齒輪作為工業(yè)設(shè)備的重要組成部件,隨著現(xiàn)代加工工藝的發(fā)展,其加工精度要求也在不斷提高。高精密齒輪的加工質(zhì)量,直接影響了工業(yè)設(shè)備的工作性能。滾齒加工的方式具有適應(yīng)性強(qiáng)、加工效率高等優(yōu)勢(shì),近年來(lái)廣泛應(yīng)用在工業(yè)設(shè)備中高精密齒輪加工過(guò)程中。在實(shí)際加工過(guò)程中,軸運(yùn)動(dòng)、夾具、齒輪加工刀具等都存在引發(fā)加工誤差的因素。通常情況下,需要采用誤差預(yù)防和誤差補(bǔ)償兩種方法,提升齒輪加工精度。但是,高精密齒輪制作過(guò)程中,目前的誤差預(yù)防策略難以發(fā)揮較好的應(yīng)用效果。因此,很多學(xué)者開始針對(duì)誤差補(bǔ)償技術(shù)進(jìn)行研究。
文獻(xiàn)針對(duì)加工后的實(shí)際齒輪進(jìn)行測(cè)量,在回轉(zhuǎn)中心和芯軸中心完全重合狀態(tài)下,明確齒輪存在的同向誤差和反向誤差。依據(jù)芯軸徑向跳動(dòng)誤差計(jì)算修正值,實(shí)現(xiàn)齒輪加工誤差補(bǔ)償,但該方法應(yīng)用后齒輪的齒形法向偏差依舊較大。文獻(xiàn)以齒輪加工過(guò)程中工件與刀具的相對(duì)運(yùn)動(dòng)關(guān)系為基礎(chǔ),結(jié)合嚙合原理生成齒面模型。對(duì)比實(shí)際齒面與理論齒面,建立幾何加工誤差控制模型。分析加工參數(shù)敏感性,選取高敏感性的加工參數(shù),計(jì)算誤差補(bǔ)償變量。運(yùn)用最小二乘法描述誤差補(bǔ)償問(wèn)題,再結(jié)合改進(jìn) L-M 算法實(shí)現(xiàn)誤差補(bǔ)償,但該方法計(jì)算復(fù)雜度較高。文獻(xiàn)以機(jī)床熱變形誤差為核心,通過(guò)直接測(cè)量和間接測(cè)量?jī)煞N方式,了解滾齒輪加工刀具與工件主軸的運(yùn)動(dòng)關(guān)系,構(gòu)建變形誤差模型,并以此為基礎(chǔ)提出變形誤差補(bǔ)償策略,但該方法操作煩瑣且成本較高。
以解決上述提出誤差補(bǔ)償技術(shù)的不足之處為目標(biāo),將高精密齒輪作為主要研究對(duì)象,提出一種新的加工誤差補(bǔ)償技術(shù)。相比傳統(tǒng)的無(wú)偏估計(jì)計(jì)算方法,提出的補(bǔ)償技術(shù)運(yùn)用了敏感系數(shù)矩陣計(jì)算修正參數(shù),得出更加精確的修正量。根據(jù)驗(yàn)證結(jié)果可以看出,所提出的誤差補(bǔ)償技術(shù)應(yīng)用后,齒形法向偏差得到大幅度降低,確保齒輪加工精密滿足工業(yè)加工需求。
一、工業(yè)設(shè)備中高精密齒輪加工誤差補(bǔ)償技術(shù)設(shè)計(jì)
建立高精密齒輪加工模型
刀具切削是高精密齒輪加工的主要環(huán)節(jié),為滿足齒輪切削要求,機(jī)床運(yùn)動(dòng)軸主要包括六個(gè)重要組成部分,分別是切削運(yùn)動(dòng)軸 B、分齒運(yùn)動(dòng)軸 C、軸線走刀運(yùn)動(dòng)軸 Z、徑向走刀運(yùn)動(dòng)軸 X、切向走刀運(yùn)動(dòng)軸 Y、滾刀角度調(diào)整軸 A。在伺服電機(jī)的驅(qū)動(dòng)作用下,齒輪加工機(jī)床的各個(gè)運(yùn)動(dòng)軸同時(shí)開始工作,高齒輪加工具體原理如圖1所示。
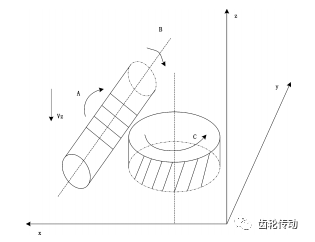
圖 1 高精密齒輪加工原理示意圖
圖 1 描述了工業(yè)設(shè)備中高精密齒輪加工原理,也屬于滾齒加工模式。其中,Z 軸和 B、C、Y 三個(gè)軸之間存在聯(lián)動(dòng)性,可實(shí)現(xiàn)高精密齒輪加工過(guò)程中的展成運(yùn)動(dòng)、軸向差動(dòng)補(bǔ)償運(yùn)動(dòng)和切向補(bǔ)償運(yùn)動(dòng),也正是通過(guò)這三項(xiàng)運(yùn)動(dòng),將不同運(yùn)動(dòng)軸之間的耦合關(guān)系描述為:

公式中,s 表示高精密齒輪加工工作臺(tái)轉(zhuǎn)速,w 表示滾刀數(shù)量,e 表示齒輪齒數(shù),n 表示滾刀轉(zhuǎn)速,γ 表示齒輪加工螺旋角,θ 表示滾刀架安裝角,v 表示進(jìn)給速度,z 表示齒輪軸向,y 表示齒輪切向,vz 表示軸向進(jìn)給速度,vy 表示切向進(jìn)給速度,sin 表示正弦函數(shù),cos 表示余弦函數(shù)。
通過(guò)公式(1)描述了工業(yè)滾刀加工設(shè)備與待加工齒輪之間的關(guān)系,結(jié)合二者相關(guān)參數(shù)獲取高精密齒輪加工嚙合比,明確正常狀態(tài)下高精密齒輪加工運(yùn)動(dòng)。
測(cè)量齒輪齒面離散化誤差
由于工業(yè)設(shè)備中高精度齒輪的齒面空間具有復(fù)雜性,為了便于分析齒輪的齒形誤差,文中運(yùn)用離散化分析理念比較理論齒面與實(shí)際加工齒面,通過(guò)二者之間的差異獲取齒形誤差值。針對(duì)加工后的高精度齒面進(jìn)行旋轉(zhuǎn)投影,運(yùn)用網(wǎng)格規(guī)劃的方法建立投影網(wǎng)格,明確高精度齒輪的齒面形狀以及齒面離散點(diǎn)分布情況,具體如圖 2 所示。以齒輪設(shè)計(jì)交叉點(diǎn)為原點(diǎn)建立坐標(biāo)系,在齒坯參數(shù)、網(wǎng)格收縮量的共同作用下,明確各離散點(diǎn)的坐標(biāo)。
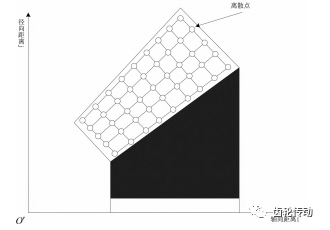
圖 2 齒面離散點(diǎn)示意圖
設(shè)置圖 2 中 i 軸為齒輪軸線,則齒面上方離散點(diǎn)到齒輪軸線之間的距離以及離散點(diǎn)到坐標(biāo)原點(diǎn)的距離,分別表示為:

公式中,α 表示離散點(diǎn)到齒輪軸線的距離,也是搖臺(tái)角相位角函數(shù),β 表示離散點(diǎn)到坐標(biāo)原點(diǎn)的距離,也是刀盤相位角函數(shù),r 表示理論齒面離散點(diǎn)徑矢,p 表示齒輪軸線。
明確離散點(diǎn)坐標(biāo)值后,采用二元迭代法計(jì)算對(duì)應(yīng)點(diǎn)在理論齒面的徑矢和法矢,再將圖 2 所示的坐標(biāo)系轉(zhuǎn)換為齒輪測(cè)量中心坐標(biāo)系,依據(jù)離散點(diǎn)間坐標(biāo)可以直接描述齒形誤差。齒輪測(cè)量中心坐標(biāo)系是以位于齒面中心的離散點(diǎn)為參考,設(shè)置該點(diǎn)的加工誤差為 0。設(shè)置測(cè)頭從離散點(diǎn)的法矢方向向?qū)嶋H齒面移動(dòng),再進(jìn)行數(shù)據(jù)處理,獲取齒形誤差值。設(shè)置拓?fù)淦矫鏋閰⒖键c(diǎn)所在的平面,并設(shè)置切點(diǎn)為坐標(biāo)原點(diǎn),根據(jù)齒形誤差值生成可以描述加工誤差的誤差曲面。
計(jì)算加工誤差補(bǔ)償修正量
在高精度齒輪加工之前,確保加工機(jī)床的安裝參數(shù)在合理范圍內(nèi),再以齒輪齒面離散化誤差測(cè)量結(jié)果為基礎(chǔ),設(shè)計(jì)以敏感系數(shù)矩陣為核心的誤差補(bǔ)償參數(shù)計(jì)算方法。
考慮到高精度齒輪加工后,齒形上方任意一點(diǎn)的誤差是多項(xiàng)機(jī)床調(diào)整參數(shù)引起誤差的總體表現(xiàn),也就是說(shuō),各項(xiàng)微小誤差產(chǎn)生的變動(dòng)量相加形成齒面法向誤差。因此,將理論齒面法向誤差描述為:

公式中,t 表示理論齒面表達(dá)式,δ 表示法向誤差,u 表示齒面的曲線參變數(shù),ϑ 表示螺旋參數(shù),h 表示齒輪加工機(jī)床,H 表示加工機(jī)床總項(xiàng)數(shù),ω 表示機(jī)床調(diào)整參數(shù)的微小變化量。
考慮到曲線參變數(shù)向量和螺旋參數(shù)向量,均與齒面法矢呈現(xiàn)出垂直關(guān)系,則法向誤差可描述為以下公式:
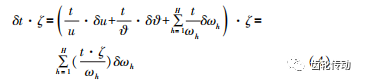
公式中,ζ 表示齒面數(shù)據(jù)點(diǎn)的法向矢量。在此基礎(chǔ)上,建立齒形法向誤差矩陣:

公式中,c 表示齒面數(shù)據(jù)點(diǎn),ε 表示齒面數(shù)據(jù)點(diǎn)總數(shù),L 表示機(jī)床調(diào)整參數(shù)變化的敏感系數(shù)矩陣。
對(duì)公式(5)進(jìn)行求解,可進(jìn)一步得出敏感系數(shù)矩陣,將其看作初始變換矩陣。提取敏感度較高的機(jī)床調(diào)整參數(shù),作為加工誤差補(bǔ)償?shù)闹匾獙?duì)象,計(jì)算加工誤差補(bǔ)償參數(shù)。
結(jié)合法向誤差測(cè)量矩陣點(diǎn)和敏感系數(shù)矩陣,在最小二乘分析方法的作用下,計(jì)算機(jī)床參數(shù)修正量。機(jī)床調(diào)整參數(shù)實(shí)際修正過(guò)程中,為確保加工誤差補(bǔ)償效果較好,且不影響齒輪加工操作。文中依托于比例修正參數(shù)計(jì)算方法,引入 SGM 加工思想,針對(duì)主要齒輪加工機(jī)床調(diào)整參數(shù),設(shè)置對(duì)應(yīng)的修正比例參數(shù),分別負(fù)責(zé)修正齒形螺旋角、齒形齒長(zhǎng)曲率、齒形齒廓曲率以及齒形短程撓率。其中,徑向刀位改變量和角向刀位改變量,在每種比例修正參數(shù)中都屬于不可或缺的內(nèi)容。上述提出的 4 種比例修正參數(shù),分別對(duì)應(yīng)高精度齒輪加工補(bǔ)償誤差所涉及的主要調(diào)整參數(shù),將其與敏感系數(shù)矩陣相結(jié)合,可針對(duì)齒形誤差測(cè)量結(jié)果計(jì)算出最優(yōu)修正值。需要注意的是,比例修正參數(shù)設(shè)置過(guò)程中,并未涉及壓力角誤差,這是因?yàn)槟X機(jī)砂輪切削刃的壓力角的改變,會(huì)對(duì)刀具壓力角產(chǎn)生直接影響,從而間接達(dá)到補(bǔ)償齒形壓力角誤差的目的。
針對(duì)正常狀態(tài)下,高精度齒輪加工機(jī)床調(diào)整參數(shù)進(jìn)行分析,可明確離散點(diǎn)在理論齒面上對(duì)應(yīng)的徑矢、法矢。也就是說(shuō),根據(jù)敏感系數(shù)矩陣和比例修正系數(shù)對(duì)機(jī)床調(diào)整參數(shù)進(jìn)行修正后,建立加工誤差補(bǔ)償后的齒面方程。采用最優(yōu)化計(jì)算方法,針對(duì)理論齒面各離散點(diǎn)求取最佳齒形誤差,并對(duì)上文設(shè)置的 4 種比例修正參數(shù),分別給定合理的改變倍數(shù),更好地補(bǔ)償齒形誤差值,保證工業(yè)設(shè)備中高精度齒輪的理論齒面和實(shí)際齒面保持一致。
實(shí)現(xiàn)數(shù)控在機(jī)誤差補(bǔ)償
文中以修正量計(jì)算結(jié)果為基礎(chǔ),設(shè)計(jì)基于數(shù)控程序的補(bǔ)償方法,對(duì)機(jī)床安裝參數(shù)進(jìn)行快速修正,實(shí)現(xiàn)齒輪加工誤差補(bǔ)償。文中應(yīng)用以數(shù)控程序?yàn)榛A(chǔ)的齒輪加工誤差補(bǔ)償方法,不需要更改加工機(jī)床的硬件設(shè)備,保證了誤差補(bǔ)償?shù)撵`活性。以 NC 程序編程模塊為核心,編寫數(shù)控加工補(bǔ)償 NC 代碼,再將其傳遞至高精度齒輪加工系統(tǒng),實(shí)現(xiàn)數(shù)控在機(jī)誤差補(bǔ)償,該補(bǔ)償方法具體實(shí)現(xiàn)模式如圖 3 所示。
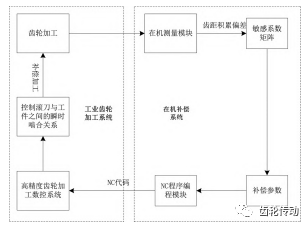
圖 3 齒輪加工誤差在機(jī)補(bǔ)償模式
圖 3 所示的齒輪加工誤差在機(jī)補(bǔ)償模式運(yùn)行后,累積偏差修正量主要通過(guò)三種方法,分別為滾刀轉(zhuǎn)速的改變、回轉(zhuǎn)工作臺(tái)轉(zhuǎn)速的改變和滾刀軸向運(yùn)動(dòng)的改變。文中綜合上述三種補(bǔ)償方式,在工業(yè)設(shè)備中高精度齒輪加工誤差補(bǔ)償目標(biāo)的同時(shí),不影響加工機(jī)床的正常嚙合行為。
在機(jī)補(bǔ)償系統(tǒng)實(shí)踐操作過(guò)程中,需要先根據(jù)工作臺(tái)與滾刀軸之間的嚙合運(yùn)用模式,了解高精度齒輪加工的整體數(shù)控代碼,根據(jù)加工誤差補(bǔ)償修正量計(jì)算結(jié)果,通過(guò) NC 程序編程模塊,得到補(bǔ)償 NC 代碼。在離散化處理后的齒輪加工過(guò)程中,插入加工補(bǔ)償函數(shù),并將 NC 程序輸入結(jié)果傳遞給加工數(shù)控系統(tǒng),完成齒輪加工誤差補(bǔ)償。
二、應(yīng)用分析
文中以減少工業(yè)設(shè)備中高精度齒輪加工誤差為目的提出一種新的誤差補(bǔ)償技術(shù),為了驗(yàn)證該技術(shù)的實(shí)際應(yīng)用效果,特進(jìn)行應(yīng)用分析。
應(yīng)用準(zhǔn)備
本次實(shí)驗(yàn)以內(nèi)齒圓柱直齒輪為研究對(duì)象,針對(duì)該齒輪加工過(guò)程進(jìn)行分析,得出表 1 所示的工件和機(jī)床調(diào)整參數(shù),作為誤差補(bǔ)償技術(shù)應(yīng)用效果分析的基礎(chǔ)。
表 1 工件和機(jī)床調(diào)整參數(shù)
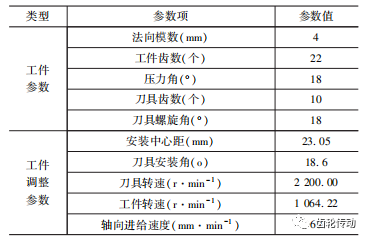
為便于分析文中提出技術(shù)的誤差補(bǔ)償效果,采用人為給定誤差擾動(dòng)的方式,將中心距誤差、角度誤差和運(yùn)動(dòng)精度誤差分別描述為+0. 5 mm、+0. 2°和+2. 5 r/ min。在此條件下進(jìn)行工業(yè)設(shè)備中高精度齒輪加工,并針對(duì)加工后的齒輪進(jìn)行測(cè)量,現(xiàn)場(chǎng)測(cè)量情況如圖 4 所示。
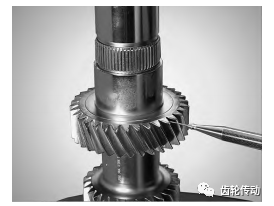
圖 4 齒輪齒形測(cè)量示意圖
將高精度齒輪的中心點(diǎn)表示為 0 mm,左側(cè)齒形描述為負(fù)數(shù),右側(cè)齒形表示為正數(shù)齒形寬度。則可得到這些誤差綜合影響之下的齒形測(cè)量結(jié)果,如圖 5 所示。
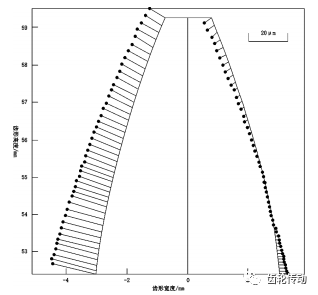
圖 5 誤差綜合影響下齒形測(cè)量結(jié)果
根據(jù)圖 5 可知,正常加工狀態(tài)下,左側(cè)齒形的最大法向偏差為 23. 7μm,而右側(cè)齒輪所呈現(xiàn)出的最大法向偏差為 4. 8μm。在上述準(zhǔn)備條件下,應(yīng)用文中提出的誤差補(bǔ)償技術(shù)進(jìn)行齒輪加工誤差補(bǔ)償,再對(duì)比補(bǔ)償后齒形測(cè)量結(jié)果,明確所提技術(shù)的可行性。
計(jì)算修正量
按照文中研究?jī)?nèi)容,以敏感系數(shù)矩陣法為基礎(chǔ),進(jìn)行加工誤差補(bǔ)償分析,得出機(jī)床調(diào)整參數(shù)修正量,與原始機(jī)床調(diào)整參數(shù)相結(jié)合,獲取修正后參數(shù)值如表 2 所示。
表 2 修正后機(jī)床調(diào)整參數(shù)
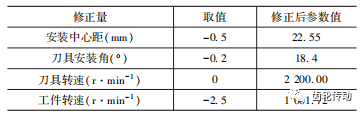
從表 2 可以看出,通過(guò)敏感系數(shù)矩陣求解出的機(jī)床調(diào)整參數(shù)修正量,與人為給定誤差擾動(dòng)相符,表明修正量計(jì)算結(jié)果真實(shí),將其輸入數(shù)控系統(tǒng)內(nèi),實(shí)現(xiàn)高精度齒輪加工誤差補(bǔ)償。
誤差補(bǔ)償結(jié)果分析
運(yùn)用修正后的齒輪加工機(jī)床,再次進(jìn)行內(nèi)齒圓柱直齒輪加工,對(duì)加工后齒輪進(jìn)行現(xiàn)場(chǎng)測(cè)量,得到圖 6 所示的齒形測(cè)量結(jié)果。
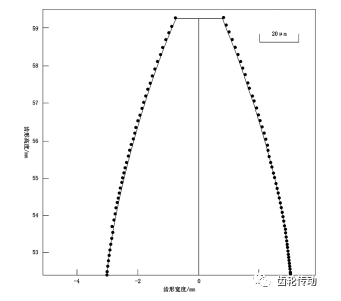
圖 6 加工誤差補(bǔ)償后齒形測(cè)量結(jié)果
為更加直觀地描述所提誤差補(bǔ)償技術(shù)的應(yīng)用效果,分別計(jì)算補(bǔ)償前齒輪齒形法向偏差和補(bǔ)償后齒輪齒形法向偏差,得到結(jié)果如圖 7 所示。
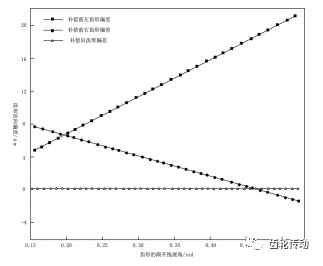
圖 7 加工誤差補(bǔ)償前后齒形法向偏差對(duì)比圖
根據(jù)圖 7 所示的補(bǔ)償前后齒形法向偏差對(duì)比結(jié)果可知,補(bǔ)償前齒形的左側(cè)齒形法向偏差呈現(xiàn)出不斷上升的趨勢(shì),右側(cè)齒形法向偏差呈現(xiàn)出下降趨勢(shì),但并未保持在誤差為 0 μm 的狀態(tài)。而應(yīng)用文中所提技術(shù)進(jìn)行機(jī)床參數(shù)修正后,齒輪加工誤差得到補(bǔ)償,補(bǔ)償后左、右齒形的最大法向偏差,均小于 0. 1 μm。對(duì)比修正前齒形法 向偏差可以看出,文中提出誤差補(bǔ)償技術(shù)具有極佳的修正效果,確保高精度齒輪加工精度保持在合理范圍內(nèi)。
三、結(jié)束語(yǔ)
文中圍繞工業(yè)設(shè)備中齒輪加工誤差進(jìn)行研究,提出一種新的誤差補(bǔ)償技術(shù),確保齒輪加工精度滿足高精度要求。從齒輪加工原理入手,對(duì)加工產(chǎn)生的誤差深入測(cè)量和分析,運(yùn)用敏感系數(shù)矩陣計(jì)算出最優(yōu)修正參數(shù),再通過(guò)在機(jī)補(bǔ)償技術(shù),在數(shù)控系統(tǒng)的作用下,實(shí)現(xiàn)加工誤差補(bǔ)償。從實(shí)驗(yàn)驗(yàn)證結(jié)果來(lái)看,文中提出的補(bǔ)償技術(shù)具有可行性,可實(shí)現(xiàn)齒形法向偏差的大幅度降低,保證齒輪加工精度滿足要求。
參考文獻(xiàn)略.