè)量方法;喬衛(wèi)東等研究了大齒輪齒形掃描式在機(jī)測(cè)量的數(shù)據(jù)處理方法;這些方法均依靠機(jī)床自身的運(yùn)動(dòng)及位置檢測(cè)功能實(shí)現(xiàn)測(cè)量,充分發(fā)揮了機(jī)床的伺服控制功能。然而,機(jī)床各伺服軸不可避免的存在著幾何及運(yùn)動(dòng)誤差,會(huì)導(dǎo)致測(cè)量誤差。上述研究并未給出合理的測(cè)量精度提升解決方案。為此,Hartig. F等應(yīng)用激光跟蹤儀實(shí)現(xiàn)了大規(guī)格漸開(kāi)線(xiàn)齒輪齒廓及螺旋線(xiàn)偏差的測(cè)量;石照耀等詳細(xì)研究了基于激光跟蹤技術(shù)的特大型齒輪的在位測(cè)量方法,給出了測(cè)量定位模型及姿態(tài)調(diào)整模型;陳洪芳等研究了面向特大型齒輪的激光跟蹤多站為定位方法;這種測(cè)量方法利用激光絕佳的測(cè)距及跟蹤功能替代了機(jī)床的位置測(cè)量系統(tǒng),能夠更為精確地獲取齒面測(cè)點(diǎn)的位置信息,避免了機(jī)床幾何及運(yùn)動(dòng)誤差對(duì)測(cè)量結(jié)果的影響,擁有較高的測(cè)量精度。但是,激光光路易因遮擋而導(dǎo)致測(cè)量中斷,且其測(cè)距性能也易受溫度場(chǎng)變化而發(fā)生波動(dòng),導(dǎo)致測(cè)量精度降低。此外,激光跟蹤儀使用成本高昂、調(diào)試操作復(fù)雜,難以適應(yīng)加工現(xiàn)場(chǎng)大規(guī)模應(yīng)用的要求。綜上所述,探究一種充分發(fā)揮機(jī)床的運(yùn)動(dòng)及精度潛能、廣泛適合加工現(xiàn)場(chǎng)應(yīng)用并具備誤差補(bǔ)償修正功能在機(jī)測(cè)量方法是十分必要的。
為此,本文提出了一種基于機(jī)床自身運(yùn)動(dòng)及位置檢測(cè)功能大規(guī)格漸開(kāi)線(xiàn)齒廓偏差的集成在機(jī)測(cè)量及其誤差補(bǔ)償方法。建立了漸開(kāi)線(xiàn)螺旋面綜合測(cè)量模型;確定了測(cè)量方案;推導(dǎo)了機(jī)床幾何及運(yùn)動(dòng)誤差與測(cè)量誤差之間的映射關(guān)系;計(jì)算了各測(cè)點(diǎn)對(duì)應(yīng)的測(cè)量誤差;提出了測(cè)量誤差的后補(bǔ)償方法;最后,在一臺(tái)五軸數(shù)控成形砂輪磨齒機(jī)上進(jìn)行了齒廓偏差的在機(jī)測(cè)量及其補(bǔ)償實(shí)驗(yàn)。
一、在機(jī)測(cè)量方法
測(cè)量系統(tǒng)的組成
采用掃描測(cè)頭測(cè)量漸開(kāi)線(xiàn)齒廓時(shí),探針與被測(cè)齒面相接觸,數(shù)控系統(tǒng)控制測(cè)頭與齒輪以理論構(gòu)型曲線(xiàn)為目標(biāo)軌跡相對(duì)運(yùn)動(dòng)。若齒面存在加工誤差,則實(shí)際構(gòu)型曲線(xiàn)與理論構(gòu)型曲線(xiàn)編存在偏差,引起探針發(fā)生偏轉(zhuǎn),上位機(jī)將所有的偏轉(zhuǎn)量記錄下來(lái),再經(jīng)過(guò)數(shù)據(jù)處理即可得到被測(cè)齒輪的齒廓偏差。在機(jī)測(cè)量系統(tǒng)的構(gòu)成如圖1所示。
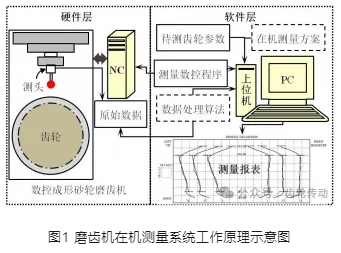
YK73系列數(shù)控成形砂輪磨齒機(jī)擁有六個(gè)伺服運(yùn)動(dòng)軸,如圖2(a)所示,分別為:立柱徑向進(jìn)給軸X、縱向砂輪進(jìn)給軸Z、齒輪分度軸C、螺旋角旋轉(zhuǎn)軸A、砂輪修形軸(齒輪切向)Y及砂輪修形軸(垂直方向)W。各伺服軸間的拓?fù)潢P(guān)系如圖2(b)所示,機(jī)床擁有“測(cè)頭-Y軸-A軸-Z軸-X軸-床身”及“床身-C軸-齒輪”兩個(gè)運(yùn)動(dòng)鏈。
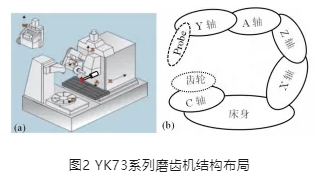
測(cè)量方案的分析與確定
數(shù)控機(jī)床擁有的伺服軸數(shù)往往多于在機(jī)測(cè)量方案所需的伺服軸數(shù),即一個(gè)在機(jī)測(cè)量方案會(huì)有多個(gè)在機(jī)測(cè)量運(yùn)動(dòng)控制方案。由于數(shù)控機(jī)床各伺服軸的的精度水平不盡相同,不同的測(cè)量方案會(huì)有測(cè)量精度的高低差異。確定合理的測(cè)量方案應(yīng)遵循以下準(zhǔn)則:
1)參與伺服軸最少原則
機(jī)床各伺服軸相互串聯(lián),測(cè)頭的軌跡受各軸及軸間的各種形式的誤差疊加耦合影響,產(chǎn)生測(cè)量誤差。因此參與測(cè)量運(yùn)動(dòng)的伺服軸越少越好;
2)重心偏移最小原則
機(jī)床伺服軸重心的偏移會(huì)引起機(jī)床的變形,產(chǎn)生幾何及運(yùn)動(dòng)誤差,進(jìn)而導(dǎo)致測(cè)量誤差。測(cè)量運(yùn)動(dòng)引起機(jī)床重心偏移最小的方案,為應(yīng)優(yōu)先選取的方案;
3)長(zhǎng)度基準(zhǔn)最短原則
由于長(zhǎng)導(dǎo)軌制造精度較難保證,特別是在機(jī)床上,工況復(fù)雜,長(zhǎng)導(dǎo)軌的精度流失更為嚴(yán)重。因此在確定測(cè)量方案時(shí),應(yīng)避免選取存在相對(duì)較長(zhǎng)線(xiàn)性移動(dòng)量的測(cè)量方案。
漸開(kāi)線(xiàn)齒廓的測(cè)量方案
常見(jiàn)的漸開(kāi)線(xiàn)齒廓測(cè)量方法,如圖3所示,包括直角坐標(biāo)法、展成法(法向極坐標(biāo)法)、嚙合線(xiàn)法、極坐標(biāo)法等。
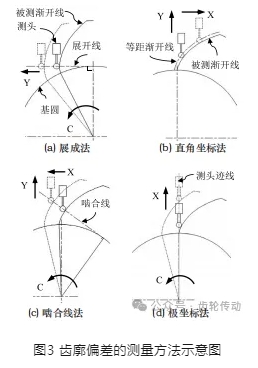
1)展成法(法向極坐標(biāo)法)
幾乎所有齒輪量?jī)x都采用該方法。測(cè)頭沿漸開(kāi)線(xiàn)的展成方向運(yùn)動(dòng)。機(jī)床提供回轉(zhuǎn)運(yùn)動(dòng)及高精度直線(xiàn)運(yùn)動(dòng)。展成法需要高精度直線(xiàn)導(dǎo)軌作為測(cè)量基準(zhǔn)。漸開(kāi)線(xiàn)規(guī)格越大,所需的直線(xiàn)導(dǎo)軌越長(zhǎng)。而高精、大規(guī)格的直導(dǎo)軌往往難以制造。并且,在機(jī)床的工況環(huán)境下,長(zhǎng)導(dǎo)軌的實(shí)際使用精度的保證往往是一個(gè)難題。此外,在YK73系列數(shù)控成形砂輪磨齒機(jī)上,漸開(kāi)線(xiàn)的展成方向?yàn)闄C(jī)床Y軸方向,而Y軸為砂輪修整成形軸,行程很短,無(wú)法滿(mǎn)足展成法的要求。因此展成法不適合作為在機(jī)測(cè)量方案。
2)直角坐標(biāo)法
測(cè)頭由機(jī)床直線(xiàn)軸X軸及Y軸帶動(dòng),探針球心軌跡為被測(cè)漸開(kāi)線(xiàn)的等距線(xiàn)。受機(jī)床結(jié)構(gòu)影響,測(cè)頭的安裝位置距Y軸的中心(重心)位置存在偏置量,如圖2所示。為了使測(cè)頭在測(cè)量時(shí)正對(duì)被測(cè)齒槽,需要以抵償上述偏置。由于Y 軸行程很短,抵償偏置后往往已接近Y軸一端行程的極限位置,大大限制了測(cè)量運(yùn)動(dòng)范圍,難以滿(mǎn)足較大規(guī)格漸開(kāi)線(xiàn)的測(cè)量。此外,Y軸上安裝有砂輪、電主軸及其附屬裝置,質(zhì)量較大,重心的偏移會(huì)導(dǎo)致Y軸自身的直線(xiàn)度誤差及X、Y 軸間的垂直度誤差,引起機(jī)床的幾何及運(yùn)動(dòng)誤差,進(jìn)而導(dǎo)致測(cè)量誤差。因此直角坐標(biāo)法不是最優(yōu)的在機(jī)測(cè)量方案。
3)嚙合線(xiàn)法
探針球心的運(yùn)動(dòng)軌跡為被測(cè)漸開(kāi)線(xiàn)的嚙合線(xiàn)。這種方法雖有效避免了展成法中對(duì)于長(zhǎng)導(dǎo)軌的要求,但是測(cè)量運(yùn)動(dòng)需要機(jī)床X、Y、C三個(gè)伺服軸插補(bǔ)完成。由于機(jī)床是由各運(yùn)動(dòng)軸串聯(lián)而成,每個(gè)軸及軸與軸之間的各種形式的誤差相互疊加最終作用在測(cè)頭的軌跡上,引起測(cè)量誤差。顯然,參與在機(jī)測(cè)量的伺服軸越多,測(cè)量誤差越大。
4)極坐標(biāo)法
由機(jī)床回轉(zhuǎn)軸C軸及X軸做插補(bǔ)運(yùn)動(dòng)完成測(cè)量。其優(yōu)勢(shì)在于測(cè)量過(guò)程中不存在機(jī)床的重心的偏移。同時(shí),避免了對(duì)較長(zhǎng)導(dǎo)軌幾何及運(yùn)動(dòng)精度的要求。綜上,本文選擇極坐標(biāo)法進(jìn)行漸開(kāi)線(xiàn)齒廓偏差的在機(jī)測(cè)量。
測(cè)量模型的建立
測(cè)量過(guò)程中,探針始終與漸開(kāi)線(xiàn)螺旋面相切,兩者的空間相互位置關(guān)系如圖4所示:在過(guò)測(cè)點(diǎn)k的漸開(kāi)線(xiàn)螺旋面的法平面內(nèi),測(cè)球同法平面與螺旋面的交線(xiàn)相切于測(cè)點(diǎn)k;在齒廓偏差的測(cè)量平面(螺旋面任意端截面)內(nèi),測(cè)球與被測(cè)漸開(kāi)線(xiàn)在k點(diǎn)相切。
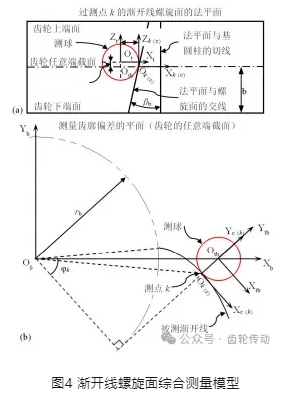
不妨建立如下坐標(biāo)系:ΣOb齒廓偏差測(cè)量坐標(biāo)系,固定在距齒輪下端面距離為b的端截面內(nèi),原點(diǎn)位于被測(cè)漸開(kāi)線(xiàn)的基圓圓心;ΣOk為在端截面內(nèi)通過(guò)測(cè)點(diǎn)k的漸開(kāi)線(xiàn)法平面坐標(biāo)系,其原點(diǎn)位于基圓與法平面的切點(diǎn)處;ΣOc為在探針測(cè)球球面上的觸點(diǎn)坐標(biāo)系,測(cè)量過(guò)程中與ΣOk重合;ΣOt為測(cè)球球心坐標(biāo)系;ΣOtb為齒廓偏差測(cè)量界面內(nèi)測(cè)球的截面坐標(biāo)系,各坐標(biāo)軸方向與ΣOt相同;ΣOm為機(jī)床(齒輪)坐標(biāo)系,設(shè)置在齒輪下端面,圓心位于齒輪的中心,其各坐標(biāo)軸方向與機(jī)床各伺服軸方向相同。
根據(jù)圖4所示的各坐標(biāo)系之間的相互位姿關(guān)系,應(yīng)用齊次坐標(biāo)變換原理,在ΣOm下描述測(cè)量過(guò)程中探針球心Ot的位置,即可得到漸開(kāi)線(xiàn)螺旋面綜合測(cè)量模型:
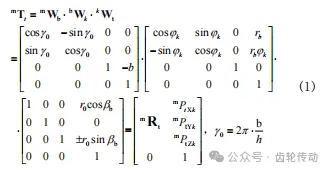
式中,φk為被測(cè)點(diǎn)k對(duì)應(yīng)的展開(kāi)角,rb為被測(cè)齒輪的基圓半徑,r0為探針測(cè)球半徑,βb為被測(cè)齒輪基圓螺旋角。
在機(jī)測(cè)量時(shí),齒輪在C軸帶動(dòng)下做回轉(zhuǎn)運(yùn)動(dòng),為保證測(cè)頭與齒輪的始終接觸,測(cè)頭由X軸帶動(dòng)應(yīng)做相應(yīng)的直線(xiàn)移動(dòng),伺服軸間的關(guān)系為:
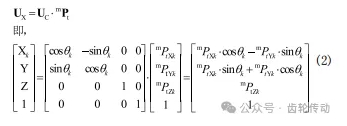
式中,θk、Xk、Y、Z分別為測(cè)點(diǎn)k對(duì)應(yīng)的機(jī)床C軸、X 軸、Y軸、Z軸在機(jī)床坐標(biāo)系下的坐標(biāo)。
由于機(jī)床Y軸始終停在一個(gè)固定位置上,假設(shè)在機(jī)床坐標(biāo)系下其坐標(biāo)值為e,則有:
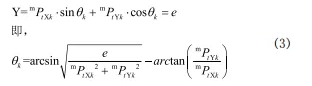
則各測(cè)點(diǎn)對(duì)應(yīng)的機(jī)床X軸及C軸的在機(jī)床坐標(biāo)系下的坐標(biāo):
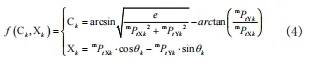
二、誤差補(bǔ)償方法
補(bǔ)償原理
數(shù)控機(jī)床的幾何及運(yùn)動(dòng)誤差會(huì)導(dǎo)致插補(bǔ)運(yùn)動(dòng)產(chǎn)生的實(shí)際理論構(gòu)型曲線(xiàn)與標(biāo)準(zhǔn)理論構(gòu)型曲線(xiàn)存在偏差,引起測(cè)頭探針的誤偏轉(zhuǎn),產(chǎn)生測(cè)量誤差。通過(guò)建立機(jī)床空間綜合誤差與測(cè)量誤差之間的映射關(guān)系,計(jì)算出測(cè)點(diǎn)的誤差,進(jìn)而對(duì)測(cè)量誤差進(jìn)行補(bǔ)償,從而提高在機(jī)測(cè)量精度。齒廓偏差在機(jī)測(cè)量誤差補(bǔ)償方法的基本流程如圖5所示。
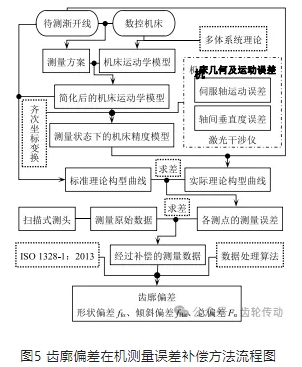
首先,根據(jù)測(cè)量方案對(duì)機(jī)床的運(yùn)動(dòng)構(gòu)型進(jìn)行簡(jiǎn)化,應(yīng)用多體系統(tǒng)理論建立對(duì)應(yīng)于測(cè)量方案的機(jī)床運(yùn)動(dòng)學(xué)模型,并求出測(cè)量時(shí)的標(biāo)準(zhǔn)理論構(gòu)型曲線(xiàn)坐標(biāo)集;隨后,結(jié)合機(jī)床幾何及運(yùn)動(dòng)誤差,基于齊次坐標(biāo)變換方法建立測(cè)量狀態(tài)下的機(jī)床精度模型,并求出空間誤差作用下的實(shí)際理論構(gòu)型曲線(xiàn)坐標(biāo)集;顯然,兩種構(gòu)型曲線(xiàn)上各坐標(biāo)點(diǎn)的差即為各測(cè)點(diǎn)的測(cè)量誤差;隨后,將掃描式測(cè)頭得到的測(cè)量原始數(shù)據(jù)與測(cè)量誤差求差,即可得到經(jīng)過(guò)修正的測(cè)量數(shù)據(jù);最后,依據(jù)ISO 1328-1:2013標(biāo)準(zhǔn)的規(guī)定,對(duì)測(cè)量數(shù)據(jù)進(jìn)行處理,便可得到齒廓偏差的測(cè)量結(jié)果。
需要指出的是,數(shù)控機(jī)床空間綜合誤差的補(bǔ)償方法通常有兩種。一是前補(bǔ)償,即利用坐標(biāo)點(diǎn)誤差修正原有NC程序刀具(測(cè)頭)點(diǎn)位,再進(jìn)行加工或測(cè)量;二是后補(bǔ)償,即測(cè)量完成后,直接利用坐標(biāo)點(diǎn)誤差修正測(cè)量原始數(shù)據(jù)。前補(bǔ)償大多應(yīng)用于數(shù)控加工過(guò)程,其問(wèn)題在于:修正后的 NC程序依然由包含誤差的伺服機(jī)構(gòu)執(zhí)行,補(bǔ)償精度是有限的。而后補(bǔ)償方法有效避免了前補(bǔ)償法中的二次補(bǔ)償誤差,更適用于在機(jī)測(cè)量誤差的補(bǔ)償與修正。
磨齒機(jī)精度建模
數(shù)控機(jī)床的空間綜合誤差由伺服軸的運(yùn)動(dòng)誤差及伺服軸間的垂直度誤差兩部分構(gòu)成,如圖6所示。在三維笛卡爾坐標(biāo)系內(nèi),伺服軸的運(yùn)動(dòng)誤差有六個(gè)自由度,包括沿三個(gè)坐標(biāo)軸的平移及繞三個(gè)坐標(biāo)軸的回轉(zhuǎn)。伺服軸間的垂直度誤差為繞三個(gè)坐標(biāo)軸旋轉(zhuǎn)的角度誤差。兩者的特征矩陣如表1所示,矩陣中的各項(xiàng)元素的值均可通過(guò)激光干涉儀測(cè)得。
不妨將伺服軸的運(yùn)動(dòng)誤差及軸間垂直度誤差看作為機(jī)床各伺服軸的微小的錯(cuò)誤運(yùn)動(dòng)。因此,采用齊次坐標(biāo)變換的方法,按照機(jī)床的拓?fù)浣Y(jié)構(gòu),將各誤差特征矩陣連乘起來(lái)便可得到機(jī)床(某側(cè)運(yùn)動(dòng)鏈)的空間精度模型:

式中,Δi+1Wi為伺服軸間垂直度誤差,Ui為伺服軸運(yùn)動(dòng)功能矩陣,ΔUi 為伺服軸的運(yùn)動(dòng)誤差。
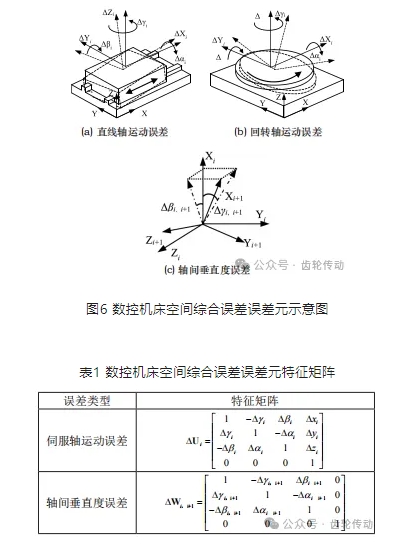
測(cè)量誤差的計(jì)算
采用極坐標(biāo)法,即C軸、X軸插補(bǔ)法測(cè)量漸開(kāi)線(xiàn)齒廓時(shí),YK73系列成形砂輪磨齒機(jī)的運(yùn)動(dòng)構(gòu)型可簡(jiǎn)化為如圖7所示的形式。
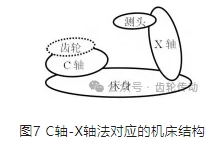
根據(jù)式(5)及式(2),測(cè)量狀態(tài)下機(jī)床的精度模型為:
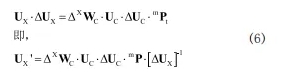
結(jié)合式(4)及式(6),可得到在機(jī)床幾何及運(yùn)動(dòng)誤差作用下,各測(cè)點(diǎn)對(duì)應(yīng)的機(jī)床X軸及C軸的在機(jī)床坐標(biāo)系下的坐標(biāo)f'(Ck',Xk')。
那么,各測(cè)點(diǎn)的測(cè)量誤差為:

三、實(shí)驗(yàn)
在一臺(tái)五軸數(shù)控成形砂輪磨齒機(jī)上進(jìn)行了大規(guī)格漸開(kāi)線(xiàn)齒廓的在機(jī)測(cè)量及誤差補(bǔ)償實(shí)驗(yàn),如圖8所示。被測(cè)齒輪主要參數(shù)如表2所示。
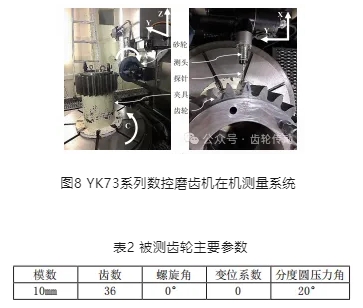
將齒輪參數(shù)代入式(1)及式(4)計(jì)算得到機(jī)床坐標(biāo)系下各測(cè)點(diǎn)對(duì)應(yīng)C軸及X軸的絕對(duì)坐標(biāo),據(jù)此編寫(xiě)測(cè)量數(shù)控程序,完成測(cè)量。應(yīng)用激光干涉儀分別測(cè)量機(jī)床C軸、X軸整個(gè)行程范圍內(nèi)的各項(xiàng)誤差及兩軸間的垂直度誤差;結(jié)合式 (7)計(jì)算各測(cè)點(diǎn)的測(cè)量誤差,隨后對(duì)測(cè)頭記錄的原始數(shù)據(jù)進(jìn)行修正、補(bǔ)償;最后依據(jù)ISO 1328-1:2013的規(guī)定計(jì)算漸開(kāi)線(xiàn)齒廓偏差的各項(xiàng)評(píng)價(jià)指標(biāo)。
首先,為驗(yàn)證本文的測(cè)量方法及補(bǔ)償方法的有效性。隨機(jī)在齒輪上選擇一牙,以其右齒面為例,將其測(cè)量結(jié)果與齒輪量?jī)x的測(cè)量結(jié)果進(jìn)行對(duì)比,同時(shí)對(duì)比補(bǔ)償前后的結(jié)果。表3為齒廓偏差評(píng)價(jià)參數(shù)的對(duì)比結(jié)果。圖9為補(bǔ)償前后齒廓偏差測(cè)量曲線(xiàn)及與齒輪量?jī)x計(jì)量結(jié)果的對(duì)比。
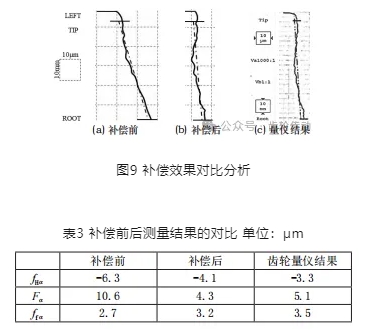
可以看出,本文提出的測(cè)量方法是可行的、有效的。通過(guò)補(bǔ)償,測(cè)量精度得到了明顯提高,補(bǔ)償后齒廓偏差的三項(xiàng)評(píng)價(jià)指標(biāo)均接近齒輪量?jī)x的測(cè)量結(jié)果。
在齒輪上選擇均勻分布的三個(gè)輪齒進(jìn)行測(cè)量及補(bǔ)償實(shí)驗(yàn),驗(yàn)證本文方法的可靠性及適應(yīng)性。實(shí)驗(yàn)獨(dú)立重復(fù)進(jìn)行5 次。限于篇幅這里只將1號(hào)齒的測(cè)量結(jié)果展示在表4之中。
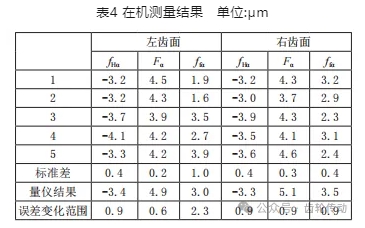
由表可知,各評(píng)價(jià)指標(biāo)的標(biāo)準(zhǔn)差最小為0.2μm,最大為1μm,這說(shuō)明測(cè)量結(jié)果的重復(fù)性較好,測(cè)量方法的可靠性較高。與量?jī)x相比,除左齒面形狀偏差ffα外,5次測(cè)量得到的各評(píng)價(jià)參數(shù)誤差波動(dòng)范圍均小于1μm,最小僅為 0.6μm,這驗(yàn)證了測(cè)量方法的精確性。
在5次測(cè)量結(jié)果中隨機(jī)選取某次的測(cè)量報(bào)表如圖10所示。可以看出,采用本文方法得到的齒廓偏差測(cè)量結(jié)果,在偏差大小、偏差位置、偏差形狀方面都與齒輪量?jī)x的計(jì)量結(jié)果保持了較高的一致性。
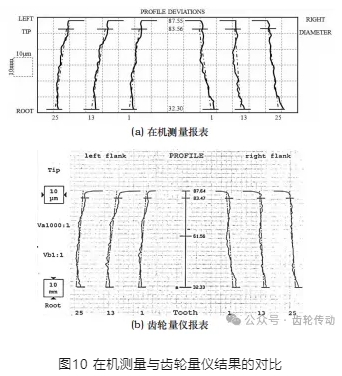
四、結(jié)語(yǔ)
提出了確定合理的數(shù)控機(jī)床在機(jī)測(cè)量方案應(yīng)遵循的準(zhǔn)則;
針對(duì)大規(guī)格磨齒機(jī)結(jié)構(gòu)特點(diǎn),對(duì)比分析了各種漸開(kāi)線(xiàn)齒廓測(cè)量方法的優(yōu)劣,確定了極坐標(biāo)法為最優(yōu)的在機(jī)測(cè)量方案;
以探針與齒面嚙合關(guān)系為約束,推導(dǎo)了漸開(kāi)線(xiàn)螺旋面綜合測(cè)量模型,建立了漸開(kāi)線(xiàn)被測(cè)構(gòu)型與機(jī)床伺服軸運(yùn)動(dòng)量之間的映射關(guān)系;
基于多提系統(tǒng)理論及齊次坐標(biāo)變換方法,建立了對(duì)應(yīng)于測(cè)量方案的機(jī)床綜合精度模型,推導(dǎo)了機(jī)床空間綜合誤差與測(cè)量誤差之間的函數(shù)關(guān)系;計(jì)算了各測(cè)點(diǎn)處的測(cè)量誤差,實(shí)現(xiàn)了在機(jī)測(cè)量誤差的后補(bǔ)償;
在一臺(tái)五軸數(shù)控成形砂輪磨齒機(jī)上進(jìn)行了大規(guī)格漸開(kāi)線(xiàn)齒廓的在機(jī)測(cè)量及誤差補(bǔ)償實(shí)驗(yàn),實(shí)驗(yàn)結(jié)果證明了本文提出的方法有效、可靠、精度高。
參考文獻(xiàn)略.