新能源純電動(dòng)卡車用電機(jī)取代發(fā)動(dòng)機(jī)作為驅(qū)動(dòng)源,所匹配的變速器傳動(dòng)系統(tǒng)具有速比大、功率密度高的特點(diǎn),為進(jìn)一步降低變速器重量,殼體采用鋁合金材料。其一款四檔變速器在進(jìn)行疲勞壽命試驗(yàn)時(shí)一檔齒輪出現(xiàn)了接觸疲勞失效。未能滿足使用要求,因此必須改善齒輪嚙合性能,提高齒輪壽命。齒輪修形技術(shù)是減少制造誤差、抵消彈性變形對(duì)齒輪嚙合的影響,提高齒輪性能及壽命的有效手段。
國(guó)外學(xué)者 Walker在 1938 年公布了漸開(kāi)線齒輪齒廓修形。Mehmet建立了研究扭轉(zhuǎn)振動(dòng)的模型,通過(guò)優(yōu)化齒輪初始的設(shè)計(jì)參數(shù)來(lái)抑制其振動(dòng),提高了齒輪嚙合性能。國(guó)內(nèi)研究者謝坤琪等在 2019 年通過(guò) Romax 軟件建立了減速器傳動(dòng)模型,并對(duì)齒輪進(jìn)行修形,對(duì)比修形前后齒輪承載面上的最大載荷、應(yīng)力的數(shù)值變化,證明了不改變齒輪參數(shù)情況下對(duì)齒輪修形可以提高齒輪的承載能力。吳晗等利用 Romax 對(duì)齒輪進(jìn)行修形分析,結(jié)果表明修形后減小了齒輪的傳遞誤差和最大接觸應(yīng)力,齒面載荷分布更加合理,有效改善了齒輪的傳動(dòng)性能,增加了齒輪壽命。本文對(duì)變速器傳動(dòng)系統(tǒng)進(jìn)行建模仿真,分析殼體變形對(duì)齒面嚙合的影響,制定齒輪修形優(yōu)化方案并進(jìn)行試驗(yàn)驗(yàn)證。
一、變速器結(jié)構(gòu)與傳動(dòng)系統(tǒng)建模
變速器結(jié)構(gòu)
變速器為 12~18 t 的新能源重卡定軸式四檔自動(dòng)變速器,具有傳動(dòng)效率高,傳遞扭矩大、易于制造且價(jià)格低廉、結(jié)構(gòu)簡(jiǎn)單等優(yōu)點(diǎn)。
變速器共有 4 個(gè)檔位,其中四檔為直接檔,倒檔為一檔時(shí)驅(qū)動(dòng)電機(jī)反轉(zhuǎn)來(lái)實(shí)現(xiàn)。齒輪為漸開(kāi)線斜齒輪,最大輸入扭矩為 1 000 N·m,最大輸入轉(zhuǎn)速為 3 100 rpm,各檔速比見(jiàn)表 1。
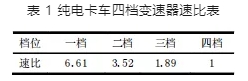
該結(jié)構(gòu)中常嚙合齒輪副的輸入軸齒輪與輸入軸固連,各齒輪副中的中間軸齒輪與中間軸固連,輸出軸上的齒輪與輸出軸間由滾針軸承支撐,與輸出軸通過(guò)同步器在相應(yīng)檔位時(shí)進(jìn)行連接,傳遞動(dòng)力。
齒輪傳動(dòng)系統(tǒng)建模
利用齒輪傳動(dòng)分析軟件 Romax 對(duì)變速箱傳動(dòng)系統(tǒng)進(jìn)行建模,用于齒輪強(qiáng)度分析及齒輪修形參數(shù)確定。各檔位齒輪參數(shù)見(jiàn)表 2,齒輪材料使用 20CrMnTiH,齒輪精度等級(jí) 7 級(jí)。
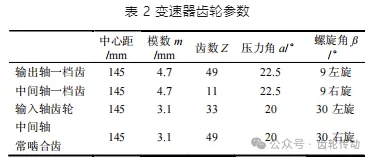
對(duì)齒輪組及齒輪軸進(jìn)行詳細(xì)建模并按照其幾何尺寸進(jìn)行組裝,完成后的 Romax 模型如圖 1 所示。
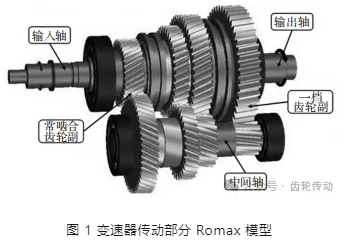
二、齒輪修形方案制定與驗(yàn)證
齒輪修形前分析
失效時(shí)變速器在進(jìn)行疲勞耐久試驗(yàn),輸入轉(zhuǎn)速 1 600 rpm,輸入扭矩 1 000 N·m,失效齒輪為中間軸一檔齒輪,一檔時(shí)動(dòng)力傳遞路線如圖 2 所示。
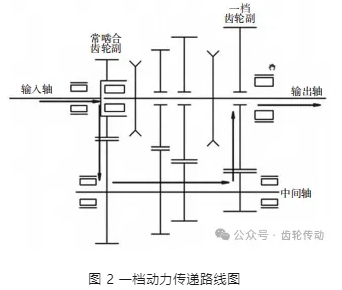
失效形式為齒面早期點(diǎn)蝕引起齒面剝落。觀察失效齒輪,有明顯的偏載現(xiàn)象,如圖 3 所示。
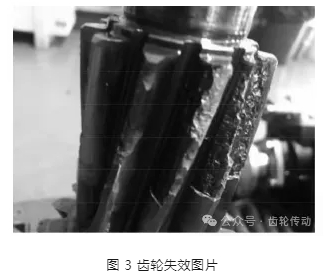
設(shè)計(jì)階段對(duì)各檔位齒輪均進(jìn)行過(guò)設(shè)計(jì)校核,一檔齒輪副接觸安全系數(shù)大于 1.1,滿足使用要求,不應(yīng)出現(xiàn)早期點(diǎn)蝕的情況。同時(shí)對(duì)齒輪的表面硬度及硬化層深進(jìn)行檢測(cè),均在設(shè)計(jì)要求范圍內(nèi),可排除加工制造問(wèn)題。根據(jù)失效現(xiàn)象及排查結(jié)果,可判斷異常失效與齒面偏載有十分密切的關(guān)系,確定偏載情況是解決問(wèn)題的重要方向。
對(duì)齒輪參數(shù)進(jìn)行分析,變速器一檔齒輪副壓力角采用的大壓力角,且單級(jí)速比為 4.45,從而產(chǎn)生的齒輪徑向力較大,對(duì)殼體軸承座處施加的力也會(huì)更大;同時(shí)殼體采用的鋁合金材料,材料的彈性模量與傳統(tǒng)卡車變速器鑄鐵殼體相比小的多,受力產(chǎn)生的變形較大,使得齒輪安裝軸兩端偏移理論位置,造成齒輪軸線平行度差,引起齒輪偏載,與失效形式吻合。因此需要重新考慮齒輪修形方案,且重點(diǎn)考慮殼體變形造成的嚙合偏差。
修形方案
齒輪在實(shí)際使用中會(huì)因?yàn)榧庸ふ`差、材料變形等因素的影響,嚙合性能下降,存在沖擊、偏載等情況。齒面修形就是主動(dòng)將偏差引入到齒輪中,使齒面輪廓偏離原本的理論齒廓,從而減小因誤差及變形引起的沖擊和偏載。需要注意的是齒面的修形量與齒輪的變形量有著十分密切的關(guān)系,不同工況下最佳的齒面修形量有所不同。
齒面的微觀修形分為齒廓修形及齒向修形。
對(duì)齒形方向進(jìn)行齒廓修形,包括漸開(kāi)線修形、凸度修形及齒頂修緣,目的為減少齒面偏載現(xiàn)象,抵消接觸變形,降低接觸應(yīng)力、嚙合沖擊及傳遞誤差。
對(duì)齒寬方向進(jìn)行齒向修形,主要為鼓形修形,使得齒輪的齒面形成中間凸的形狀,優(yōu)化齒面的接觸斑點(diǎn);螺旋線修形,即在齒寬方向?qū)β菪沁M(jìn)行調(diào)整,減少偏載現(xiàn)象。
根據(jù)失效原因分析,計(jì)算殼體變形引起的偏載。建立殼體有限元模型,在一檔最大輸入扭矩的工況下,對(duì)支撐傳動(dòng)系統(tǒng)的軸承座孔進(jìn)行受力分析,對(duì)殼體進(jìn)行受力加載,分析軸承孔剛度,計(jì)算殼體變形量如圖 4 所示。根據(jù)殼體變形量,對(duì)齒輪軸線平行度進(jìn)行計(jì)算,將水平方向上的變形等效替換到螺旋角方向上,進(jìn)行補(bǔ)償修形,從而減少偏載現(xiàn)象。
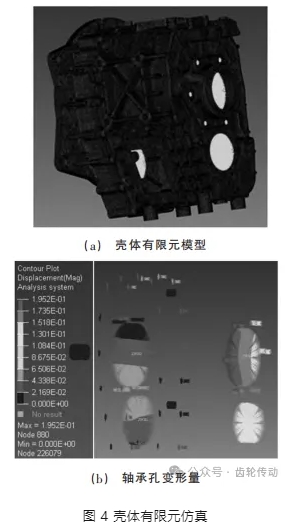
該模型中殼體變形引起的齒輪軸線水平方向平行度偏差如圖 5 所示,計(jì)算公式歸納為

式中:fΣβ 為齒輪軸向總偏差;f ′Hβ1 為輸出軸軸承水平位移 62 μm;f″Hβ1 為輸入軸軸承水平位移 15 μm;f ′Hβ2 為中間軸前軸承水平位移 17 μm;f″Hβ2 為中間軸后軸承水平位移 53 μm。
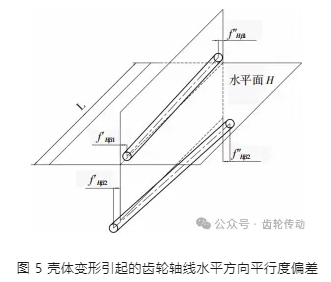
螺旋線補(bǔ)償修形量計(jì)算公式為
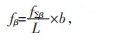
式中:fβ 為螺旋線補(bǔ)償修形量;L 為軸長(zhǎng) 260 mm;b 為齒寬 45 mm。
計(jì)算所得螺旋線補(bǔ)償修形量約為 25 μm。
修形參數(shù)確定
考慮變速器實(shí)際使用工況,一檔用于滿載爬坡時(shí)使用,所需扭矩接近最大扭矩,因此修形按最大輸入扭矩 1 000 N·m 下進(jìn)行。加入螺旋線補(bǔ)償修形,按照最優(yōu)接觸斑點(diǎn)和最小接觸應(yīng)力原則得出一檔齒輪最佳修形量見(jiàn)表 3。
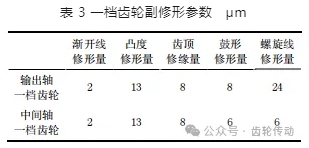
增加螺旋線補(bǔ)償修形前后失效的中間軸一檔齒輪齒面接觸斑點(diǎn)如圖 6 所示,接觸斑點(diǎn)有明顯改善,最大接觸應(yīng)力下降了 22%,極大地改善了齒輪的嚙合性能,能夠有效提高齒輪的壽命。
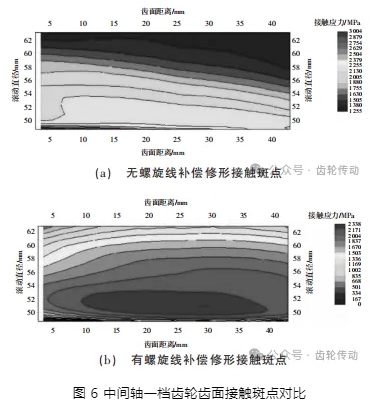
試驗(yàn)驗(yàn)證
對(duì)重新修形后的齒輪再次進(jìn)行試驗(yàn),相同試驗(yàn)工況下原本失效的中間軸一檔齒輪并未出現(xiàn)點(diǎn)蝕,通過(guò)了疲勞耐久試驗(yàn)(圖 7),證明新的修形方案有效地提高了齒輪疲勞壽命(圖 8)。
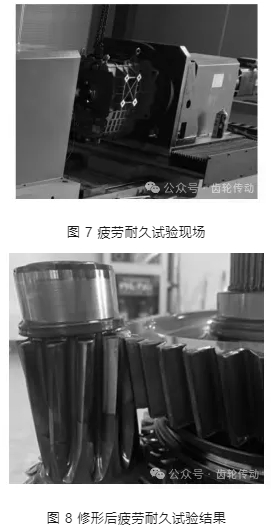
三、結(jié)論
本文針對(duì)應(yīng)用于純電重卡的四檔變速器中間軸一檔失效問(wèn)題,對(duì)齒輪進(jìn)行了修形優(yōu)化并進(jìn)行了試驗(yàn)驗(yàn)證,得出如下結(jié)論。
1)在沒(méi)有改變齒輪宏觀參數(shù)情況下,對(duì)齒面進(jìn)行修形優(yōu)化,提高了齒輪的疲勞壽命,解決了一檔齒輪點(diǎn)蝕問(wèn)題。
2)研究了殼體變形對(duì)齒面嚙合的影響,提出螺旋線補(bǔ)償修形并給出補(bǔ)償計(jì)算方法,優(yōu)化了修形方案。
3)對(duì)需要考慮殼體變形所造成偏載情況的大速比、輕量化殼體變速器齒輪的修形方向具有指導(dǎo)性作用,實(shí)際應(yīng)用效果良好。
參考文獻(xiàn)略.