風(fēng)力發(fā)電機(jī)組運(yùn)維成本大、對(duì)可靠性要求極高,隨著風(fēng)電機(jī)組單機(jī)容量朝著8~16 Mw發(fā)展,對(duì)增速齒輪箱扭矩密度提出了更高要求,由此帶來(lái)的齒輪內(nèi)部接觸疲勞失效問題成為制約傳動(dòng)系統(tǒng)可靠性的瓶頸。不同于傳統(tǒng)的齒輪接觸疲勞失效形式(如微點(diǎn)蝕、點(diǎn)蝕和剝落),齒輪內(nèi)部疲勞斷裂(tooth interior fatigue fracture,TIFF)常見于重載滲碳齒輪,其裂紋源大多位于硬化層與心部交界處,斷裂截面與齒面呈40°~ 50°夾角,主要失效原因包括齒輪次表面等效應(yīng)力超出材料許用剪切強(qiáng)度、非金屬夾雜物導(dǎo)致應(yīng)力集中等。
國(guó)外FZG、SMT、KISSsoft等研究機(jī)構(gòu)較早開展了TIFF數(shù)值模擬和試驗(yàn)研究;MackAldener等采用有限元方法,研究了齒輪宏觀參數(shù)、材料強(qiáng)度、滲碳層深度對(duì)TIFF的影響。Al等將TIFF失效計(jì)算方法歸納為應(yīng)力歷程分析、殘余應(yīng)力分析、多軸疲勞準(zhǔn)則選取和失效風(fēng)險(xiǎn)評(píng)估四個(gè)步驟;Hein等基于材料暴露值研究了不同參數(shù)對(duì)齒輪內(nèi)部斷裂失效風(fēng)險(xiǎn)的影響;Octrue等綜合CAE分析方法和多軸疲勞準(zhǔn)則,建立了TIFF失效評(píng)估模型,并就滲碳層深度和殘余壓應(yīng)力的影響進(jìn)行了分析。國(guó)內(nèi)相關(guān)研究起步較晚,Liu等建立齒輪內(nèi)部等效應(yīng)力模型,通過(guò)材料暴露值研究了硬化層深度、殘余應(yīng)力對(duì)齒輪內(nèi)部疲勞斷裂的影響;zhou等采用彈塑性流體動(dòng)力潤(rùn)滑模型研究硬化齒輪的接觸性能,結(jié)合DangVan準(zhǔn)則研究了表面粗糙度、殘余應(yīng)力、硬化層深度對(duì)齒輪內(nèi)部疲勞參數(shù)的影響。上述研究主要側(cè)重于硬化層對(duì)接觸性能的影響,而對(duì)齒輪疲勞可靠度關(guān)注較少。
風(fēng)電齒輪設(shè)計(jì)壽命為20~25年,屬典型的高周疲勞范疇。目前風(fēng)電齒輪的可靠度研究主要針對(duì)點(diǎn)蝕和斷齒失效,而針對(duì)TIFF失效的可靠度研究鮮有報(bào)道。美國(guó)可再生能源實(shí)驗(yàn)室早在2007年便率先啟動(dòng)了風(fēng)電齒輪箱可靠度相關(guān)研究,且一直持續(xù)至今;Sun 等基于應(yīng)力強(qiáng)度干涉模型和Monte Carlo方法建立 了1.5 MW風(fēng)電齒輪箱可靠性分析模型。秦大同等利用二階矩和攝動(dòng)法求解風(fēng)電齒輪動(dòng)態(tài)可靠性指標(biāo);陳會(huì)濤等應(yīng)用概率累積損傷理論構(gòu)建了風(fēng)電齒輪可靠度模型;劉波等通過(guò)建立某1.5 MW風(fēng)電齒輪箱傳動(dòng)系統(tǒng)copula可靠性模型,研究了齒輪可靠度隨服役時(shí)問變化的規(guī)律。目前關(guān)于風(fēng)電齒輪可靠性的研究主要針對(duì)點(diǎn)蝕及彎曲疲勞失效,對(duì)TIFF失效可靠度缺乏深入研究。此外,大部分研究仍局限于傳統(tǒng)均質(zhì)材料的理想假設(shè),未考慮風(fēng)電齒輪時(shí)變載荷、硬化層梯度性能以及微觀修形等因素影響,與大模數(shù)風(fēng)電齒輪實(shí)際運(yùn)行場(chǎng)景存在顯著差異,嚴(yán)重制約了更高扭矩密度風(fēng)電齒輪箱的研發(fā)。
本文結(jié)合某風(fēng)場(chǎng)2 MW風(fēng)電齒輪TIFF失效案例,分析影響大模數(shù)滲碳齒輪TIFF失效的主要因素,基于應(yīng)力強(qiáng)度模糊干涉函數(shù)和齒輪材料強(qiáng)度退化理論,結(jié)合Dang Van多軸疲勞準(zhǔn)則建立風(fēng)電滲碳齒輪內(nèi)部疲勞斷裂可靠度分析模型,并通過(guò)因子試驗(yàn)和望小優(yōu)化設(shè)計(jì)建立TIFF疲勞可靠度優(yōu)化方法,期望為高可靠性高扭矩密度風(fēng)電齒輪箱的設(shè)計(jì)制造提供支撐。
一、齒輪內(nèi)部疲勞斷裂可靠性分析建模
齒輪內(nèi)部等效應(yīng)力
鑒于齒輪接觸過(guò)程中的時(shí)變多軸非比例加載情況,多軸疲勞準(zhǔn)則被廣泛應(yīng)用于接觸疲勞評(píng)估,其中應(yīng)用較廣泛主要是基于臨界面法的Dang Van準(zhǔn)則、Finley準(zhǔn)則以及Matake準(zhǔn)則等。Dang Van準(zhǔn)則認(rèn)為疲勞裂紋的萌生是由于材料內(nèi)部的臨界體積內(nèi)特征滑移帶上晶粒所受的塑形應(yīng)變引起,靜水應(yīng)力σH促使裂紋進(jìn)一步擴(kuò)展,與TIFF失效中的裂紋萌生擴(kuò)展較為一致,因此本文采用Dang Van多軸疲勞準(zhǔn)則將齒輪次表面應(yīng)力場(chǎng)轉(zhuǎn)化為等效應(yīng)力。風(fēng)電齒輪通過(guò)微觀修形優(yōu)化齒面載荷分布,首先通過(guò)齒輪箱有限元模型提取齒面嚙合線上各點(diǎn)單位長(zhǎng)度載荷,則次表面應(yīng)力場(chǎng)可根據(jù) Hertz接觸理論求解。
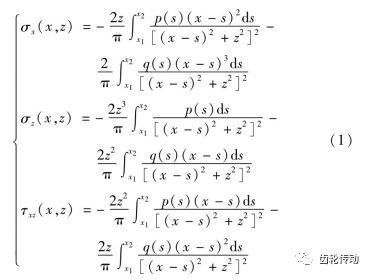
式中:p(s)為齒面壓力分布;q(s)為摩擦力分布;x為沿嚙合線方向坐標(biāo);z為沿齒面深度方向坐標(biāo),應(yīng)力分量得出后即可利用Dang Van多軸疲勞準(zhǔn)則求得目標(biāo)點(diǎn)等效應(yīng)力分布。

式中,材料疲勞參數(shù) 分別為對(duì)稱循環(huán)下材料的扭轉(zhuǎn)和拉壓疲勞極限,針對(duì)合金鋼風(fēng)電齒輪,
,靜水應(yīng)力σH和最大剪應(yīng)力τmax根據(jù)齒輪次表面應(yīng)力分量求得。
風(fēng)電齒輪滲碳熱處理和磨削后不可避免的會(huì)引入殘余應(yīng)力,將顯著影響齒輪接觸疲勞性能,通過(guò)考慮等效殘余應(yīng)力τRS(z)和殘余應(yīng)力擾動(dòng)量ΔτRS(z),對(duì)當(dāng)量應(yīng)力進(jìn)行修正

式中,τRS(z)和ΔτRS(z)可通過(guò)殘余應(yīng)力σRS(z)直接求解如下

通常齒輪殘余應(yīng)力可由x射線衍射儀直接測(cè)得,也可通過(guò)經(jīng)驗(yàn)公式近似計(jì)算。對(duì)于正常狀態(tài)的滲碳硬化齒輪,工程實(shí)踐中通常采用Hertter經(jīng)驗(yàn)公式計(jì)算殘余應(yīng)力
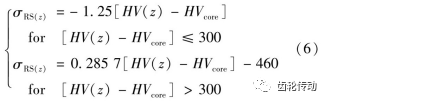
式中:HV為齒輪硬度梯度;HVcore為齒輪心部硬度。
齒輪材料強(qiáng)度及退化
根據(jù)Witzig的測(cè)試結(jié)果,材料質(zhì)量等級(jí)滿足 ISO6336-5 MQ級(jí)時(shí)齒輪內(nèi)部任意點(diǎn)許用強(qiáng)度服從以下經(jīng)驗(yàn)公式

式中:kτ,per為硬度梯度修正系數(shù),滲碳齒輪取0.4;kml為材料相關(guān)系數(shù),對(duì)于抗拉強(qiáng)度Rm≥900 MPa的材料,取值1.08。齒輪內(nèi)部疲勞斷裂失效風(fēng)險(xiǎn)程度可通過(guò)材料暴露系數(shù)AFF(z)表示

這一系數(shù)通過(guò)等效剪切應(yīng)力與許用強(qiáng)度比值表征疲勞失效風(fēng)險(xiǎn),根據(jù)Stahl等研究成果,滲碳齒輪材料暴露系數(shù)的安全臨界值為0.8。
材料強(qiáng)度伴隨服役時(shí)間增加呈現(xiàn)衰減趨勢(shì),其在任意時(shí)問f時(shí)的強(qiáng)度被定義為剩余強(qiáng)度,剩余強(qiáng)度的衰減量與材料內(nèi)部的微觀損傷密不可分。根據(jù)等損傷比剩余強(qiáng)度模型,在累積損傷量D的作用下,材料的剩余強(qiáng)度R(n)與初始強(qiáng)度R(0)和循環(huán)應(yīng)力峰值σmax有如下關(guān)系

方義慶等基于非線性損傷理論,通過(guò)試樣測(cè)試確定損傷變量參數(shù),給出基于非線性連續(xù)疲勞損傷的疲勞損傷量D的數(shù)學(xué)描述如下
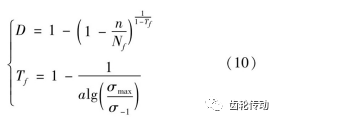
式中:n為載荷累計(jì)循環(huán)次數(shù);Nf為材料疲勞壽命,由材料S—N曲線確定,a為材料相關(guān)參數(shù),根據(jù)文獻(xiàn)取值 1.284??紤]風(fēng)電齒輪箱中各級(jí)齒輪轉(zhuǎn)速差異,將載荷循環(huán)次數(shù)n轉(zhuǎn)換為服役時(shí)間t,根據(jù)國(guó)家能源局發(fā)布的統(tǒng)計(jì)數(shù)據(jù),2020年全國(guó)風(fēng)電平均利用小時(shí)數(shù)為2 097 小時(shí),則服役時(shí)間可轉(zhuǎn)化為t/2 097年,關(guān)于時(shí)間的剩余強(qiáng)度模型可以表示為
式中:σmax為應(yīng)力最大值;Lf可轉(zhuǎn)化為總服役時(shí)間。由于滲碳齒輪鋼通常使用鋁作為強(qiáng)脫氧劑,該過(guò)程不可避免的會(huì)引入非金屬夾雜物,考慮非金屬夾雜物尺寸影響,材料疲勞循環(huán)次數(shù)和承受的對(duì)稱應(yīng)力幅的關(guān)系可表示如下

式中,areainc為夾雜物直徑,單位為μm,材料相關(guān)參數(shù)基于18CrNiM07-6齒輪鋼高周疲勞試驗(yàn)結(jié)果取值為:D=5.24×1056、m=22.03、α=-0.28。σ-1為單軸對(duì)稱循環(huán)疲勞極限,其與材料抗拉極限存在如下近似關(guān)系

為獲取滲碳和磨削后齒輪材料實(shí)際抗拉強(qiáng)度,從失效齒輪非工作面一側(cè)取樣,根據(jù)國(guó)際標(biāo)準(zhǔn)IS0 6892— 1:2019《金屬材料拉伸測(cè)試標(biāo)準(zhǔn)》,按圖1切割拉伸試樣,每片厚度0.9 mm。采用ANS電子拉力試驗(yàn)機(jī)對(duì)切片試樣進(jìn)行抗拉強(qiáng)度測(cè)試,得到三條較為規(guī)則的拉伸應(yīng)力應(yīng)變曲線,如圖1(d)所示,圖1(e)為試樣失效斷口,取三次測(cè)試的平均值抗拉強(qiáng)度為Rm=1 196 MPa。
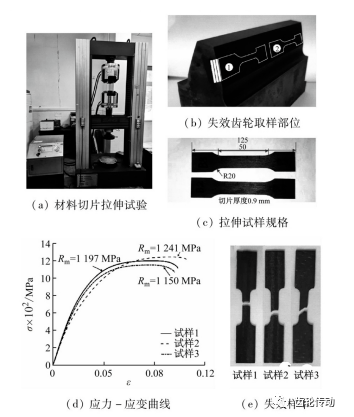
圖1 失效齒輪切片拉伸強(qiáng)度試驗(yàn)
齒輪內(nèi)部疲勞斷裂可靠度模型
傳統(tǒng)應(yīng)力強(qiáng)度干涉理論以極限狀態(tài)曲面劃分安全和失效區(qū)域與實(shí)際存在較大差異,風(fēng)電齒輪從安全運(yùn)行到失效存在一個(gè)模糊的漸變區(qū),采用降半梯形分布的隸屬函數(shù)描述如下
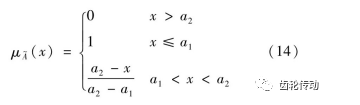
式中: 為模糊數(shù)x的隸屬度;a1和a2分別表示模糊上界和下界。針對(duì)齒輪可靠度分析引用擴(kuò)增系數(shù)β確定模糊邊界,βlower=0.75~1.0,βuppre=1.0~1.25,齒輪應(yīng)力超出材料強(qiáng)度才有可能發(fā)生損壞,取βlower= 1.0,βuppre=1.1??紤]齒輪強(qiáng)度退化,令a1=ri(t),a2=1.1ri(t),則可得到齒輪模糊可靠度函數(shù)
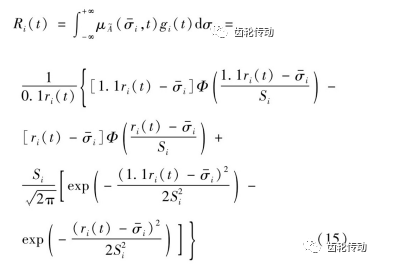
將式(3)、(12)求得的等效應(yīng)力和剩余強(qiáng)度代人式 (15),即可得到齒輪內(nèi)部疲勞斷裂可靠度計(jì)算模型如下
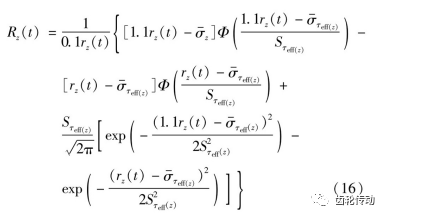
式中:rz(t)代表任意時(shí)刻、距齒面深度z點(diǎn)的齒輪材料剩余強(qiáng)度;分別代表任意點(diǎn)應(yīng)力標(biāo)準(zhǔn)差和均值。
二、研究對(duì)象
某2 MW風(fēng)電齒輪箱采用一級(jí)行星兩級(jí)平行軸傳動(dòng)結(jié)構(gòu),如圖2所示。
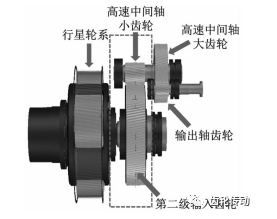
圖2 2 MW風(fēng)電齒輪箱傳動(dòng)結(jié)構(gòu)示意圖
該機(jī)組失效前累計(jì)發(fā)電 3 551 347千瓦時(shí),相當(dāng)于高速中間軸小齒輪額定功率運(yùn)行1 761.48小時(shí),折合0.84年。失效形式為高速中間級(jí)小齒輪內(nèi)部疲勞斷裂,如圖3所示,裂紋同時(shí)朝齒根和齒面兩個(gè)方向擴(kuò)展,在齒面半高處擴(kuò)展至齒面,表現(xiàn)出典型TIFF失效特征。裂紋源距齒面約3.5 mm,軸向處于1/3齒寬位置。在裂紋源區(qū)周圍可以觀察到顯著的貝紋狀推進(jìn)線,這是由于裂紋在擴(kuò)展過(guò)程中載荷變化或其他應(yīng)力干擾因素造成裂紋波動(dòng),貝紋線的凸起方向即為裂紋擴(kuò)展方向。
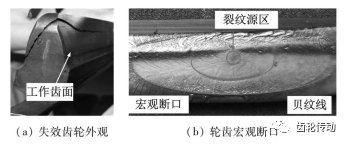
圖3 中間級(jí)小齒輪內(nèi)部疲勞斷裂失效
對(duì)圖3齒輪斷口進(jìn)行掃描電鏡檢查,疲勞輝紋明顯,裂紋源靠近齒頂、存在非金屬夾雜物聚集,圖4(c) 為該齒輪中典型球狀?yuàn)A雜物光學(xué)圖片,夾雜物直徑16 μm。經(jīng)能譜分析夾雜物主要成分為Al和O元素,與齒輪鋼脫氧環(huán)節(jié)引入的氧化鋁主要成分類同。
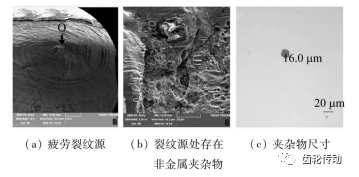
圖4 失效齒輪斷口電鏡檢查
表1 失效齒輪副主要參數(shù)
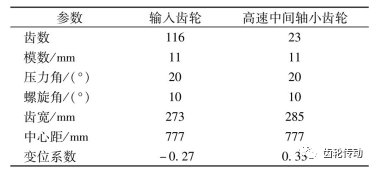
失效齒輪采用1 8CrNiM07-6材料,齒面滲碳淬火處理,該齒輪副額定轉(zhuǎn)速為384.75 r/min,額定扭矩為 55.89 kN·m,嚙合副宏觀幾何參數(shù)如表1所示。該 2 MW風(fēng)電齒輪箱設(shè)計(jì)壽命20年,本文基于主機(jī)廠家提供的風(fēng)場(chǎng)載荷譜和Miner法則,采用雨流計(jì)數(shù)法將風(fēng)機(jī)時(shí)問序列載荷等效為44個(gè)子工況進(jìn)行分析,如圖5 所示。
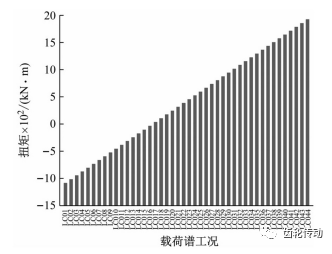
圖5 風(fēng)場(chǎng)等效載荷譜
三、分析討論
齒輪內(nèi)部疲勞斷裂危險(xiǎn)位置分析
考慮齒輪微觀修形影響,高速中間軸小齒輪在額定扭矩下沿嚙合線單位長(zhǎng)度載荷分布如圖6(a)所示,單位長(zhǎng)度載荷峰值為1 886.64 N/mm,位于單齒嚙合最高點(diǎn)HPSTC。對(duì)嚙合起始點(diǎn)SAP、單齒嚙合最低點(diǎn) LPSTC、節(jié)點(diǎn)PP、單齒嚙合最高點(diǎn)HPSTC、嚙合終止點(diǎn) EAP材料暴露系數(shù)進(jìn)行分析,結(jié)果如圖6(b)所示,最大值分別為0.103、0.593、0.598、0.607、0.220??梢娸d荷峰值、材料暴露系數(shù)最大值均出現(xiàn)在HPSTC點(diǎn),與失效齒輪裂紋源部位吻合,下文將著重分析該點(diǎn)對(duì)應(yīng)縱深截面上各點(diǎn)的疲勞斷裂失效風(fēng)險(xiǎn)。
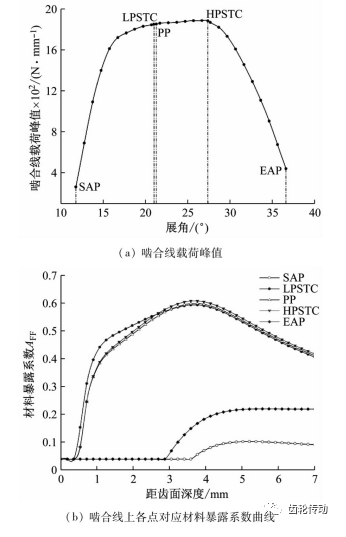
圖6 載荷與暴露系數(shù)分布
高速中間軸小齒輪HPSTC點(diǎn)對(duì)應(yīng)的靜水應(yīng)力σH、 最大剪應(yīng)力τmax、殘余剪應(yīng)力τRS(z)和ΔτRS(z)分布如圖7(a)所示,材料許用強(qiáng)度τper與齒輪熱處理后硬度梯度曲線近似分布;疊加殘余應(yīng)力分布影響后,當(dāng)量應(yīng)力τeff在距齒面2.88 mm處達(dá)到峰值107.57 MPa。內(nèi)部疲勞斷裂失效最大風(fēng)險(xiǎn)部位距齒面3.78 mm,如圖7 (b)所示,與圖3失效樣本3.5 mm裂紋源深偏差 8.0%。
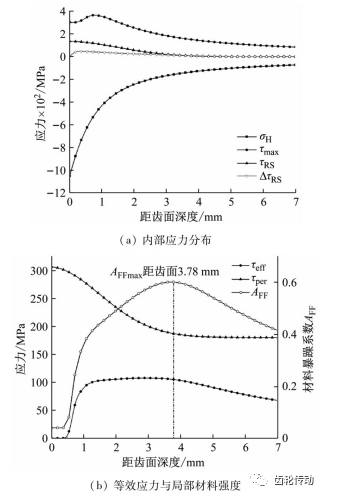
圖7 單齒嚙合最高點(diǎn)應(yīng)力分布
風(fēng)電齒輪內(nèi)部疲勞斷裂影響因素分析
風(fēng)電齒輪宏觀參數(shù)通過(guò)增速比、額定扭矩、機(jī)艙尺寸等約束,而為適應(yīng)風(fēng)電傳動(dòng)系統(tǒng)載荷多變的特點(diǎn),需要對(duì)齒輪進(jìn)行特殊微觀修形設(shè)計(jì),從而達(dá)到優(yōu)化傳動(dòng)系統(tǒng)動(dòng)態(tài)性能和齒面載荷分布的目的。失效齒輪采用了圖8所示的齒向鼓形修形、齒向螺旋角修形以及齒端減薄修形。鑒于齒輪宏觀參數(shù)針對(duì)內(nèi)部疲勞斷裂失效可調(diào)整空間較小,基于前述可靠性分析模型,選取齒輪表面硬度、心部硬度、有效硬化層深度、齒頂修緣、齒向鼓形、齒向斜度6個(gè)參數(shù)進(jìn)行因子試驗(yàn)研究,進(jìn)行主效應(yīng)和交互效應(yīng)分析。采用部分因子試驗(yàn)設(shè)計(jì)方法,試驗(yàn)次數(shù)20次,試驗(yàn)參數(shù)如表2所示。其中因素A表面硬度低水平為57HRC、高水平為62HRC;因素B心部硬度低水平為30HRC、高水平為40HRC;因素c有效滲碳層深度低水平為2 mm、高水平為2.4 mm;因素D齒頂修緣低水平為50μm、高水平為120μm;因素E齒向鼓形低水平為0、高水平為40μm;因素F齒向斜度低水平為0、高水平為90μm。
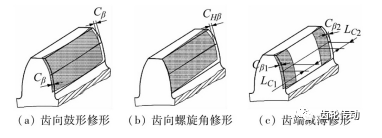
圖8 齒輪常用修形方式示意圖
表2部分析因試驗(yàn)參數(shù)
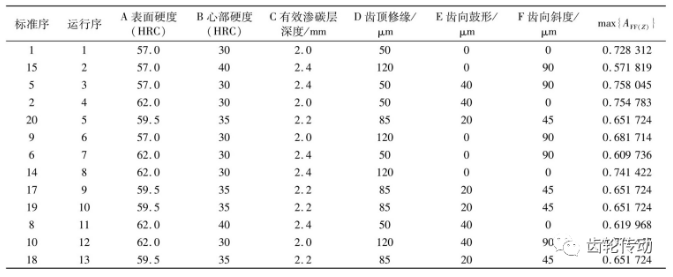
通過(guò)因子交互效應(yīng)各因子對(duì)應(yīng)回歸方程系數(shù)的影響,分組為:A表面硬度×B心部硬度、A表面硬度×C 有效滲層深度、B心部硬度×c有效滲層深度、D齒頂修緣×E齒向鼓形、E齒向鼓形×F齒向斜度五組,對(duì)存在混雜進(jìn)行了剔除,相關(guān)參數(shù)如表3所示。
每種因子組合下材料暴露系數(shù)的最大值為 max{AFF,CP(Z)},各運(yùn)行序?qū)?yīng)的材料暴露系數(shù)曲線如圖9(a)所示。對(duì)A、B、C、D、E、F、AB、BC、AC、DE、EF 11組因子及其有效組合,采用標(biāo)準(zhǔn)化效應(yīng)Pareto進(jìn)行顯著性影響分析,由圖9(b)統(tǒng)計(jì)顯著性參考線可知,對(duì)材料暴露系數(shù)影響顯著性從大到小依次為B心部硬度、E齒向鼓形、F齒向斜度、D齒頂修緣、A表面硬度、EF、AC、DE、AB、BC、C有效滲碳層深度。由式(5)可知,針對(duì)給定齒面硬度,心部硬度約大,殘余壓應(yīng)力越小,對(duì)應(yīng)齒輪內(nèi)部等效應(yīng)力越大,故心部硬度對(duì)材料暴露系數(shù)影響最顯著。齒向鼓形直接影響單位長(zhǎng)度線載荷,進(jìn)而影響內(nèi)部Dang Van多軸應(yīng)力,故也對(duì)材料暴露系數(shù)影響顯著。剩余因子或其組合對(duì)材料暴露系數(shù)的影響主要也是通過(guò)殘余應(yīng)力和Dang Van多軸應(yīng)力兩種途徑實(shí)現(xiàn),只是顯著性存在差異。
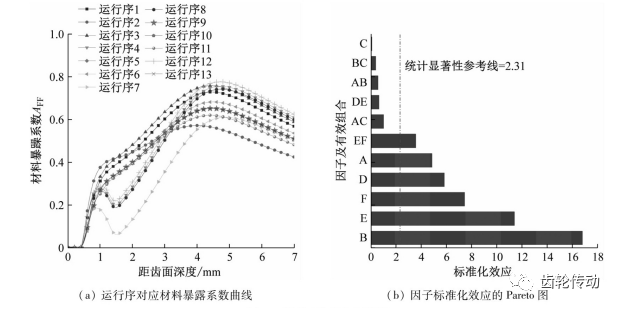
圖9 部分析因試驗(yàn)結(jié)果
表3 因子主效應(yīng)及交互效應(yīng)影響系數(shù)
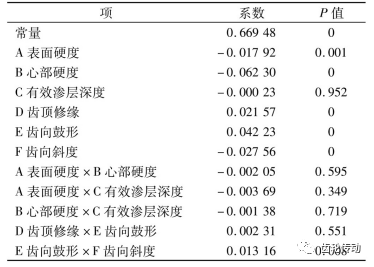
齒輪內(nèi)部疲勞斷裂可靠性分析及優(yōu)化
基于風(fēng)電齒輪失效分析案例,針對(duì)齒輪鍛件常出現(xiàn)的氧化鋁類夾雜物,根據(jù)GB/T10561《鋼中非金屬夾雜物含量的測(cè)定標(biāo)準(zhǔn)評(píng)級(jí)圖顯微檢驗(yàn)法》中有關(guān)細(xì)系球狀氧化物的定義,選取3、5.5、8、16μm四種夾雜物直徑,進(jìn)行高速中問軸小齒輪TIFF可靠度對(duì)比,結(jié)果如圖10所示。可見,夾雜物尺寸通過(guò)公式(14)影響材料疲勞循環(huán)次數(shù),進(jìn)而影響齒輪TIFF可靠度,影響趨勢(shì)呈非線性特點(diǎn)。由圖10(d)可見,失效齒輪含16μm 三氧化二鋁夾雜物,TIFF可靠度經(jīng)0.32年由 0.999 966衰減至0.968 399,與該齒輪失效時(shí)間0.84 年處于同一量級(jí),但理論計(jì)算結(jié)果偏于保守。
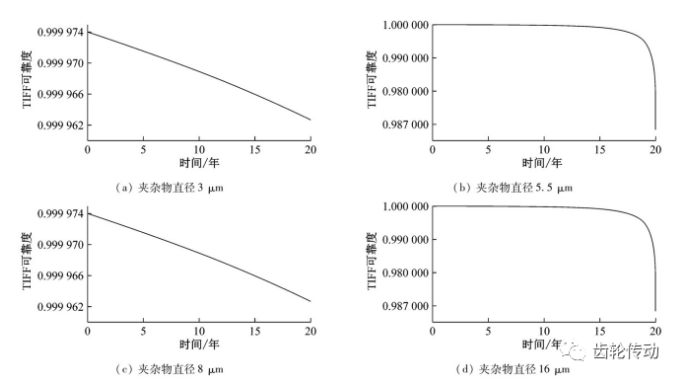
圖10 夾雜物對(duì)齒輪內(nèi)部疲勞斷裂可靠度影響
采用最優(yōu)化設(shè)計(jì)方法,對(duì)表3獲得的齒輪材料暴露系數(shù)回歸方程進(jìn)行望小優(yōu)化設(shè)計(jì),得到6個(gè)主因子最優(yōu)參數(shù)分別為:A表面硬度62HRC、B心部硬度 40HRC、C有效滲碳層深度2.4 mm、D齒頂修緣50 μm、E齒向鼓形0、F齒向斜度90μm。材料暴露系數(shù)越小,對(duì)應(yīng)齒輪內(nèi)部疲勞斷裂可靠度越高。考慮夾雜物直徑為5.5μm時(shí)的情況,將優(yōu)化前后兩組參數(shù)代人式(16),得到可靠度曲線如圖11所示。優(yōu)化前高速中間軸小齒輪TIFF可靠度初始值為0.999 967,經(jīng)過(guò)20 年運(yùn)行后變?yōu)?.968 399;優(yōu)化后TIFF可靠度初始值為 1.000 000,經(jīng)20年運(yùn)行后變?yōu)?.972 678。
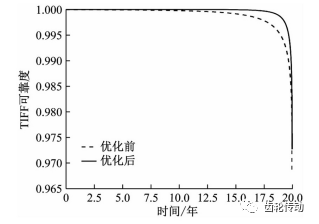
圖11 齒輪內(nèi)部疲勞斷裂失效可靠度優(yōu)化
四、結(jié)論
(1)基于應(yīng)力強(qiáng)度模糊干涉函數(shù)和齒輪材料強(qiáng)度退化理論,結(jié)合Dang Van多軸疲勞準(zhǔn)則建立風(fēng)電滲碳齒輪內(nèi)部疲勞斷裂可靠度分析模型,通過(guò)某2 MW風(fēng)電齒輪箱高速中間軸小齒輪失效樣本裂紋源深度對(duì)比,驗(yàn)證了模型的適用性。
(2)采用部分因子試驗(yàn)設(shè)計(jì)方法,確定對(duì)齒輪內(nèi)部斷裂失效影響權(quán)重從大到小的主因子分別為:心部硬度、齒向鼓形、齒向斜度、齒頂修緣、表面硬度、有效滲碳層深度。心部硬度越大、齒向鼓形越小,齒輪內(nèi)部疲勞斷裂失效風(fēng)險(xiǎn)越小。
(3)針對(duì)因子試驗(yàn)回歸方程進(jìn)行望小優(yōu)化設(shè)計(jì),獲得風(fēng)電齒輪內(nèi)部疲勞斷裂各影響因子最佳匹配參數(shù),優(yōu)化后20年齒輪內(nèi)部疲勞斷裂可靠度由0.968 399 提高至0.972 678,本文提出的可靠度優(yōu)化方法可為高扭矩密度風(fēng)電齒輪設(shè)計(jì)提供有益借鑒。
參考文獻(xiàn)略.