采用 CBN 砂輪磨齒遇到磨齒燒傷問題:
CBN 砂輪在磨削性能上高于普通鋼玉類砂輪和 SG磨料砂輪,它磨削時幾乎沒有損耗(有極好的保形性)。CBN砂輪有著良好的切削刃角且不易磨損,因此對齒輪的壓應(yīng)力非常小,不易產(chǎn)生磨削裂紋及燒傷。同時,CBN 砂輪采用大進刀量切削,切削效率是SG 砂輪的2~3倍,因此中間軸磨齒采用CBN磨齒工藝。雖然 CBN 磨齒優(yōu)勢明顯,但卻伴生有磨齒燒傷問題,幾乎所有的 CBN 砂輪磨齒都會遇到這類技術(shù)質(zhì)量問題。
從以上對 CBN 砂輪應(yīng)用的分析可看出,高效的磨削帶來高磨削熱以及CBN 砂輪使用的技術(shù)復(fù)雜性,必須采用適當?shù)募夹g(shù)解決好磨削發(fā)熱問題。
從磨削原理來看,磨削熱是造成磨齒燒傷的根源,因此改善磨齒燒傷有兩個途徑:一是盡最大可能減少磨削熱的產(chǎn)生;二是改善冷卻條件,盡量使產(chǎn)生的熱量少傳入工件。
1)合理選擇砂輪的粒度。粒度即磨料顆粒的大小,用每英寸篩網(wǎng)上的篩孔數(shù)量表示。粒度提高時,表面粗糙度會提高,采用60粒的砂輪時,可以滿足大部分零件表面粗糙度的要求。當粒度達到80?;蛘吒邥r,砂輪的容屑能力和散熱性能會大大降低,進而增加磨削燒傷和裂紋發(fā)生的概率。為確保齒面粗糙度和齒面支撐長度率,中間軸磨齒砂輪采用100粒砂輪。
2)硬度表示磨料從砂輪表面脫落的難易程度,這取決于磨料與結(jié)合劑的粘結(jié)強度,與磨料本身的硬度是兩種不同的概念。硬度較高的砂輪,磨料不易脫落;硬度較低的砂輪,磨料相對容易脫落。由于砂輪具有自銳性,磨料在磨削過程中會從砂輪表面脫落,若硬度太高,則砂輪在磨鈍后磨料仍難以及時脫落,容易產(chǎn)生更多的磨削熱。因此,宜選擇較低的砂輪硬度,以便磨鈍后的砂粒能夠及時脫落。中間軸表面最低硬度為 HRC60, 經(jīng)過實踐驗證,中間軸砂輪由J 級硬度改為G 級硬度,磨削燒傷改善非常明顯。
3)砂輪的結(jié)構(gòu)形式對磨齒燒傷影響也是巨大的。SU 成型磨齒機自設(shè)備驗收之日起,燒傷問題便時有發(fā)生。為此,在砂輪圓周方向上開槽,使砂輪間斷磨削,工件受熱時間短,金相組織來不及轉(zhuǎn)變,通過強化散熱條件,進行磨齒燒傷改善。剛開始的時候,為了保證砂輪開槽強度,開槽的寬度為1mm, 隨著砂輪開槽技術(shù)日臻完善,目前砂輪開槽尺寸由1mm 優(yōu)化至 2mm, 在防止燒傷上起到了良好的效果,見圖11。
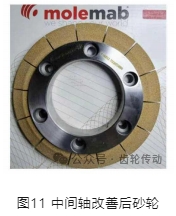
4)組織表示磨料、結(jié)合劑和氣孔三者之間的比例關(guān)系,磨料所占比例越大,組織越緊密,氣孔越少;反之,組織疏松,氣孔較多。組織緊密的砂輪能磨出粗糙度較好的工件表面,而組織疏松的砂輪,因空隙大,可以保證磨削過程中容納磨屑,避免砂輪堵塞,減少磨削熱。
合理的切削參數(shù)對磨齒燒傷的影響
背吃刀量的選用是關(guān)系到磨削燒傷和裂紋的關(guān)鍵因素。背吃刀量增大,零件磨削力增大,會產(chǎn)生更多的磨削熱,容易引起磨削燒傷。對于體積大、熱處理后變形較大的零件,在利用數(shù)控機床進行磨削時,對刀后還要人為放大空程量。對于數(shù)控磨齒機,在磨齒過程中,還需要觀察功率顯示屏,防止熱處理齒面變形導(dǎo)致局部背吃刀量過大。對于磨齒機,切削速度取決于砂輪的轉(zhuǎn)速。對于同一片砂輪,砂輪轉(zhuǎn)速增加,線速度相應(yīng)增加,磨削燒傷和磨削裂紋的風險也會增加。在機床能力允許的前提下,選取砂輪線速度在30~ 35m/s 的范圍內(nèi),即可滿足Ra0.8 的表面粗糙度要求。在磨削時,砂輪沿齒面的移動速度應(yīng)根據(jù)模數(shù)確定。通過減少磨齒余量可以有效降低磨齒燒傷風險。中間軸齒圈磨齒余量由 0.2mm 降至0 . 14mm, 粗磨徑向余量由 0 . 1 2mm 降至 0.08mm, 精磨徑向余量由0.08mm降至0.06mm, 對磨齒燒傷解決起到了至關(guān)重要的作用。砂輪軸向移動速度一般選取 2500mm/min。經(jīng)過生產(chǎn)實踐驗證,粗磨正向軸向移動速度為2800mm/min, 粗磨反向軸向移動速度為2800mm/min, 精磨正向軸向移動速度為2800mm/min, 精磨反向軸向移動速度為2700mm/min。檢齒誤差的選擇也至關(guān)重要,因為檢齒誤差過大,容易造成偏磨,局部熱量積聚,導(dǎo)致磨齒燒傷。經(jīng)過反復(fù)試驗驗證,確定檢齒示值誤差≤0.08mm。
磨齒油對磨齒燒傷的影響
冷卻液在磨削的過程中具有冷卻、清洗、潤滑和防銹的作用。磨齒通常采用磨齒油,對磨齒油的要求如下:①具備良好的潤滑和冷卻性能,減少切削熱的產(chǎn)生,從而使產(chǎn)品具有良好的工件表面質(zhì)量,滿足精度、粗糙度要求,獲得高進給量,實現(xiàn)更高的加工效率,降低磨削力,節(jié)約能耗,提高砂輪壽命;②高閃點,低揮發(fā),降低火災(zāi)風險;③優(yōu)異的抗油霧性能;④良好的空氣釋放性,減少泡沫,適合高速加工和高壓系統(tǒng);⑤良好的過濾性和沉屑性;⑥安全環(huán)保,不刺激皮膚。磨齒油一方面會帶走磨削熱量,另一方面可以起到潤滑的作用,減少摩擦。在冷卻的過程中,如果冷卻的速度不夠,就會導(dǎo)致熱量無法快速釋放,進而造成表面溫度過高,產(chǎn)生燒傷問題,冷卻過快則會導(dǎo)致表面硬化問題。因此要解決如下問題:
1)磨削區(qū)的磨齒油供應(yīng)量不足或供液壓力不足。
2)磨齒油的噴射口噴射位置安裝不當,應(yīng)調(diào)整使其直接噴射到磨削區(qū)域。
3)磨齒油溫度太高,導(dǎo)致冷卻性能急劇降低,應(yīng)配備合適的冷卻換熱系統(tǒng)。
4)磨齒油中產(chǎn)生大量泡沫,降低冷卻效果及冷卻均勻性,應(yīng)及時排除解決。
5)磨齒油太臟,未配備有效的過濾系統(tǒng)。
6)磨齒油的選擇不當,油品的黏度、流動性及冷卻性能不合適。
如果磨齒油的上述問題不能很好解決,則磨齒燒傷的概率會大幅提高。
冷卻系統(tǒng)對磨齒燒傷的影響
在磨齒過程中,砂輪與工件接觸區(qū)的瞬時溫度可達 960℃以上,因此,冷卻油管的位置決定了發(fā)生磨齒燒傷的概率。通常情況下,冷卻液直接噴射到磨削區(qū)域,但磨削區(qū)域產(chǎn)生的瞬時熱量會使冷卻液霧化,在磨削區(qū)域形成貧油區(qū),使冷卻液無法達到冷卻效果,加大了磨齒燒傷的概率。改進后的冷卻液避免直接噴射在磨削區(qū)域,同時要考慮砂輪氣孔的阻塞,兩組冷卻油管的分工如下:一組直接噴射到砂輪上參與切削,以沖去粘在砂輪上的鐵屑,這一組的噴射方向與砂輪旋轉(zhuǎn)方向相反;另一組噴射在磨削區(qū)域,與砂輪的旋轉(zhuǎn)方向相同,保證了冷卻液在離心力作用下到達磨削區(qū)域,達到冷卻效果,見圖12。也有其他方式,見圖13,需要通過試驗驗證效果。試驗證明,改進后的冷卻系統(tǒng)對磨齒燒傷有明顯改善。
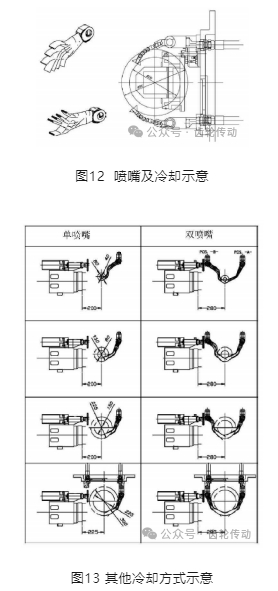
在磨齒操作過程中,冷卻控制是十分關(guān)鍵的要素。冷卻一定要完全且充分,冷卻液也一定要流到區(qū)域內(nèi)。多數(shù)情況下,流量需要控制在40~60L/min, 這樣才可以實現(xiàn)完全的冷卻,壓力一般控制在0.8~1.2N/mm², 對表面切屑進行較好的沖刷。在冷卻液足夠純凈的條件下進行工作,從而清除冷卻液中的較臟的顆粒。冷卻液的承載容器體積一定要夠大,防止其中產(chǎn)生過多的氣泡。防止冷卻液溫度過快改變,一般控制冷卻系統(tǒng)的容積和工作間的室溫,對于溫度就可以進行較好的控制,但是在一些特殊情況下,還是要使用散熱器進行工作。
工裝夾具對磨齒燒傷的影響
工裝夾具及輔助工裝的剛度也是決定磨齒燒傷的關(guān)鍵因素(圖14)。在磨削過程中,砂輪的瞬間進給使工件承擔很大的軸向力,砂輪的進給使工件處于不穩(wěn)定狀態(tài),導(dǎo)致設(shè)定的進給量的均勻性無法保證,從而大幅增加磨齒燒傷的概率。
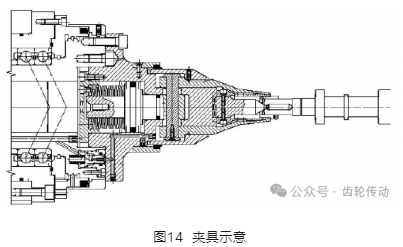
輔助工藝對磨齒燒傷的影響
磨齒前要對滲碳淬火齒輪進行打磨或噴沙,以有效去除齒面的氧化皮,降低雜質(zhì)堵塞砂輪的概率,有效降低磨齒燒傷的概率,另外也可以提高冷卻液的潔凈度。
金剛滾輪等對磨齒燒傷的影響
在砂輪的平衡上要做到精益求精(砂輪動平衡等級 G0.4), 仔細操作和調(diào)控,因為砂輪在高速旋轉(zhuǎn)時,每一次微小的抖動都會對齒面造成嚴重的燒傷。展成磨齒機和成型磨齒機都要保持金剛筆和金剛滾輪的鋒利(圖15),以修整出銳利的砂輪。若金剛筆有0.3mm以上的磨損,或金剛輪有0.02mm以上的磨損,則表明金剛石(筆)已經(jīng)鈍化,需要及時更換。金剛筆和金剛輪在粗加工時一定要移動迅速,以保證砂輪的銳利性。根據(jù)經(jīng)驗,砂輪修形頻率為1次/8 件,修整量0.01mm, 修形移動速度300mm/min。
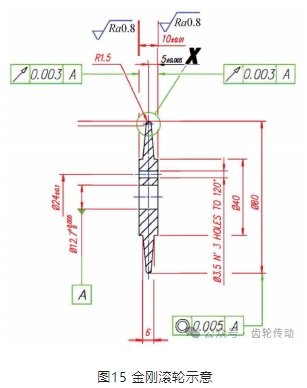
滾齒對磨齒燒傷的影響
滾齒是磨齒粗加工,滾齒精度也會影響磨齒燒傷。以 1701048-TV101 中間軸為例,在滾齒加工中,需要嚴格控制滾齒公法線 W5=60.22mm±0.015mm (磨齒公法線 W5=60.075mm±0.015mm, 公差帶寬由0.05mm壓縮至0.03mm, 確保磨齒余量為0.145mm±0.03mm), 滾齒齒圈跳動量≤0.041mm, 滾齒齒距累積 Fp≤0.051mm,齒形 Fa≤0.021mm, 齒向Fβ≤0.018mm 。主要目的是確保磨齒余量均勻,減少局部余量過大熱量積聚變化產(chǎn)生磨齒燒傷。滾齒過程中,滾刀的設(shè)計也是重要一環(huán)。磨前滾刀對齒形設(shè)計有如下要求:①齒面留磨余量均勻;②齒根處要有一定沉割,一般較磨齒余量大0.05~0.07mm, 保證磨齒后無臺階,砂輪與齒根具有一定的冷卻空間;③漸開線足夠長,一般來說需要超越 Mn×0.05=4.35×0.05=0.22mm, 即 SPC值由10.7mm 下延至10.92mm。磨前滾刀設(shè)計見圖16。
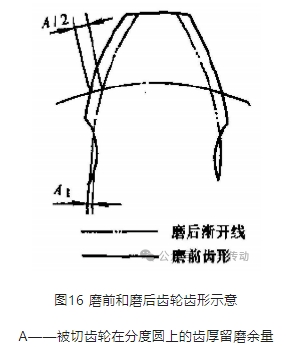
對于磨齒后具有特殊修形的齒圈,例如中間軸B 齒圈,成品修形見圖17。
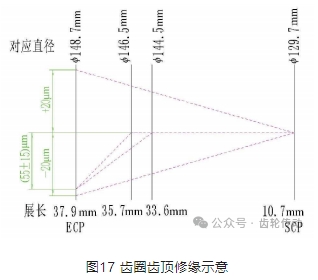
從圖17中可以看到,齒形齒頂修緣最大0.07mm, 相當于在磨削齒頂時會多出0.07mm余量,這對磨齒是相當不利的,將導(dǎo)致齒頂余量加大,磨削熱量增大,增大齒頂磨齒燒傷風險。為此,在滾刀設(shè)計時,讓滾刀自帶齒頂修緣,與成品修緣吻合,從而使齒頂和齒面磨削余量均衡、均勻,從設(shè)計源頭根除磨削燒傷隱患。
熱處理對磨齒燒傷的影響
熱處理變形對熱后加工影響巨大。如果軸的初始變形量大,則很難保證齒圈精度,例如公法線、齒形、齒向、齒圈徑向跳動量,這樣在磨齒加工中就會出現(xiàn)偏磨,導(dǎo)致局部磨削熱積聚,很容易造成磨削燒傷。在材料淬透性未改善前,熱處理不同條件下初始變形量統(tǒng)計見圖18,其中,B 齒圈初始變形量高達0.269mm, 對校直工序來說難度頗大,大部分零件只能通過手工校直來滿足,校直后齒圈跳動量只能保證在0.1mm 以內(nèi)。但是也有因初始變形量大,采用熱校的,不僅浪費成本,還給磨齒留下了很大隱患。由于齒圈跳動量超差,檢齒誤差過小無法通過,只能放大檢齒誤差,結(jié)果就是出現(xiàn)偏磨,很容易產(chǎn)生磨齒燒傷。2021年1月以來,熱處理工藝進行了材料淬透性改善,材料淬透性由H3 優(yōu)化至 H2。第六輪(最后一輪)滲碳淬火工藝,預(yù)氧化溫度由 450~500℃變更為500~550℃。變更工藝后,初始變形量由變更前的0.1~0.12mm, 變?yōu)?.07~0.1mm, 一次校直合格率目前穩(wěn)定在大于或等于98%的水平。改善后,校直齒圈跳動量 Fr≤0.05mm, 確保了檢齒誤差由0. 12mm 優(yōu)化至 0.08mm。整個磨削比較均勻,有效避免了偏磨的出現(xiàn),對避免磨齒燒傷起到了重要作用,見圖19。
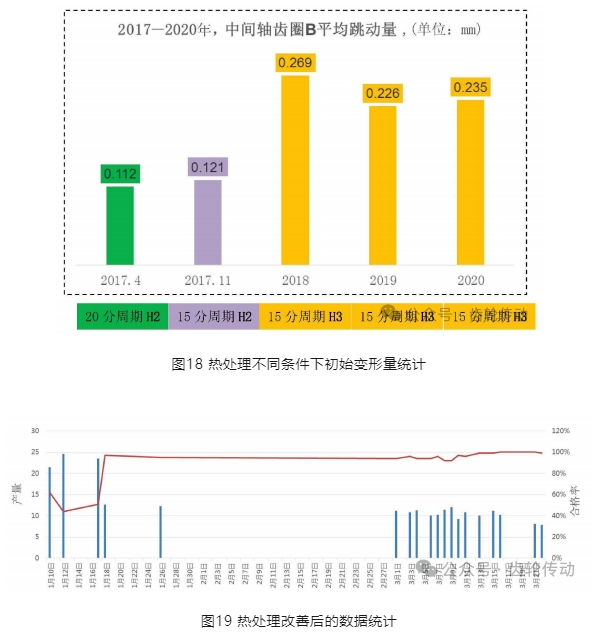
此外,滲層碳濃度過高,在滲層組織中容易形成網(wǎng)狀碳化物或過多的游離碳化物。由于這種物質(zhì)極硬,在磨削過程中可能出現(xiàn)局部過熱傾向和表面回火。另外,還會使輪齒表面產(chǎn)生過多的殘余奧氏體。磨削時,殘余奧氏體因砂輪磨削時產(chǎn)生的熱量和壓力而轉(zhuǎn)變,同時可能伴生表面回火和磨削裂紋。
改善主要對策
改善主要對策見表。
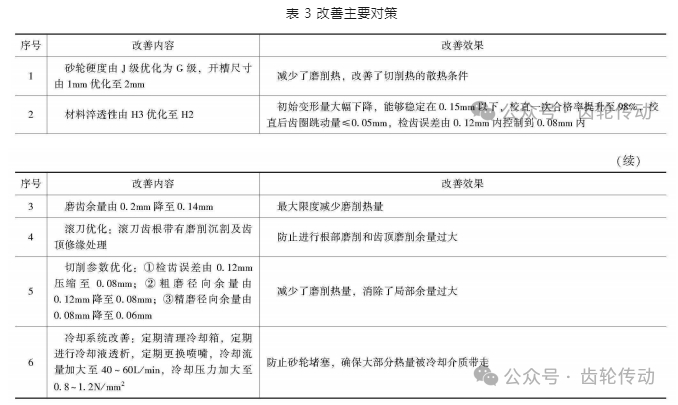
三、改善驗證及檢測
磨齒燒傷成因復(fù)雜,每一項措施都進行了燒傷檢測特管及驗證。通過酸洗法進行磨齒燒傷檢測,加上磨齒燒傷的標準樣件圖譜,經(jīng)過系統(tǒng)培訓,以連續(xù)3個月按每個修整周期 (每8件1次修整)進行1件磨齒燒傷檢測,均未出現(xiàn)磨齒燒傷作為磨齒燒傷效果的評判標準。此外,針對未磨齒燒傷的中間軸通過變速器臺架疲勞壽命驗證,滿足使用壽命作為衡量改善的標準。為此,組織50輛分中間軸100%進行燒傷檢測的零件(無燒傷),定點投放在中間軸打齒排名第一的區(qū)域進一步驗證,得到了客戶的認可。經(jīng)過多輪生產(chǎn)、臺架和路試,必須滿足評判標準,否則視為改善無效或不徹底。
四、改進成果
14檔中間軸打齒為長里程故障,2019年4月才開始在市場上出現(xiàn)。2019年5月首先在23廠增加了磨削燒傷酸洗法抽檢,然后進行了冷卻噴嘴優(yōu)化和更換,檢齒誤差由 0.12mm 加嚴至0.08mm, 齒圈跳動量Fr≥0.08mm 的增加一次粗磨循環(huán),2019年燒傷情況基本可控。但由于檢測環(huán)節(jié)缺失,改進效果只能以市場數(shù)據(jù)檢查,加上量的急劇增加,2020年3mis 和6mis抬頭,3mis 接近0 .05%,6mis 接近 0.2%,12mis 接近0.8%。2020年年底,分別實施了材料淬透性優(yōu)化、校直工藝優(yōu)化、磨齒余量減少、磨齒參數(shù)優(yōu)化、砂輪優(yōu)化、冷卻液優(yōu)化等工作,3mis降至 0 , 6mis 降至 0.02%。由圖20可見,故障率在2021年降低了80%,市場賠償也從單月70萬的峰值逐步降低,證明了改善措施有效。后續(xù)通過在防止流出上增加磁彈儀,在冷卻上實施3D 打印可移動噴嘴,持續(xù)細化影響磨齒燒傷的可能因素,一定會從制造源頭上徹底避免中間軸磨齒燒傷問題。
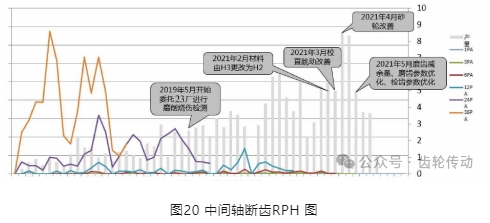
五、結(jié)論
通過對長期生產(chǎn)實踐中出現(xiàn)的各種磨削燒傷的情況進行總結(jié),歸納出磨削燒傷的種類以及可能產(chǎn)生的危害,并分析了磨削燒傷的檢測方法。同時,從合理選用砂輪、合理設(shè)置切削用量、確保冷卻條件等方面,對磨削燒傷的防止措施進行了較為全面的分析。本文的總結(jié)與分析為進一步減少磨削燒傷問題,改善磨削質(zhì)量提供了較為全面的參考。齒輪的磨齒燒傷是客觀存在的,通過對磨齒燒傷因素的探討,找到部分影響磨齒燒傷的因素,在生產(chǎn)過程中不斷改進和完善,可有效改善磨齒燒傷狀況。本文所做試驗還比較有限,尚不能完全總結(jié)出所有磨齒砂輪的性能及與之匹配的磨齒參數(shù),還需開展更多試驗工作。
參考文獻略.