隨著機床市場從批量化需求向多品種、小批量需求轉(zhuǎn)變,柔性制造系統(tǒng)憑借“能夠靈活應對市場需求的變化”這一優(yōu)勢而日益受到重視。四川普什寧江機床有限公司(以下簡稱“普什寧江”)研制的箱體類零件加工柔性制造系統(tǒng),由多臺精密臥式加工中心(可配清洗機、三坐標測量機等數(shù)控裝備)、物流貯運系統(tǒng)和總控系統(tǒng)組成,實現(xiàn)了物流、加工及輔助設備的一體化集成,能夠確保在一定的時間內(nèi),實現(xiàn)機床的零停機,從而滿足了用戶對高效加工的要求。由于是多臺機床(一般為3~6臺)的集成,使得機床、刀具、清洗和檢測等資源得到了最大程度的共享利用。在總控控制下,該柔性制造系統(tǒng)可以實現(xiàn)多種零件的混流加工,并允許長時間的無人看管連續(xù)運行。
2016年5月25日,由普什寧江牽頭承擔的“機床箱體類精密柔性制造系統(tǒng)研發(fā)及示范應用”課題通過了任務終驗收。該課題由普什寧江聯(lián)合武漢華中數(shù)控股份有限公司、四川大學和重慶大學共同完成,目標是研制精密柔性制造系統(tǒng),實現(xiàn)多品種箱體類零件的單件或批量的柔性、高效、高精加工,并在機床企業(yè)實現(xiàn)示范應用。
課題從2012年1月開始實施,歷經(jīng)3年多時間,完成了任務書規(guī)定的所有研究內(nèi)容。根據(jù)機床制造企業(yè)提升設備能力、適應機床箱體類零件多品種、變批量、柔性、自動化及智能化加工的需求,該課題設計制造了機床箱體類零件精密柔性制造系統(tǒng),研制出630mm和800㎜規(guī)格(各4 臺)的兩條精密柔性制造系統(tǒng)FMS63和FMS80,其中,F(xiàn)MS80配套進口數(shù)控系統(tǒng),F(xiàn)MS63配套國產(chǎn)數(shù)控系統(tǒng)。兩條精密柔性制造系統(tǒng)的工作臺交換重復定位精度0.002mm,運輸小車快移速度75m/min,精密臥式加工中心THM6380的平均故障間隔時間MTBF為1645.1h。
課題開展了基于國產(chǎn)數(shù)控系統(tǒng)的FMS應用技術、在線測量及監(jiān)控技術、可靠性技術、刀具及工裝夾具管理技術以及基于MES無縫集成的FMS應用支撐技術等技術的研究。建成的兩套 FMS在普什寧江的精密加工事業(yè)部實現(xiàn)了箱體類零件的混流加工,對可靠性理論和方法進行了驗證,并開展了國產(chǎn)數(shù)控系統(tǒng)與進口數(shù)控系統(tǒng)的對比試驗,使國產(chǎn)數(shù)控系統(tǒng)在應用驗證中得到改進。
產(chǎn)品性能介紹
作為新一代產(chǎn)品,機床箱體類零件精密柔性制造系統(tǒng)FMS具有高柔性、自動化和智能化等特點。
高柔性:研制成功的FMS63和FMS80兩條機床箱體類零件精密柔性制造系統(tǒng),滿足了床身、立柱等8種機床零件、4種工藝路線并行加工的要求,實現(xiàn)了多品種、變批量的混流加工。
自動化:自主研制的RGV輸送小車,集成自動上下料、物流、智能識別及自動控制等技術,具備作業(yè)計劃制定、任務分配、可視化操作和監(jiān)控等功能,能24h連續(xù)工作,并能在無人看管的情況下連續(xù)運行16h。
智能化:自主開發(fā)的總控系統(tǒng),能夠完成對FMS中所有設備的監(jiān)控、計劃管理和零件調(diào)度。向下層,可對物流系統(tǒng)與加工系統(tǒng)進行控制,實現(xiàn)零件的換裝、混流和混工序;向上層,MES系統(tǒng)實現(xiàn)信息的傳遞。通過智能識別、智能調(diào)度等功能,實現(xiàn)零件的柔性化加工。在更換加工對象時,借助零件識別、智能調(diào)度和混流加工技術,無需對FMS進行停機調(diào)試即可實現(xiàn)品種的自動轉(zhuǎn)換,從而實現(xiàn)了基于混流加工的“零”調(diào)整。
表 FMS63和FMS80的主要技術參數(shù)
關鍵技術研究
1.典型機床箱體類零件加工工藝技術及FMS系統(tǒng)集成設計
根據(jù)箱體類零件工序比較集中的特點,開展了典型機床箱體類零件工藝需求分析和加工工藝技術研究,完成了機床箱體類精密FMS的總體設計;開展了柔性生產(chǎn)制造技術研究,實現(xiàn)了機床箱體類零件的多品種、小批量的柔性、高效、高精及混流加工的生產(chǎn)示范;建立了加工工藝參數(shù)數(shù)據(jù)庫;開展了機床箱體類零件加工特征自動建模技術的研究;開展了國產(chǎn)數(shù)控刀具切削性能和高效柔性夾具運用的研究。
(1)基于機床箱體類零件加工具有工序長、種類多以及精度高的特點,采用半精加工和精加工的加工中心進行共線配置,同時采用刀具配送、加工程序后臺保障等方式,確定了機床箱體類零件的精密FMS 集成方案,規(guī)劃設計了其物理布局、設備和控制結(jié)構等。
(2)完成了柔性制造系統(tǒng)模塊化、單元化設計;掌握了單機聯(lián)線裝配調(diào)試等技術,形成了相應的工藝和質(zhì)量控制文件;在CAPP平臺基礎上,初步建立了加工工藝參數(shù)數(shù)據(jù)庫 。
(3)實現(xiàn)了刀具、夾具的智能化管理,開展了夾具定位和裝夾等技術的研究和試驗,通過設備應用,對國產(chǎn)數(shù)控系統(tǒng)與進口數(shù)控系統(tǒng)進行了對比驗證,完成了機床箱體類零件的多品種、變批量的柔性、高效、高精和混流加工的生產(chǎn)示范和應用驗證。
2.基于開放式數(shù)控系統(tǒng)的FMS集成控制技術
開展了基于開放式數(shù)控系統(tǒng)的FMS 集成控制技術的研究,針對兩套FMS,分別組成了4臺共計8臺的臥式加工中心。針對分別以國產(chǎn)數(shù)控系統(tǒng)和進口數(shù)控系統(tǒng)為控制平臺的兩條機床箱體類零件精密柔性制造系統(tǒng),完成了電氣控制系統(tǒng)的開發(fā)設計、制造、調(diào)試改進、技術驗證、車間應用以及對比測試和驗證等工作。建成了FMS80和FMS63柔性制造系統(tǒng),實現(xiàn)了多品種箱體類零件的單件或批量的柔性、高效、高精加工示范應用。
(1)提出了一套以臥式加工中心為主體,含多托板庫物流自動搬運、計算機總控系統(tǒng)和電氣控制系統(tǒng)在內(nèi)的集成方案;實施建設了基于以太網(wǎng)及現(xiàn)場總線技術的分布式網(wǎng)絡系統(tǒng),實現(xiàn)了對FMS 運行狀態(tài)信息的遠程實時采集和在線監(jiān)測。
(2)形成了具有自主知識產(chǎn)權和寧江特色的,采用計算機軟件技術、自動控制技術、網(wǎng)絡信息化技術和開放式數(shù)控系統(tǒng)應用技術平臺開發(fā)的機床箱體類零件的管理系統(tǒng)控制軟件,用于柔性制造系統(tǒng)的控制和管理。該軟件具有效率優(yōu)先、先進先出、急事先辦、安全高效、高柔性并行及采用混流工藝的FMS 無人化自動調(diào)度加工的特點。
(3)集成開發(fā)了以國產(chǎn)HNC8數(shù)控系統(tǒng)為控制平臺的FMS63柔性制造系統(tǒng),圍繞集成特點和性能,開展了進口數(shù)控系統(tǒng)與國產(chǎn)數(shù)控系統(tǒng)的對比研究,將國產(chǎn)FMS63柔性制造系統(tǒng)實際應用于機床箱體類零件的柔性化批量制造中。
3.基于國產(chǎn)數(shù)控系統(tǒng)的FMS應用技術研究
實現(xiàn)了基于華中8型數(shù)控系統(tǒng)的功能擴展及基于NCUC-BUS總線的控制、物流和信息的網(wǎng)絡融合;實現(xiàn)了FMS多個數(shù)控系統(tǒng)的分布與協(xié)同控制;實現(xiàn)了刀具自動識別、監(jiān)測及自動換刀的功能;完成了綜合精度測量技術研究;完成了物流布局、節(jié)拍、流程和邏輯控制的研究;實現(xiàn)了托盤編碼及自動識別等功能;實現(xiàn)了物流子系統(tǒng)的安全控制;實現(xiàn)了網(wǎng)絡化作業(yè)計劃管理及智能調(diào)度;完成了機床箱體零件的在線檢測測量;實現(xiàn)了精密臥式加工中心監(jiān)控的功能。
(1)對比進口數(shù)控系統(tǒng)的功能,開展了基于HNC8型數(shù)控系統(tǒng)的功能擴展研究,實現(xiàn)了國產(chǎn)數(shù)控系統(tǒng)在柔性制造系統(tǒng)中的首次應用,以及國產(chǎn)FMS63柔性制造系統(tǒng)主機及物流的集成控制。
(2)開發(fā)了基于國產(chǎn)數(shù)控系統(tǒng)的物流控制系統(tǒng),節(jié)拍、精度控制及流程邏輯控制技術,隨行托盤自動識別技術和物流系統(tǒng)安全控制技術。
(3)實現(xiàn)了多個數(shù)控系統(tǒng)的分布式管理與協(xié)同控制,包括主控PC對數(shù)控系統(tǒng)的分布式管理及物流車對數(shù)控系統(tǒng)的協(xié)同控制。
(4)基于對NCUC-BUS 總線的數(shù)控、物流和信息3個層次網(wǎng)絡融合技術的研究,完成了單個數(shù)控系統(tǒng)的現(xiàn)場總線、以太網(wǎng)集成工作,在單個數(shù)控系統(tǒng)上實現(xiàn)了現(xiàn)場總線與以太網(wǎng)的并行傳輸,現(xiàn)場總線控制周期為1ms,以太網(wǎng)傳輸周期為50ms。完成了多個數(shù)控系統(tǒng)的現(xiàn)場總線、以太網(wǎng)互聯(lián)方案設計。
4.基于國產(chǎn)數(shù)控系統(tǒng)的在線測量與監(jiān)控技術
研究了基于國產(chǎn)數(shù)控系統(tǒng)的刀具在線檢測、工件在線檢測技術,實現(xiàn)了工件、刀具的在線檢測和補償。整個過程在測量軟件的控制下自動完成,避免了人為誤差。
研究了基于國產(chǎn)數(shù)控系統(tǒng)的監(jiān)控技術,實現(xiàn)了零件物流的動態(tài)模擬監(jiān)視,以圖形化的形式顯示機床狀況、加工狀態(tài)和信號數(shù)據(jù)的實時信息;開發(fā)了柔性制造系統(tǒng)的歷史數(shù)據(jù)管理系統(tǒng),以同步記錄柔性制造系統(tǒng)的重要事件,包括機床的報警、托板的物流和設備的在線/離線等,便于歷史追溯和問題分析。
(1)提出了“采用國產(chǎn)精密臥式加工中心作為核心檢測設備,充分利用其精密特點和測量功能,實現(xiàn)FMS的在線測量”的方案。
(2)形成了基于國產(chǎn)數(shù)控系統(tǒng)設備對刀、刀具破損檢測、工件找正、序中測量和首件檢測的解決方案;
(3)開發(fā)了基于國產(chǎn)數(shù)控系統(tǒng)的刀具在線檢測和工件在線檢測技術,實現(xiàn)了工件、刀具的在線檢測與補償,整個過程在測量軟件的控制下自動完成,避免了人為誤差。
(4)開展了基于國產(chǎn)數(shù)控系統(tǒng)的FMS數(shù)據(jù)、信息和視頻的實時監(jiān)控技術研究,實現(xiàn)了數(shù)字與視頻的動態(tài)監(jiān)視與記錄。
(5)開發(fā)了圖形化顯示機床狀況、加工狀態(tài)和信號數(shù)據(jù)的實時信息系統(tǒng);開發(fā)了柔性制造系統(tǒng)的歷史數(shù)據(jù)管理系統(tǒng),可同步記錄柔性制造系統(tǒng)的重要事件,包括機床的報警、托板的物流以及設備的在線/離線等,便于歷史追溯和問題分析;開發(fā)了FMS動態(tài)運動視頻監(jiān)控與存儲系統(tǒng)。
5.柔性制造系統(tǒng)可靠性技術研究
以柔性制造系統(tǒng)(FMS)的可靠性研究為主線,通過對FMS的可靠性進行建模、預計和分配,形成了對FMS可靠性狀況的科學認識。在此基礎上,針對該FMS的典型分系統(tǒng),開展了可靠性技術和可靠性試驗研究,形成了一套相對完整的針對FMS的可靠性研究體系。該體系對理論研究和可靠性試驗進行了有機結(jié)合,以理論指導試驗的制定,又通過試驗結(jié)果確定進一步的試驗方向,不斷循環(huán)改進,使FMS柔性制造系統(tǒng)的可靠性水平顯著提高,最終使該FMS的加工單元THM6380的MTBF超過1500h。
(1)提出了以廣義隨機Petri網(wǎng)對FMS 的可靠性進行建模的構思,以及系統(tǒng)混合可靠性分配方法、FMS 典型分系統(tǒng)的可靠性強化試驗方案和基于任務的FMS可靠性預計模型。
(2)形成了FMS的兩個典型分系統(tǒng)的可靠性強化試驗方案。
(3)建立了表征機床工作狀態(tài)的譜系(零件譜、工況譜、載荷譜、功能譜和故障譜)結(jié)構,以及有軌小車狀態(tài)監(jiān)測與故障診斷系統(tǒng)總體框架。
6.FMS刀具及工裝夾具管理系統(tǒng)
刀具智能管理系統(tǒng)是柔性生產(chǎn)線必備的關鍵模塊之一,特別是對于機械生產(chǎn)車間,刀具、夾具和量具的管理是否合理、科學,在很大程度上決定了柔性生產(chǎn)線的可靠性、柔性程度和生產(chǎn)效率的高低。因此,刀具必須納入企業(yè)的物流和信息流之中,建立完整的、實時的刀具數(shù)據(jù)庫,實現(xiàn)無紙化的刀具管理和信息集成已成為柔性制造的一個重要環(huán)節(jié)。
為此,研究并提出了兩種單元控制系統(tǒng):在線柔性制造系統(tǒng)刀具管理和靜態(tài)刀具管理模型。結(jié)合FMS 生產(chǎn)管理的需要,研究了內(nèi)容中調(diào)度要求的對柔性制造系統(tǒng)的動態(tài)管理;刀具壽命管理:將柔性制造系統(tǒng)上的刀具信息與FMS刀具管理軟件平臺服務器進行共享,對刀具壽命進行實時動態(tài)的管理。
(1)提出了兩種單元控制系統(tǒng):在線FMS刀具管理和靜態(tài)刀具管理模型。
(2)形成了完整、詳細的刀具編碼規(guī)范及編寫方法。
(3)開發(fā)了FMS刀具及工裝夾具管理系統(tǒng)。
(4)提出了JSP綜合刀具流調(diào)度數(shù)學模型。
(5)提出了PSO-BP神經(jīng)網(wǎng)絡預測刀具壽命模型,并對FMS刀具進行了動態(tài)壽命管理。
7. MES無縫集成的FMS應用支撐技術的研究
設計了FMS應用支撐系統(tǒng),連接了企業(yè)上層MIS、ERP和現(xiàn)場柔性線,有效提高了FMS的柔性和生產(chǎn)效率,支持了FMS實現(xiàn)多品種、多工藝的混流生產(chǎn)模式,為精密柔性制造系統(tǒng)提供了應用支撐,為大幅度提高柔性制造系統(tǒng)的綜合性能及運行效率打下了基礎。
(1)提出了FMS信息化管理系統(tǒng)與運行控制系統(tǒng)一體化的思路,并結(jié)合了基于約束理論的排產(chǎn)算法。
(2)實現(xiàn)了FMS多品種、多工藝混流的生產(chǎn)模式。
(3)加強了FMS資源信息的集成化管理,向下實現(xiàn)了與設備層總線技術的實時數(shù)據(jù)采集,向上實現(xiàn)了與MES的無縫接入,從而能夠?qū)F(xiàn)場制造信息實時反饋給企業(yè)級MIS/ERP系統(tǒng),以制定能夠快速響應市場需求的合理生產(chǎn)計劃,有效提高了FMS的柔性和效率。
(4)研究開發(fā)了一套適合國內(nèi)企業(yè)運行和使用的柔性制造系統(tǒng)的運行支撐系統(tǒng)。
8. 精密柔性制造系統(tǒng)綜合性能測評技術與規(guī)范研究
通過對FMS綜合性能指標的評測研究,找出了提高FMS精度穩(wěn)定性和FMS加工效率的有效辦法,有效提高了FMS的柔性和生產(chǎn)效率。重點研究了FMS精度指標集建立技術、FMS精度測試技術和FMS綜合性能評測技術等,為大幅度提高精密柔性制造系統(tǒng)的綜合性能及運行效率打下了基礎。
(1)提出了以球桿儀、激光干涉儀、數(shù)控機床動態(tài)誤差檢測技術和基于機床實時狀態(tài)監(jiān)測的機床動態(tài)精度分析技術為基礎、檢測柔性制造系統(tǒng)設備單元誤差的方法。
(2)形成了針對確定綜合性能指標的數(shù)控機床進行性能測試的規(guī)范。
(3)開發(fā)了數(shù)控機床誤差源分析及精度評價指標集設計技術、柔性制造系統(tǒng)精度指標檢測技術、柔性制造系統(tǒng)加工效率和設備利用率測評技術,以及基于層次分析法的數(shù)控機床精度測評技術。
(4)建立了基于層次分析法的數(shù)控機床綜合性能評價體系。
成果應用及推廣情況
“機床箱體類精密柔性制造系統(tǒng)研發(fā)及示范應用”課題研制的FMS63、FMS80兩條精密柔性制造系統(tǒng),已被普什寧江用于精密箱體零件的加工?,F(xiàn)已實現(xiàn)了8種以上機床箱體類零件的混流加工、4種工藝路線的并行生產(chǎn)以及年產(chǎn)能1200件的驗證;開展了可靠性理論和可靠性方法驗證,對國產(chǎn)數(shù)控系統(tǒng)進行了應用驗證和改進,并與進口數(shù)控系統(tǒng)進行了對比試驗;對FMS應用支撐系統(tǒng)的資源集成管理、生產(chǎn)計劃管理和智能調(diào)度等各項功能進行了驗證,并通過對機床典型箱體類零件的加工及示范應用,形成了FMS應用規(guī)范,為FMS的推廣應用奠定了基礎。
承擔專項課題以來,普什寧江研制完成了近30套柔性制造系統(tǒng),并已應用到機床、汽車、船舶、能源、航空航天和通用機械等重要行業(yè)領域,很好地滿足了用戶的需求,在行業(yè)內(nèi)起到了良好的示范作用。
柔性制造系統(tǒng),尤其是配備國產(chǎn)數(shù)控系統(tǒng)的柔性制造系統(tǒng)的研制,是在“高檔數(shù)控機床與基礎制造裝備”科技重大專項的支持下形成的智能制造裝備,隨著產(chǎn)業(yè)化的進一步推進,將在更多加工領域?qū)崿F(xiàn)少人化、柔性化和智能化的加工,將更快、更好地促進加工制造業(yè)的轉(zhuǎn)型升級。
2016年5月25日,由普什寧江牽頭承擔的“機床箱體類精密柔性制造系統(tǒng)研發(fā)及示范應用”課題通過了任務終驗收。該課題由普什寧江聯(lián)合武漢華中數(shù)控股份有限公司、四川大學和重慶大學共同完成,目標是研制精密柔性制造系統(tǒng),實現(xiàn)多品種箱體類零件的單件或批量的柔性、高效、高精加工,并在機床企業(yè)實現(xiàn)示范應用。
課題從2012年1月開始實施,歷經(jīng)3年多時間,完成了任務書規(guī)定的所有研究內(nèi)容。根據(jù)機床制造企業(yè)提升設備能力、適應機床箱體類零件多品種、變批量、柔性、自動化及智能化加工的需求,該課題設計制造了機床箱體類零件精密柔性制造系統(tǒng),研制出630mm和800㎜規(guī)格(各4 臺)的兩條精密柔性制造系統(tǒng)FMS63和FMS80,其中,F(xiàn)MS80配套進口數(shù)控系統(tǒng),F(xiàn)MS63配套國產(chǎn)數(shù)控系統(tǒng)。兩條精密柔性制造系統(tǒng)的工作臺交換重復定位精度0.002mm,運輸小車快移速度75m/min,精密臥式加工中心THM6380的平均故障間隔時間MTBF為1645.1h。
課題開展了基于國產(chǎn)數(shù)控系統(tǒng)的FMS應用技術、在線測量及監(jiān)控技術、可靠性技術、刀具及工裝夾具管理技術以及基于MES無縫集成的FMS應用支撐技術等技術的研究。建成的兩套 FMS在普什寧江的精密加工事業(yè)部實現(xiàn)了箱體類零件的混流加工,對可靠性理論和方法進行了驗證,并開展了國產(chǎn)數(shù)控系統(tǒng)與進口數(shù)控系統(tǒng)的對比試驗,使國產(chǎn)數(shù)控系統(tǒng)在應用驗證中得到改進。
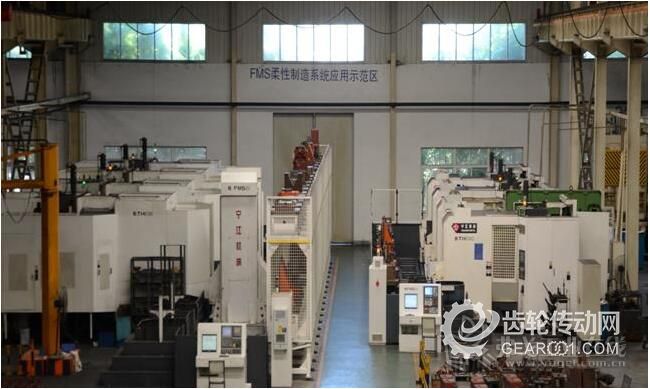
機床箱體類零件精密柔性制造系統(tǒng)FMS80和FMS63的應用現(xiàn)場
產(chǎn)品性能介紹
作為新一代產(chǎn)品,機床箱體類零件精密柔性制造系統(tǒng)FMS具有高柔性、自動化和智能化等特點。
高柔性:研制成功的FMS63和FMS80兩條機床箱體類零件精密柔性制造系統(tǒng),滿足了床身、立柱等8種機床零件、4種工藝路線并行加工的要求,實現(xiàn)了多品種、變批量的混流加工。
自動化:自主研制的RGV輸送小車,集成自動上下料、物流、智能識別及自動控制等技術,具備作業(yè)計劃制定、任務分配、可視化操作和監(jiān)控等功能,能24h連續(xù)工作,并能在無人看管的情況下連續(xù)運行16h。
智能化:自主開發(fā)的總控系統(tǒng),能夠完成對FMS中所有設備的監(jiān)控、計劃管理和零件調(diào)度。向下層,可對物流系統(tǒng)與加工系統(tǒng)進行控制,實現(xiàn)零件的換裝、混流和混工序;向上層,MES系統(tǒng)實現(xiàn)信息的傳遞。通過智能識別、智能調(diào)度等功能,實現(xiàn)零件的柔性化加工。在更換加工對象時,借助零件識別、智能調(diào)度和混流加工技術,無需對FMS進行停機調(diào)試即可實現(xiàn)品種的自動轉(zhuǎn)換,從而實現(xiàn)了基于混流加工的“零”調(diào)整。
表 FMS63和FMS80的主要技術參數(shù)
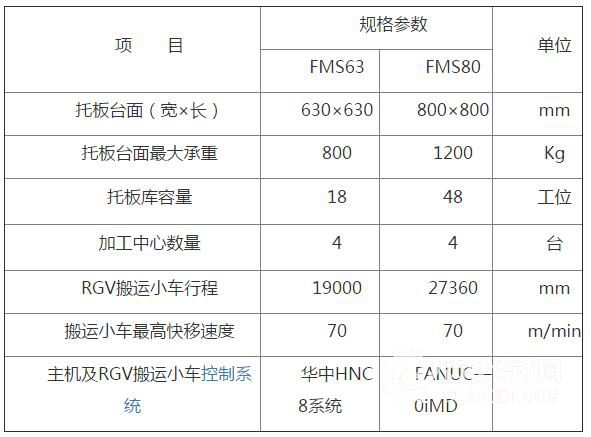
關鍵技術研究
1.典型機床箱體類零件加工工藝技術及FMS系統(tǒng)集成設計
根據(jù)箱體類零件工序比較集中的特點,開展了典型機床箱體類零件工藝需求分析和加工工藝技術研究,完成了機床箱體類精密FMS的總體設計;開展了柔性生產(chǎn)制造技術研究,實現(xiàn)了機床箱體類零件的多品種、小批量的柔性、高效、高精及混流加工的生產(chǎn)示范;建立了加工工藝參數(shù)數(shù)據(jù)庫;開展了機床箱體類零件加工特征自動建模技術的研究;開展了國產(chǎn)數(shù)控刀具切削性能和高效柔性夾具運用的研究。
(1)基于機床箱體類零件加工具有工序長、種類多以及精度高的特點,采用半精加工和精加工的加工中心進行共線配置,同時采用刀具配送、加工程序后臺保障等方式,確定了機床箱體類零件的精密FMS 集成方案,規(guī)劃設計了其物理布局、設備和控制結(jié)構等。
(2)完成了柔性制造系統(tǒng)模塊化、單元化設計;掌握了單機聯(lián)線裝配調(diào)試等技術,形成了相應的工藝和質(zhì)量控制文件;在CAPP平臺基礎上,初步建立了加工工藝參數(shù)數(shù)據(jù)庫 。
(3)實現(xiàn)了刀具、夾具的智能化管理,開展了夾具定位和裝夾等技術的研究和試驗,通過設備應用,對國產(chǎn)數(shù)控系統(tǒng)與進口數(shù)控系統(tǒng)進行了對比驗證,完成了機床箱體類零件的多品種、變批量的柔性、高效、高精和混流加工的生產(chǎn)示范和應用驗證。
2.基于開放式數(shù)控系統(tǒng)的FMS集成控制技術
開展了基于開放式數(shù)控系統(tǒng)的FMS 集成控制技術的研究,針對兩套FMS,分別組成了4臺共計8臺的臥式加工中心。針對分別以國產(chǎn)數(shù)控系統(tǒng)和進口數(shù)控系統(tǒng)為控制平臺的兩條機床箱體類零件精密柔性制造系統(tǒng),完成了電氣控制系統(tǒng)的開發(fā)設計、制造、調(diào)試改進、技術驗證、車間應用以及對比測試和驗證等工作。建成了FMS80和FMS63柔性制造系統(tǒng),實現(xiàn)了多品種箱體類零件的單件或批量的柔性、高效、高精加工示范應用。
(1)提出了一套以臥式加工中心為主體,含多托板庫物流自動搬運、計算機總控系統(tǒng)和電氣控制系統(tǒng)在內(nèi)的集成方案;實施建設了基于以太網(wǎng)及現(xiàn)場總線技術的分布式網(wǎng)絡系統(tǒng),實現(xiàn)了對FMS 運行狀態(tài)信息的遠程實時采集和在線監(jiān)測。
(2)形成了具有自主知識產(chǎn)權和寧江特色的,采用計算機軟件技術、自動控制技術、網(wǎng)絡信息化技術和開放式數(shù)控系統(tǒng)應用技術平臺開發(fā)的機床箱體類零件的管理系統(tǒng)控制軟件,用于柔性制造系統(tǒng)的控制和管理。該軟件具有效率優(yōu)先、先進先出、急事先辦、安全高效、高柔性并行及采用混流工藝的FMS 無人化自動調(diào)度加工的特點。
(3)集成開發(fā)了以國產(chǎn)HNC8數(shù)控系統(tǒng)為控制平臺的FMS63柔性制造系統(tǒng),圍繞集成特點和性能,開展了進口數(shù)控系統(tǒng)與國產(chǎn)數(shù)控系統(tǒng)的對比研究,將國產(chǎn)FMS63柔性制造系統(tǒng)實際應用于機床箱體類零件的柔性化批量制造中。
3.基于國產(chǎn)數(shù)控系統(tǒng)的FMS應用技術研究
實現(xiàn)了基于華中8型數(shù)控系統(tǒng)的功能擴展及基于NCUC-BUS總線的控制、物流和信息的網(wǎng)絡融合;實現(xiàn)了FMS多個數(shù)控系統(tǒng)的分布與協(xié)同控制;實現(xiàn)了刀具自動識別、監(jiān)測及自動換刀的功能;完成了綜合精度測量技術研究;完成了物流布局、節(jié)拍、流程和邏輯控制的研究;實現(xiàn)了托盤編碼及自動識別等功能;實現(xiàn)了物流子系統(tǒng)的安全控制;實現(xiàn)了網(wǎng)絡化作業(yè)計劃管理及智能調(diào)度;完成了機床箱體零件的在線檢測測量;實現(xiàn)了精密臥式加工中心監(jiān)控的功能。
(1)對比進口數(shù)控系統(tǒng)的功能,開展了基于HNC8型數(shù)控系統(tǒng)的功能擴展研究,實現(xiàn)了國產(chǎn)數(shù)控系統(tǒng)在柔性制造系統(tǒng)中的首次應用,以及國產(chǎn)FMS63柔性制造系統(tǒng)主機及物流的集成控制。
(2)開發(fā)了基于國產(chǎn)數(shù)控系統(tǒng)的物流控制系統(tǒng),節(jié)拍、精度控制及流程邏輯控制技術,隨行托盤自動識別技術和物流系統(tǒng)安全控制技術。
(3)實現(xiàn)了多個數(shù)控系統(tǒng)的分布式管理與協(xié)同控制,包括主控PC對數(shù)控系統(tǒng)的分布式管理及物流車對數(shù)控系統(tǒng)的協(xié)同控制。
(4)基于對NCUC-BUS 總線的數(shù)控、物流和信息3個層次網(wǎng)絡融合技術的研究,完成了單個數(shù)控系統(tǒng)的現(xiàn)場總線、以太網(wǎng)集成工作,在單個數(shù)控系統(tǒng)上實現(xiàn)了現(xiàn)場總線與以太網(wǎng)的并行傳輸,現(xiàn)場總線控制周期為1ms,以太網(wǎng)傳輸周期為50ms。完成了多個數(shù)控系統(tǒng)的現(xiàn)場總線、以太網(wǎng)互聯(lián)方案設計。
4.基于國產(chǎn)數(shù)控系統(tǒng)的在線測量與監(jiān)控技術
研究了基于國產(chǎn)數(shù)控系統(tǒng)的刀具在線檢測、工件在線檢測技術,實現(xiàn)了工件、刀具的在線檢測和補償。整個過程在測量軟件的控制下自動完成,避免了人為誤差。
研究了基于國產(chǎn)數(shù)控系統(tǒng)的監(jiān)控技術,實現(xiàn)了零件物流的動態(tài)模擬監(jiān)視,以圖形化的形式顯示機床狀況、加工狀態(tài)和信號數(shù)據(jù)的實時信息;開發(fā)了柔性制造系統(tǒng)的歷史數(shù)據(jù)管理系統(tǒng),以同步記錄柔性制造系統(tǒng)的重要事件,包括機床的報警、托板的物流和設備的在線/離線等,便于歷史追溯和問題分析。
(1)提出了“采用國產(chǎn)精密臥式加工中心作為核心檢測設備,充分利用其精密特點和測量功能,實現(xiàn)FMS的在線測量”的方案。
(2)形成了基于國產(chǎn)數(shù)控系統(tǒng)設備對刀、刀具破損檢測、工件找正、序中測量和首件檢測的解決方案;
(3)開發(fā)了基于國產(chǎn)數(shù)控系統(tǒng)的刀具在線檢測和工件在線檢測技術,實現(xiàn)了工件、刀具的在線檢測與補償,整個過程在測量軟件的控制下自動完成,避免了人為誤差。
(4)開展了基于國產(chǎn)數(shù)控系統(tǒng)的FMS數(shù)據(jù)、信息和視頻的實時監(jiān)控技術研究,實現(xiàn)了數(shù)字與視頻的動態(tài)監(jiān)視與記錄。
(5)開發(fā)了圖形化顯示機床狀況、加工狀態(tài)和信號數(shù)據(jù)的實時信息系統(tǒng);開發(fā)了柔性制造系統(tǒng)的歷史數(shù)據(jù)管理系統(tǒng),可同步記錄柔性制造系統(tǒng)的重要事件,包括機床的報警、托板的物流以及設備的在線/離線等,便于歷史追溯和問題分析;開發(fā)了FMS動態(tài)運動視頻監(jiān)控與存儲系統(tǒng)。
5.柔性制造系統(tǒng)可靠性技術研究
以柔性制造系統(tǒng)(FMS)的可靠性研究為主線,通過對FMS的可靠性進行建模、預計和分配,形成了對FMS可靠性狀況的科學認識。在此基礎上,針對該FMS的典型分系統(tǒng),開展了可靠性技術和可靠性試驗研究,形成了一套相對完整的針對FMS的可靠性研究體系。該體系對理論研究和可靠性試驗進行了有機結(jié)合,以理論指導試驗的制定,又通過試驗結(jié)果確定進一步的試驗方向,不斷循環(huán)改進,使FMS柔性制造系統(tǒng)的可靠性水平顯著提高,最終使該FMS的加工單元THM6380的MTBF超過1500h。
(1)提出了以廣義隨機Petri網(wǎng)對FMS 的可靠性進行建模的構思,以及系統(tǒng)混合可靠性分配方法、FMS 典型分系統(tǒng)的可靠性強化試驗方案和基于任務的FMS可靠性預計模型。
(2)形成了FMS的兩個典型分系統(tǒng)的可靠性強化試驗方案。
(3)建立了表征機床工作狀態(tài)的譜系(零件譜、工況譜、載荷譜、功能譜和故障譜)結(jié)構,以及有軌小車狀態(tài)監(jiān)測與故障診斷系統(tǒng)總體框架。
6.FMS刀具及工裝夾具管理系統(tǒng)
刀具智能管理系統(tǒng)是柔性生產(chǎn)線必備的關鍵模塊之一,特別是對于機械生產(chǎn)車間,刀具、夾具和量具的管理是否合理、科學,在很大程度上決定了柔性生產(chǎn)線的可靠性、柔性程度和生產(chǎn)效率的高低。因此,刀具必須納入企業(yè)的物流和信息流之中,建立完整的、實時的刀具數(shù)據(jù)庫,實現(xiàn)無紙化的刀具管理和信息集成已成為柔性制造的一個重要環(huán)節(jié)。
為此,研究并提出了兩種單元控制系統(tǒng):在線柔性制造系統(tǒng)刀具管理和靜態(tài)刀具管理模型。結(jié)合FMS 生產(chǎn)管理的需要,研究了內(nèi)容中調(diào)度要求的對柔性制造系統(tǒng)的動態(tài)管理;刀具壽命管理:將柔性制造系統(tǒng)上的刀具信息與FMS刀具管理軟件平臺服務器進行共享,對刀具壽命進行實時動態(tài)的管理。
(1)提出了兩種單元控制系統(tǒng):在線FMS刀具管理和靜態(tài)刀具管理模型。
(2)形成了完整、詳細的刀具編碼規(guī)范及編寫方法。
(3)開發(fā)了FMS刀具及工裝夾具管理系統(tǒng)。
(4)提出了JSP綜合刀具流調(diào)度數(shù)學模型。
(5)提出了PSO-BP神經(jīng)網(wǎng)絡預測刀具壽命模型,并對FMS刀具進行了動態(tài)壽命管理。
7. MES無縫集成的FMS應用支撐技術的研究
設計了FMS應用支撐系統(tǒng),連接了企業(yè)上層MIS、ERP和現(xiàn)場柔性線,有效提高了FMS的柔性和生產(chǎn)效率,支持了FMS實現(xiàn)多品種、多工藝的混流生產(chǎn)模式,為精密柔性制造系統(tǒng)提供了應用支撐,為大幅度提高柔性制造系統(tǒng)的綜合性能及運行效率打下了基礎。
(1)提出了FMS信息化管理系統(tǒng)與運行控制系統(tǒng)一體化的思路,并結(jié)合了基于約束理論的排產(chǎn)算法。
(2)實現(xiàn)了FMS多品種、多工藝混流的生產(chǎn)模式。
(3)加強了FMS資源信息的集成化管理,向下實現(xiàn)了與設備層總線技術的實時數(shù)據(jù)采集,向上實現(xiàn)了與MES的無縫接入,從而能夠?qū)F(xiàn)場制造信息實時反饋給企業(yè)級MIS/ERP系統(tǒng),以制定能夠快速響應市場需求的合理生產(chǎn)計劃,有效提高了FMS的柔性和效率。
(4)研究開發(fā)了一套適合國內(nèi)企業(yè)運行和使用的柔性制造系統(tǒng)的運行支撐系統(tǒng)。
8. 精密柔性制造系統(tǒng)綜合性能測評技術與規(guī)范研究
通過對FMS綜合性能指標的評測研究,找出了提高FMS精度穩(wěn)定性和FMS加工效率的有效辦法,有效提高了FMS的柔性和生產(chǎn)效率。重點研究了FMS精度指標集建立技術、FMS精度測試技術和FMS綜合性能評測技術等,為大幅度提高精密柔性制造系統(tǒng)的綜合性能及運行效率打下了基礎。
(1)提出了以球桿儀、激光干涉儀、數(shù)控機床動態(tài)誤差檢測技術和基于機床實時狀態(tài)監(jiān)測的機床動態(tài)精度分析技術為基礎、檢測柔性制造系統(tǒng)設備單元誤差的方法。
(2)形成了針對確定綜合性能指標的數(shù)控機床進行性能測試的規(guī)范。
(3)開發(fā)了數(shù)控機床誤差源分析及精度評價指標集設計技術、柔性制造系統(tǒng)精度指標檢測技術、柔性制造系統(tǒng)加工效率和設備利用率測評技術,以及基于層次分析法的數(shù)控機床精度測評技術。
(4)建立了基于層次分析法的數(shù)控機床綜合性能評價體系。
成果應用及推廣情況
“機床箱體類精密柔性制造系統(tǒng)研發(fā)及示范應用”課題研制的FMS63、FMS80兩條精密柔性制造系統(tǒng),已被普什寧江用于精密箱體零件的加工?,F(xiàn)已實現(xiàn)了8種以上機床箱體類零件的混流加工、4種工藝路線的并行生產(chǎn)以及年產(chǎn)能1200件的驗證;開展了可靠性理論和可靠性方法驗證,對國產(chǎn)數(shù)控系統(tǒng)進行了應用驗證和改進,并與進口數(shù)控系統(tǒng)進行了對比試驗;對FMS應用支撐系統(tǒng)的資源集成管理、生產(chǎn)計劃管理和智能調(diào)度等各項功能進行了驗證,并通過對機床典型箱體類零件的加工及示范應用,形成了FMS應用規(guī)范,為FMS的推廣應用奠定了基礎。
承擔專項課題以來,普什寧江研制完成了近30套柔性制造系統(tǒng),并已應用到機床、汽車、船舶、能源、航空航天和通用機械等重要行業(yè)領域,很好地滿足了用戶的需求,在行業(yè)內(nèi)起到了良好的示范作用。
柔性制造系統(tǒng),尤其是配備國產(chǎn)數(shù)控系統(tǒng)的柔性制造系統(tǒng)的研制,是在“高檔數(shù)控機床與基礎制造裝備”科技重大專項的支持下形成的智能制造裝備,隨著產(chǎn)業(yè)化的進一步推進,將在更多加工領域?qū)崿F(xiàn)少人化、柔性化和智能化的加工,將更快、更好地促進加工制造業(yè)的轉(zhuǎn)型升級。